- Volumes 84-95 (2024)
-
Volumes 72-83 (2023)
-
Volume 83
Pages 1-258 (December 2023)
-
Volume 82
Pages 1-204 (November 2023)
-
Volume 81
Pages 1-188 (October 2023)
-
Volume 80
Pages 1-202 (September 2023)
-
Volume 79
Pages 1-172 (August 2023)
-
Volume 78
Pages 1-146 (July 2023)
-
Volume 77
Pages 1-152 (June 2023)
-
Volume 76
Pages 1-176 (May 2023)
-
Volume 75
Pages 1-228 (April 2023)
-
Volume 74
Pages 1-200 (March 2023)
-
Volume 73
Pages 1-138 (February 2023)
-
Volume 72
Pages 1-144 (January 2023)
-
Volume 83
-
Volumes 60-71 (2022)
-
Volume 71
Pages 1-108 (December 2022)
-
Volume 70
Pages 1-106 (November 2022)
-
Volume 69
Pages 1-122 (October 2022)
-
Volume 68
Pages 1-124 (September 2022)
-
Volume 67
Pages 1-102 (August 2022)
-
Volume 66
Pages 1-112 (July 2022)
-
Volume 65
Pages 1-138 (June 2022)
-
Volume 64
Pages 1-186 (May 2022)
-
Volume 63
Pages 1-124 (April 2022)
-
Volume 62
Pages 1-104 (March 2022)
-
Volume 61
Pages 1-120 (February 2022)
-
Volume 60
Pages 1-124 (January 2022)
-
Volume 71
- Volumes 54-59 (2021)
- Volumes 48-53 (2020)
- Volumes 42-47 (2019)
- Volumes 36-41 (2018)
- Volumes 30-35 (2017)
- Volumes 24-29 (2016)
- Volumes 18-23 (2015)
- Volumes 12-17 (2014)
- Volume 11 (2013)
- Volume 10 (2012)
- Volume 9 (2011)
- Volume 8 (2010)
- Volume 7 (2009)
- Volume 6 (2008)
- Volume 5 (2007)
- Volume 4 (2006)
- Volume 3 (2005)
- Volume 2 (2004)
- Volume 1 (2003)
• We model a fluid bed granulator in 3D using the exact geometry of the lab-scale equipment.
• Detailed particle scale simulations allow predicting the strength of product agglomerates.
• DPM helps understanding the impact of process variables on particle dynamics.
• The validated DPM model offer a potential for product design based on targeted process conditions.
Fluidized bed agglomeration is a process commonly used to construct powdered food or pharmaceutical products to improve their instant properties. This works analyzes the influence of a wide range of operating parameters (i.e., fluidization air flow rate, temperature, and liquid injection rate) on growth rate, process stability, and product particle structure. Different granulator configurations (i.e., top spray, Wurster coater, spouted bed) are compared using identical process parameters. The impacts of both process variables and granulator geometry on the fluidization regime, the particle and collision dynamics, and the resulting product structure and corresponding properties are studied in detailed simulations using a discrete particle model (DPM) and lab-scale agglomeration experiments with amorphous dextrose syrup (DE21). The combination of numerical and experimental results allows to correlate the kinetics of micro-scale particle interactions and the final product properties (i.e., agglomerate structure and strength). In conclusion, detailed DPM simulations are proven as a valuable tool for knowledge-based product design.
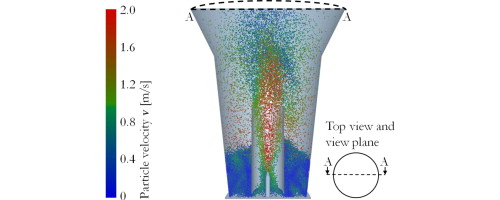
Fluidization; Agglomeration; Discrete element method; Food powder; Collision dynamics