- Volumes 84-95 (2024)
-
Volumes 72-83 (2023)
-
Volume 83
Pages 1-258 (December 2023)
-
Volume 82
Pages 1-204 (November 2023)
-
Volume 81
Pages 1-188 (October 2023)
-
Volume 80
Pages 1-202 (September 2023)
-
Volume 79
Pages 1-172 (August 2023)
-
Volume 78
Pages 1-146 (July 2023)
-
Volume 77
Pages 1-152 (June 2023)
-
Volume 76
Pages 1-176 (May 2023)
-
Volume 75
Pages 1-228 (April 2023)
-
Volume 74
Pages 1-200 (March 2023)
-
Volume 73
Pages 1-138 (February 2023)
-
Volume 72
Pages 1-144 (January 2023)
-
Volume 83
-
Volumes 60-71 (2022)
-
Volume 71
Pages 1-108 (December 2022)
-
Volume 70
Pages 1-106 (November 2022)
-
Volume 69
Pages 1-122 (October 2022)
-
Volume 68
Pages 1-124 (September 2022)
-
Volume 67
Pages 1-102 (August 2022)
-
Volume 66
Pages 1-112 (July 2022)
-
Volume 65
Pages 1-138 (June 2022)
-
Volume 64
Pages 1-186 (May 2022)
-
Volume 63
Pages 1-124 (April 2022)
-
Volume 62
Pages 1-104 (March 2022)
-
Volume 61
Pages 1-120 (February 2022)
-
Volume 60
Pages 1-124 (January 2022)
-
Volume 71
- Volumes 54-59 (2021)
- Volumes 48-53 (2020)
- Volumes 42-47 (2019)
- Volumes 36-41 (2018)
- Volumes 30-35 (2017)
- Volumes 24-29 (2016)
- Volumes 18-23 (2015)
- Volumes 12-17 (2014)
- Volume 11 (2013)
- Volume 10 (2012)
- Volume 9 (2011)
- Volume 8 (2010)
- Volume 7 (2009)
- Volume 6 (2008)
- Volume 5 (2007)
- Volume 4 (2006)
- Volume 3 (2005)
- Volume 2 (2004)
- Volume 1 (2003)
• Seven existing models of blockage boundary for pneumatic conveying were evaluated.
• Existing models provide considerable under- or over-predictions for scale-up.
• New model was developed using Froude number and solid loading ratio.
• It aims at diameter and length scale-up effects.
• New model provides improved prediction accuracy under wide range of scale-up.
This paper presents results of an ongoing investigation into modelling fluidized dense-phase pneumatic conveying of powders. For the reliable design of dense-phase pneumatic conveying systems, an accurate estimation of the blockage boundary condition or the minimum transport velocity requirement is of significant importance. The existing empirical models for fine powder conveying in fluidized dense-phase mode are either based on only a particular pipeline and product or have not been tested for their accuracy under a wide range of scale-up conditions. In this paper, a validated test design procedure has been developed to accurately scale-up the blockage boundary with the help of a modelling format that employs solids loading ratio and Froude number at pipe inlet conditions using conveying data of two different samples of fly ash, electro-static precipitation (ESP) dust and cement (particle densities: 2197–3637 kg/m3; loose poured bulk densities: 634–1070 kg/m3; median size: 7–30 μm). The developed models (in power function format) have been used to predict the blockage boundary for larger diameter and longer pipelines (e.g. models based on 69 mm I.D. × 168 m long pipe have been scaled up to 105 mm I.D. and 554 m length). The predicted blockage boundaries for the scale-up conditions were found to provide better accuracy compared to the existing models.
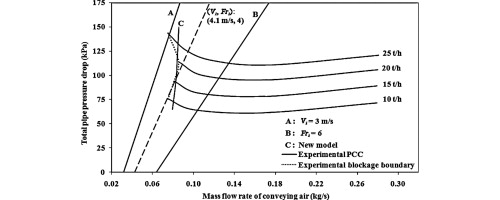