- Volumes 84-95 (2024)
-
Volumes 72-83 (2023)
-
Volume 83
Pages 1-258 (December 2023)
-
Volume 82
Pages 1-204 (November 2023)
-
Volume 81
Pages 1-188 (October 2023)
-
Volume 80
Pages 1-202 (September 2023)
-
Volume 79
Pages 1-172 (August 2023)
-
Volume 78
Pages 1-146 (July 2023)
-
Volume 77
Pages 1-152 (June 2023)
-
Volume 76
Pages 1-176 (May 2023)
-
Volume 75
Pages 1-228 (April 2023)
-
Volume 74
Pages 1-200 (March 2023)
-
Volume 73
Pages 1-138 (February 2023)
-
Volume 72
Pages 1-144 (January 2023)
-
Volume 83
-
Volumes 60-71 (2022)
-
Volume 71
Pages 1-108 (December 2022)
-
Volume 70
Pages 1-106 (November 2022)
-
Volume 69
Pages 1-122 (October 2022)
-
Volume 68
Pages 1-124 (September 2022)
-
Volume 67
Pages 1-102 (August 2022)
-
Volume 66
Pages 1-112 (July 2022)
-
Volume 65
Pages 1-138 (June 2022)
-
Volume 64
Pages 1-186 (May 2022)
-
Volume 63
Pages 1-124 (April 2022)
-
Volume 62
Pages 1-104 (March 2022)
-
Volume 61
Pages 1-120 (February 2022)
-
Volume 60
Pages 1-124 (January 2022)
-
Volume 71
- Volumes 54-59 (2021)
- Volumes 48-53 (2020)
- Volumes 42-47 (2019)
- Volumes 36-41 (2018)
- Volumes 30-35 (2017)
- Volumes 24-29 (2016)
- Volumes 18-23 (2015)
- Volumes 12-17 (2014)
- Volume 11 (2013)
- Volume 10 (2012)
- Volume 9 (2011)
- Volume 8 (2010)
- Volume 7 (2009)
- Volume 6 (2008)
- Volume 5 (2007)
- Volume 4 (2006)
- Volume 3 (2005)
- Volume 2 (2004)
- Volume 1 (2003)
• A model study of airborne wear particle transport (<100 nm) in an enclosed space was presented.
• The flow pattern inside the chamber was significantly influenced by the disc rotation.
• A very slow growth of particle concentration away from the outlet side was observed.
• The estimated particle loss rate at the outlet was about 70% after 240 s.
• Numerical simulation results were validated against laboratory measurements.
Laboratory measurements of airborne particles from sliding contacts are often performed using a tribometer located in a ventilation chamber. Although knowledge of particle transport behavior inside the chamber is required because it can influence the analysis of measurements, this knowledge is lacking. A numerical model was built based on the same geometry as a pin-on-disc measurement system to explain particle transport behavior inside the chamber and to determine the deviation between real amounts of generated and measured particles at the outlet. The effect of controlled flow conditions on the airflow pattern and particle transport inside the chamber was studied for different experimental conditions. Calculations show that a complex airflow pattern is formed by the spinning disc, and that it differs for each rotational speed. Simulation results reveal that particle transport in the chamber is governed mainly by the airflow pattern. The deposition velocity in the chamber was estimated and the possibility that part of the generated particles would remain in the chamber was studied. This led to an approximate estimation of particle loss rate. A comparison between experimental and simulated results with respect to the particle mass flow rate close to the outlet yields a reference factor of 0.7, which provides an indication of the difference between measured and real values.
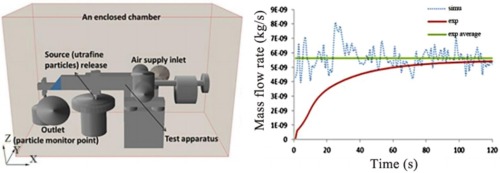