- Volumes 84-95 (2024)
-
Volumes 72-83 (2023)
-
Volume 83
Pages 1-258 (December 2023)
-
Volume 82
Pages 1-204 (November 2023)
-
Volume 81
Pages 1-188 (October 2023)
-
Volume 80
Pages 1-202 (September 2023)
-
Volume 79
Pages 1-172 (August 2023)
-
Volume 78
Pages 1-146 (July 2023)
-
Volume 77
Pages 1-152 (June 2023)
-
Volume 76
Pages 1-176 (May 2023)
-
Volume 75
Pages 1-228 (April 2023)
-
Volume 74
Pages 1-200 (March 2023)
-
Volume 73
Pages 1-138 (February 2023)
-
Volume 72
Pages 1-144 (January 2023)
-
Volume 83
-
Volumes 60-71 (2022)
-
Volume 71
Pages 1-108 (December 2022)
-
Volume 70
Pages 1-106 (November 2022)
-
Volume 69
Pages 1-122 (October 2022)
-
Volume 68
Pages 1-124 (September 2022)
-
Volume 67
Pages 1-102 (August 2022)
-
Volume 66
Pages 1-112 (July 2022)
-
Volume 65
Pages 1-138 (June 2022)
-
Volume 64
Pages 1-186 (May 2022)
-
Volume 63
Pages 1-124 (April 2022)
-
Volume 62
Pages 1-104 (March 2022)
-
Volume 61
Pages 1-120 (February 2022)
-
Volume 60
Pages 1-124 (January 2022)
-
Volume 71
- Volumes 54-59 (2021)
- Volumes 48-53 (2020)
- Volumes 42-47 (2019)
- Volumes 36-41 (2018)
- Volumes 30-35 (2017)
- Volumes 24-29 (2016)
- Volumes 18-23 (2015)
- Volumes 12-17 (2014)
- Volume 11 (2013)
- Volume 10 (2012)
- Volume 9 (2011)
- Volume 8 (2010)
- Volume 7 (2009)
- Volume 6 (2008)
- Volume 5 (2007)
- Volume 4 (2006)
- Volume 3 (2005)
- Volume 2 (2004)
- Volume 1 (2003)
► A three-phase CFD model is developed to investigate hydrodynamics, heat transfer and cracking reaction in a heavy oil riser.
► Hydrodynamics, temperature and species concentration exhibit significantly nonuniform behavior in the riser.
► New operating mode is superior to the conventional fluid catalytic cracking process.
This paper presents a computational investigation of hydrodynamics, heat transfer and cracking reaction in a heavy oil riser operated in a novel operating mode of low temperature contact and high catalyst-to-oil ratio. Through incorporating feedstock vaporization and a 12-lump cracking kinetics model, a validated gas–solid flow model has been extended to the analysis of the hydrodynamic and reaction behavior in an industrial riser. The results indicate that the hydrodynamics, temperature and species concentration exhibit significantly nonuniform behavior inside the riser, especially in the atomization nozzle region. The lump concentration profiles along the riser height provide useful information for riser optimization. Compared to conventional fluid catalytic cracking (FCC) process, feedstock conversion and gasoline yield are respectively increased by 1.9 units and 1.0 unit in the new FCC process, the yield of liquefied petroleum gas is increased by about 1.0 unit while dry gas yield is reduced by about 0.3 unit.
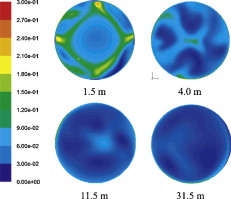