- Volumes 84-95 (2024)
-
Volumes 72-83 (2023)
-
Volume 83
Pages 1-258 (December 2023)
-
Volume 82
Pages 1-204 (November 2023)
-
Volume 81
Pages 1-188 (October 2023)
-
Volume 80
Pages 1-202 (September 2023)
-
Volume 79
Pages 1-172 (August 2023)
-
Volume 78
Pages 1-146 (July 2023)
-
Volume 77
Pages 1-152 (June 2023)
-
Volume 76
Pages 1-176 (May 2023)
-
Volume 75
Pages 1-228 (April 2023)
-
Volume 74
Pages 1-200 (March 2023)
-
Volume 73
Pages 1-138 (February 2023)
-
Volume 72
Pages 1-144 (January 2023)
-
Volume 83
-
Volumes 60-71 (2022)
-
Volume 71
Pages 1-108 (December 2022)
-
Volume 70
Pages 1-106 (November 2022)
-
Volume 69
Pages 1-122 (October 2022)
-
Volume 68
Pages 1-124 (September 2022)
-
Volume 67
Pages 1-102 (August 2022)
-
Volume 66
Pages 1-112 (July 2022)
-
Volume 65
Pages 1-138 (June 2022)
-
Volume 64
Pages 1-186 (May 2022)
-
Volume 63
Pages 1-124 (April 2022)
-
Volume 62
Pages 1-104 (March 2022)
-
Volume 61
Pages 1-120 (February 2022)
-
Volume 60
Pages 1-124 (January 2022)
-
Volume 71
- Volumes 54-59 (2021)
- Volumes 48-53 (2020)
- Volumes 42-47 (2019)
- Volumes 36-41 (2018)
- Volumes 30-35 (2017)
- Volumes 24-29 (2016)
- Volumes 18-23 (2015)
- Volumes 12-17 (2014)
- Volume 11 (2013)
- Volume 10 (2012)
- Volume 9 (2011)
- Volume 8 (2010)
- Volume 7 (2009)
- Volume 6 (2008)
- Volume 5 (2007)
- Volume 4 (2006)
- Volume 3 (2005)
- Volume 2 (2004)
- Volume 1 (2003)
• A detached DEM grid was used to reduce the time needed for CFD–DEM communication.
• The DEM-cells employed a no binary search to decrease the computational effort.
• The DEM-cells were divided into sub-cells to gain further speed up.
• The stiffness of the smallest particles was decreased to allow larger time step.
• Finest particles were eliminated in the simulation.
• DEM comminution simulations can run about 300 times faster.
Size-reduction systems have been extensively used in industry for many years. Nevertheless, reliable engineering tools to be used to predict the comminution of particles are scarce. Computational fluid dynamics (CFD)–discrete element model (DEM) numerical simulation may be used to predict such a complex phenomenon and therefore establish a proper design and optimization model for comminution systems. They may also be used to predict attrition in systems where particle attrition is significant. Therefore, empirical comminution functions (which are applicable for any attrition/comminution process), such as: strength distribution, selection, equivalence, breakage, and fatigue, have been integrated into the three-dimensional CFD–DEM simulation tool. The main drawback of such a design tool is the long computational time required owing to the large number of particles and the minute time-step required to maintain a steady solution while simulating the flow of particulate materials with very fine particles.
The present study developed several methods to accelerate CFD–DEM simulations: reducing the number of operations carried out at the single-particle level, constructing a DEM grid detached from the CFD grid enabling a no binary search, generating a sub-grid within the DEM grid to enable a no binary search for fine particles, and increasing the computational time-step and eliminating the finest particles in the simulation while still tracking their contribution to the process.
The total speedup of the simulation process without the elimination of the finest particles was a factor of about 17. The elimination of the finest particles gave additional speedup of a factor of at least 18. Therefore, the simulation of a grinding process can run at least 300 times faster than the conventional method in which a standard no binary search is employed and the smallest particles are tracked.
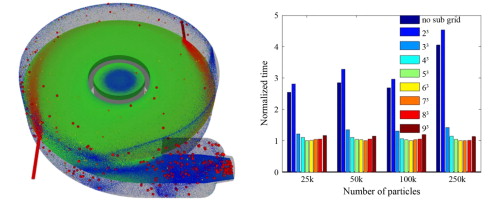