- Volumes 84-95 (2024)
-
Volumes 72-83 (2023)
-
Volume 83
Pages 1-258 (December 2023)
-
Volume 82
Pages 1-204 (November 2023)
-
Volume 81
Pages 1-188 (October 2023)
-
Volume 80
Pages 1-202 (September 2023)
-
Volume 79
Pages 1-172 (August 2023)
-
Volume 78
Pages 1-146 (July 2023)
-
Volume 77
Pages 1-152 (June 2023)
-
Volume 76
Pages 1-176 (May 2023)
-
Volume 75
Pages 1-228 (April 2023)
-
Volume 74
Pages 1-200 (March 2023)
-
Volume 73
Pages 1-138 (February 2023)
-
Volume 72
Pages 1-144 (January 2023)
-
Volume 83
-
Volumes 60-71 (2022)
-
Volume 71
Pages 1-108 (December 2022)
-
Volume 70
Pages 1-106 (November 2022)
-
Volume 69
Pages 1-122 (October 2022)
-
Volume 68
Pages 1-124 (September 2022)
-
Volume 67
Pages 1-102 (August 2022)
-
Volume 66
Pages 1-112 (July 2022)
-
Volume 65
Pages 1-138 (June 2022)
-
Volume 64
Pages 1-186 (May 2022)
-
Volume 63
Pages 1-124 (April 2022)
-
Volume 62
Pages 1-104 (March 2022)
-
Volume 61
Pages 1-120 (February 2022)
-
Volume 60
Pages 1-124 (January 2022)
-
Volume 71
- Volumes 54-59 (2021)
- Volumes 48-53 (2020)
- Volumes 42-47 (2019)
- Volumes 36-41 (2018)
- Volumes 30-35 (2017)
- Volumes 24-29 (2016)
- Volumes 18-23 (2015)
- Volumes 12-17 (2014)
- Volume 11 (2013)
- Volume 10 (2012)
- Volume 9 (2011)
- Volume 8 (2010)
- Volume 7 (2009)
- Volume 6 (2008)
- Volume 5 (2007)
- Volume 4 (2006)
- Volume 3 (2005)
- Volume 2 (2004)
- Volume 1 (2003)
• Energy dissipation induced by particle damping in centrifugal field was performed using DEM.
• Dependence of damping effect on loading, rotation speed and particle filling rate was analyzed.
• A proper particle filling rate could result in an optimal damping effect.
As a passive means of vibration reduction, particle damping is mainly applied to the horizontal or vertical steady field. However, it is seldom applied to centrifugal fields. Under high speed and heavy loading, the vibration of tooth surfaces of gear transmissions becomes more severe shortening gear service life and augmenting noise. Under centrifugal loading, the particle system exhibits different characteristics, for example, particles are extruded at the end farthest from the center. We investigated gears with drilled via holes filled with damping particles. Using the discrete-element method, we developed an energy dissipation model for the particle system accounting for friction and inelastic collisions. Energy dissipation and damping characteristics of this system were analyzed. Experiments were also conducted with the gear system having different particle filling rates. The results show that this filling rate is an important parameter associated with particle damping in a centrifugal field. An unsuitable filling rate would significantly reduce damping effectiveness. With changes in rotation speed and load, the gear transmission system has different optimal filling rates. The results provide guidelines for the application of particle damping in centrifugal fields of gear transmissions.
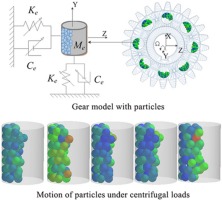