- Volumes 84-95 (2024)
-
Volumes 72-83 (2023)
-
Volume 83
Pages 1-258 (December 2023)
-
Volume 82
Pages 1-204 (November 2023)
-
Volume 81
Pages 1-188 (October 2023)
-
Volume 80
Pages 1-202 (September 2023)
-
Volume 79
Pages 1-172 (August 2023)
-
Volume 78
Pages 1-146 (July 2023)
-
Volume 77
Pages 1-152 (June 2023)
-
Volume 76
Pages 1-176 (May 2023)
-
Volume 75
Pages 1-228 (April 2023)
-
Volume 74
Pages 1-200 (March 2023)
-
Volume 73
Pages 1-138 (February 2023)
-
Volume 72
Pages 1-144 (January 2023)
-
Volume 83
-
Volumes 60-71 (2022)
-
Volume 71
Pages 1-108 (December 2022)
-
Volume 70
Pages 1-106 (November 2022)
-
Volume 69
Pages 1-122 (October 2022)
-
Volume 68
Pages 1-124 (September 2022)
-
Volume 67
Pages 1-102 (August 2022)
-
Volume 66
Pages 1-112 (July 2022)
-
Volume 65
Pages 1-138 (June 2022)
-
Volume 64
Pages 1-186 (May 2022)
-
Volume 63
Pages 1-124 (April 2022)
-
Volume 62
Pages 1-104 (March 2022)
-
Volume 61
Pages 1-120 (February 2022)
-
Volume 60
Pages 1-124 (January 2022)
-
Volume 71
- Volumes 54-59 (2021)
- Volumes 48-53 (2020)
- Volumes 42-47 (2019)
- Volumes 36-41 (2018)
- Volumes 30-35 (2017)
- Volumes 24-29 (2016)
- Volumes 18-23 (2015)
- Volumes 12-17 (2014)
- Volume 11 (2013)
- Volume 10 (2012)
- Volume 9 (2011)
- Volume 8 (2010)
- Volume 7 (2009)
- Volume 6 (2008)
- Volume 5 (2007)
- Volume 4 (2006)
- Volume 3 (2005)
- Volume 2 (2004)
- Volume 1 (2003)
• Edinburgh powder tester (EPT) was used to measure compressibility and caking of detergent powders.
• Measurement results showed excellent reproducibility.
• An EPT test was simulated with DEM using an elasto-plastic adhesive contact model.
• Simulation results showed that the model is able to capture detergent behavior reasonably well.
This paper presents an experimental and numerical study of the packing, compression, and caking behaviour of spray dried detergent (SDD) powders with a two-fold aim: an experimental process of observation and evaluation of the packing, compression and caking behaviour of SDD powders, and a numerical approach based on discrete element modelling (DEM). The mechanical properties, including the stress–strain response and the corresponding porosity change as a function of consolidation stress in a confined cylinder, the stress–strain response during unconfined shearing and the cake strength as a function of consolidation stress, were evaluated and compared for different SDD powders using an extended uniaxial tester (Edinburgh Powder Tester – EPT). The experiments using EPT showed excellent reproducibility in the measurement of packing, compression and caking behaviour and were therefore very useful for describing the handling characteristics of these powdered products including screening new products and different formulations. It was found that the sample with higher moisture had lower bulk porosity but higher compressibility and cake strength. The porosity, compressibility and cake strength were found to vary across different size fractions of the same sample. The larger sieve-cut samples had higher initial bulk porosity, compressibility and cake strength. It is revealed that moisture plays a significant role in packing, compression, and shearing behaviour of the powder. Three-dimensional DEM modelling using a recently developed elasto-plastic adhesive-frictional contact model showed that the contact model is able to capture the detergent behaviour reasonably well and can be used to model complex processes involving these powders.
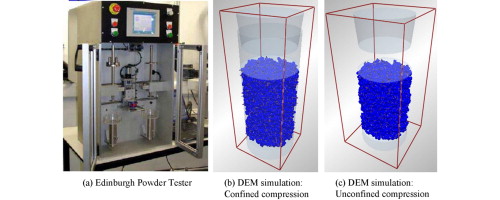