- Volumes 84-95 (2024)
-
Volumes 72-83 (2023)
-
Volume 83
Pages 1-258 (December 2023)
-
Volume 82
Pages 1-204 (November 2023)
-
Volume 81
Pages 1-188 (October 2023)
-
Volume 80
Pages 1-202 (September 2023)
-
Volume 79
Pages 1-172 (August 2023)
-
Volume 78
Pages 1-146 (July 2023)
-
Volume 77
Pages 1-152 (June 2023)
-
Volume 76
Pages 1-176 (May 2023)
-
Volume 75
Pages 1-228 (April 2023)
-
Volume 74
Pages 1-200 (March 2023)
-
Volume 73
Pages 1-138 (February 2023)
-
Volume 72
Pages 1-144 (January 2023)
-
Volume 83
-
Volumes 60-71 (2022)
-
Volume 71
Pages 1-108 (December 2022)
-
Volume 70
Pages 1-106 (November 2022)
-
Volume 69
Pages 1-122 (October 2022)
-
Volume 68
Pages 1-124 (September 2022)
-
Volume 67
Pages 1-102 (August 2022)
-
Volume 66
Pages 1-112 (July 2022)
-
Volume 65
Pages 1-138 (June 2022)
-
Volume 64
Pages 1-186 (May 2022)
-
Volume 63
Pages 1-124 (April 2022)
-
Volume 62
Pages 1-104 (March 2022)
-
Volume 61
Pages 1-120 (February 2022)
-
Volume 60
Pages 1-124 (January 2022)
-
Volume 71
- Volumes 54-59 (2021)
- Volumes 48-53 (2020)
- Volumes 42-47 (2019)
- Volumes 36-41 (2018)
- Volumes 30-35 (2017)
- Volumes 24-29 (2016)
- Volumes 18-23 (2015)
- Volumes 12-17 (2014)
- Volume 11 (2013)
- Volume 10 (2012)
- Volume 9 (2011)
- Volume 8 (2010)
- Volume 7 (2009)
- Volume 6 (2008)
- Volume 5 (2007)
- Volume 4 (2006)
- Volume 3 (2005)
- Volume 2 (2004)
- Volume 1 (2003)
• Coarse mesh simulations for large circulating fluidized bed furnace were performed.
• Macroscopic drag model provided a limit for coarse mesh closure for this study.
• Applied subgrid-scale drag models show improvement over Ergun/Wen–Yu model.
• Approximation of one particle size in wide particle size distribution is difficult.
Mesoscale flow structures such as clusters and streamers of particles are characteristic features of gas–solid flow in fluidized beds. Numerical simulations of gas–solid flows for industrial-scale fluidized beds are often performed using the Eulerian description of phases. An accurate prediction of this type of flow structure using the Eulerian modeling approach requires a sufficiently fine mesh resolution. Because of the long computational time required when using fine meshes, simulations of industrial-sized units are usually conducted using coarse meshes, which cannot resolve the mesoscale flow structures. This leads to an overestimation of the gas–solid drag force and a false prediction of the flow field. For these cases, a correction must be formulated for the gas–solid drag. We have simulated a large-scale circulating fluidized bed furnace using different gas–solid drag models and compared the model results with measurements.
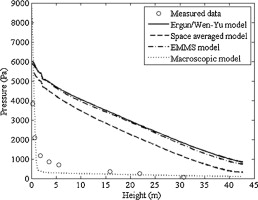