- Volumes 84-95 (2024)
-
Volumes 72-83 (2023)
-
Volume 83
Pages 1-258 (December 2023)
-
Volume 82
Pages 1-204 (November 2023)
-
Volume 81
Pages 1-188 (October 2023)
-
Volume 80
Pages 1-202 (September 2023)
-
Volume 79
Pages 1-172 (August 2023)
-
Volume 78
Pages 1-146 (July 2023)
-
Volume 77
Pages 1-152 (June 2023)
-
Volume 76
Pages 1-176 (May 2023)
-
Volume 75
Pages 1-228 (April 2023)
-
Volume 74
Pages 1-200 (March 2023)
-
Volume 73
Pages 1-138 (February 2023)
-
Volume 72
Pages 1-144 (January 2023)
-
Volume 83
-
Volumes 60-71 (2022)
-
Volume 71
Pages 1-108 (December 2022)
-
Volume 70
Pages 1-106 (November 2022)
-
Volume 69
Pages 1-122 (October 2022)
-
Volume 68
Pages 1-124 (September 2022)
-
Volume 67
Pages 1-102 (August 2022)
-
Volume 66
Pages 1-112 (July 2022)
-
Volume 65
Pages 1-138 (June 2022)
-
Volume 64
Pages 1-186 (May 2022)
-
Volume 63
Pages 1-124 (April 2022)
-
Volume 62
Pages 1-104 (March 2022)
-
Volume 61
Pages 1-120 (February 2022)
-
Volume 60
Pages 1-124 (January 2022)
-
Volume 71
- Volumes 54-59 (2021)
- Volumes 48-53 (2020)
- Volumes 42-47 (2019)
- Volumes 36-41 (2018)
- Volumes 30-35 (2017)
- Volumes 24-29 (2016)
- Volumes 18-23 (2015)
- Volumes 12-17 (2014)
- Volume 11 (2013)
- Volume 10 (2012)
- Volume 9 (2011)
- Volume 8 (2010)
- Volume 7 (2009)
- Volume 6 (2008)
- Volume 5 (2007)
- Volume 4 (2006)
- Volume 3 (2005)
- Volume 2 (2004)
- Volume 1 (2003)
Surya Deb, Danesh K. Tafti *
• 2D and 3D simulations were performed and validated with experiment for a multiple jet fluidized bed.
• 3D simulations could predict the bubble characteristics far away from the distributor plate.
• 2D simulations show good validation with experiment closer to the distributor plate.
• A full 3D simulation with time averaged results for multiple jets has not been published before.
Fluidized beds with multiple jets have widespread industrial applications. The objective of this paper is to investigate the jet interactions and hydrodynamics of a fluidized bed with multiple jets. Discrete element modeling coupled with in-house CFD code GenIDLEST has been used to simulate a bed with nine jets. The results are compared with published experiments. Mono dispersed particles of size 550 μm are used with 1.4 times the minimum fluidization velocity of the particles. Both two and three dimensional computations have been performed. To the best of our knowledge, the results presented in this paper are the first full 3D simulations of a fluidized bed performed with multiple jets. Discrepancies between the experiment and simulations are discussed in the context of the dimensionality of the simulations. The 2D solid fraction profile compares well with the experiment close to the distributor plate. At higher heights, the 2D simulation over-predicts the solid fraction profiles near the walls. The 3D simulation on the other hand is better able to capture the solid fraction profile higher up in the bed compared to that near the distributor plate. Similarly, the normalized particle velocities and the particle fluxes compare well with the experiment closer to the distributor plate for the 2D simulation and the freeboard for the 3D simulation, respectively. A lower expanded bed height is predicted in the 2D simulation compared to the 3D simulation and the experiment. The results obtained from DEM computations show that a 2D simulation can be used to capture essential jetting trends near the distributor plate regions, whereas a full scale 3D simulation is needed to capture the bubbles near the freeboard regions. These serve as validations for the experiment and help us understand the complex jet interaction and solid circulation patterns in a multiple jet fluidized bed system.
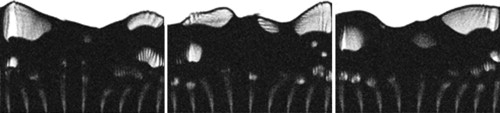