- Volumes 84-95 (2024)
-
Volumes 72-83 (2023)
-
Volume 83
Pages 1-258 (December 2023)
-
Volume 82
Pages 1-204 (November 2023)
-
Volume 81
Pages 1-188 (October 2023)
-
Volume 80
Pages 1-202 (September 2023)
-
Volume 79
Pages 1-172 (August 2023)
-
Volume 78
Pages 1-146 (July 2023)
-
Volume 77
Pages 1-152 (June 2023)
-
Volume 76
Pages 1-176 (May 2023)
-
Volume 75
Pages 1-228 (April 2023)
-
Volume 74
Pages 1-200 (March 2023)
-
Volume 73
Pages 1-138 (February 2023)
-
Volume 72
Pages 1-144 (January 2023)
-
Volume 83
-
Volumes 60-71 (2022)
-
Volume 71
Pages 1-108 (December 2022)
-
Volume 70
Pages 1-106 (November 2022)
-
Volume 69
Pages 1-122 (October 2022)
-
Volume 68
Pages 1-124 (September 2022)
-
Volume 67
Pages 1-102 (August 2022)
-
Volume 66
Pages 1-112 (July 2022)
-
Volume 65
Pages 1-138 (June 2022)
-
Volume 64
Pages 1-186 (May 2022)
-
Volume 63
Pages 1-124 (April 2022)
-
Volume 62
Pages 1-104 (March 2022)
-
Volume 61
Pages 1-120 (February 2022)
-
Volume 60
Pages 1-124 (January 2022)
-
Volume 71
- Volumes 54-59 (2021)
- Volumes 48-53 (2020)
- Volumes 42-47 (2019)
- Volumes 36-41 (2018)
- Volumes 30-35 (2017)
- Volumes 24-29 (2016)
- Volumes 18-23 (2015)
- Volumes 12-17 (2014)
- Volume 11 (2013)
- Volume 10 (2012)
- Volume 9 (2011)
- Volume 8 (2010)
- Volume 7 (2009)
- Volume 6 (2008)
- Volume 5 (2007)
- Volume 4 (2006)
- Volume 3 (2005)
- Volume 2 (2004)
- Volume 1 (2003)
• Changes in particle structure of milk powder during post-crystallization was investigated.
• The sorption and desorption of moisture into or from the surface layer played a significant role.
• A multi-component diffusion model was used to mimic experimental observations.
• Two types of particle structures were observed depending on post-crystallization conditions.
• Model predicted particle structures agreed qualitatively with experimental data.
The formation of heterogeneous particle structure in skim milk powder has been investigated in a post-crystallization facility using experimental and a mathematical model. Various processing conditions were used to produce these heterogeneous structures. The experimental process parameters were used as initial and boundary conditions for the model. The modelled data agreed well with the experimental data. The experimental and modelling results show that the powder processed at high water activity (aw = 0.7) with low initial moisture content ( = 0.01 kg/kg) developed a crystalline surface layer while the core of the particle remained amorphous. This structure is referred to as an egg-shell structure. The powder that was processed at low water activity (aw = 0.1) with high initial moisture content (
= 0.2 kg/kg) developed a crystalline core while the surface of the particle remained amorphous. This structure is referred to as an egg-yolk structure. Understanding the dependency of particle microstructures on the processing conditions could be useful when developing procedures to control the drying equipment because the particle microstructure affects the physicochemical properties of the powder and potential applications and behaviour of the powder.
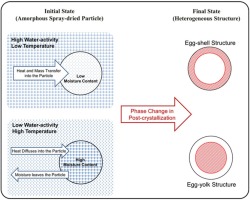