- Volumes 84-95 (2024)
-
Volumes 72-83 (2023)
-
Volume 83
Pages 1-258 (December 2023)
-
Volume 82
Pages 1-204 (November 2023)
-
Volume 81
Pages 1-188 (October 2023)
-
Volume 80
Pages 1-202 (September 2023)
-
Volume 79
Pages 1-172 (August 2023)
-
Volume 78
Pages 1-146 (July 2023)
-
Volume 77
Pages 1-152 (June 2023)
-
Volume 76
Pages 1-176 (May 2023)
-
Volume 75
Pages 1-228 (April 2023)
-
Volume 74
Pages 1-200 (March 2023)
-
Volume 73
Pages 1-138 (February 2023)
-
Volume 72
Pages 1-144 (January 2023)
-
Volume 83
-
Volumes 60-71 (2022)
-
Volume 71
Pages 1-108 (December 2022)
-
Volume 70
Pages 1-106 (November 2022)
-
Volume 69
Pages 1-122 (October 2022)
-
Volume 68
Pages 1-124 (September 2022)
-
Volume 67
Pages 1-102 (August 2022)
-
Volume 66
Pages 1-112 (July 2022)
-
Volume 65
Pages 1-138 (June 2022)
-
Volume 64
Pages 1-186 (May 2022)
-
Volume 63
Pages 1-124 (April 2022)
-
Volume 62
Pages 1-104 (March 2022)
-
Volume 61
Pages 1-120 (February 2022)
-
Volume 60
Pages 1-124 (January 2022)
-
Volume 71
- Volumes 54-59 (2021)
- Volumes 48-53 (2020)
- Volumes 42-47 (2019)
- Volumes 36-41 (2018)
- Volumes 30-35 (2017)
- Volumes 24-29 (2016)
- Volumes 18-23 (2015)
- Volumes 12-17 (2014)
- Volume 11 (2013)
- Volume 10 (2012)
- Volume 9 (2011)
- Volume 8 (2010)
- Volume 7 (2009)
- Volume 6 (2008)
- Volume 5 (2007)
- Volume 4 (2006)
- Volume 3 (2005)
- Volume 2 (2004)
- Volume 1 (2003)
• Four types of coating materials were investigated to coat urea granules.
• A gypsum-sulfur-based material was considered to best reduce dissolution rate of urea.
• Increasing the coating thickness increased considerably the crushing strength of coated granules.
• Sieving coating materials and adding wax led to an increase in efficiency of coated urea granules.
Approximately 70% of the applied urea fertilizer may be lost into the environment. This loss is due to leaching, decomposition and ammonium volatilization in soil, water and air. Through coating, the slow release technology can be used to reduce losses and to increase the fertilizer efficiency. Sulfur has been used as a coating material, but the coating cracks easily because of its friability, sometimes being peeled off from the urea surface. In this study, four types of materials, namely, gypsum, cement, sulfur and zeolite, were mixed and used as coating materials to search for the most effective and cheap coating materials. The primary reasons for selecting these materials were improving fruit quality and preventing plant diseases, providing a plant nutrient, increasing soil fertility and water retention. The materials were also selected based on their availability, processiblity and price. The effects of the coating materials, thickness, drying time, sieving and sealant on the crushing strength and dissolution rate of urea were investigated. Coated urea with the same proportion of gypsum–sulfur exhibited high crushing strength and lower dissolution rate. However, the performance was further enhanced by applying molten paraffin wax on the hot urea surface. SEM images demonstrated that the micro-structure of gypsum–sulfur coated urea after sieving resulted in a smoother coated layer. The efficiency of the coated urea was improved by 26% using gypsum–sulfur (20% total coating), 3% paraffin wax and sieving the coating materials before application.
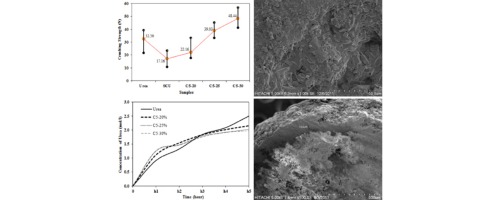