- Volumes 84-95 (2024)
-
Volumes 72-83 (2023)
-
Volume 83
Pages 1-258 (December 2023)
-
Volume 82
Pages 1-204 (November 2023)
-
Volume 81
Pages 1-188 (October 2023)
-
Volume 80
Pages 1-202 (September 2023)
-
Volume 79
Pages 1-172 (August 2023)
-
Volume 78
Pages 1-146 (July 2023)
-
Volume 77
Pages 1-152 (June 2023)
-
Volume 76
Pages 1-176 (May 2023)
-
Volume 75
Pages 1-228 (April 2023)
-
Volume 74
Pages 1-200 (March 2023)
-
Volume 73
Pages 1-138 (February 2023)
-
Volume 72
Pages 1-144 (January 2023)
-
Volume 83
-
Volumes 60-71 (2022)
-
Volume 71
Pages 1-108 (December 2022)
-
Volume 70
Pages 1-106 (November 2022)
-
Volume 69
Pages 1-122 (October 2022)
-
Volume 68
Pages 1-124 (September 2022)
-
Volume 67
Pages 1-102 (August 2022)
-
Volume 66
Pages 1-112 (July 2022)
-
Volume 65
Pages 1-138 (June 2022)
-
Volume 64
Pages 1-186 (May 2022)
-
Volume 63
Pages 1-124 (April 2022)
-
Volume 62
Pages 1-104 (March 2022)
-
Volume 61
Pages 1-120 (February 2022)
-
Volume 60
Pages 1-124 (January 2022)
-
Volume 71
- Volumes 54-59 (2021)
- Volumes 48-53 (2020)
- Volumes 42-47 (2019)
- Volumes 36-41 (2018)
- Volumes 30-35 (2017)
- Volumes 24-29 (2016)
- Volumes 18-23 (2015)
- Volumes 12-17 (2014)
- Volume 11 (2013)
- Volume 10 (2012)
- Volume 9 (2011)
- Volume 8 (2010)
- Volume 7 (2009)
- Volume 6 (2008)
- Volume 5 (2007)
- Volume 4 (2006)
- Volume 3 (2005)
- Volume 2 (2004)
- Volume 1 (2003)
• Particle transport phenomena in a pilot CFB was accurately predicted using a looping procedure.
• New calculation technique was proposed for modeling fluidization process within close loop of CFB.
• Hybrid Euler–Lagrange approach was applied for modeling particle transport within the CFB boiler.
Numerical modeling of a large scale circulating fluidized bed (CFB) imposes many complexities and difficulties. Presence of a dense solid phase, a variety of spatial and time scales as well as complex model geometries requires advanced numerical techniques. Moreover, the appropriate selection of a numerical model capable of solving granular flow, and geometrical model simplification can have a huge impact on the predicted flow field within the CFB boiler. In order to reduce the cost of the numerical simulations, the complex CFB boiler geometry is reduced to that of the combustion chamber. However, a question arises as to how much one can simplify the geometrical model without losing accuracy of numerical simulations. To accurately predict the gas–solid and solid–solid mixing processes within subsequent sections of the CFB boiler (combustion chamber, solid separator, drain section), a complete 3D geometrical model should be used. Nevertheless, because of the presence of various spatial and temporal scales within subsequent boiler sections, the complete model of the 3D CFB boiler is practically unrealizable in numerical simulations. To resolve the aforementioned problems, this paper describes a new approach that can be applied for complete boiler modeling. The proposed approach enables complex particle transport and gas flow problems within each of the boiler sections to be accurately resolved. It has been achieved by dividing the CFB boiler geometry into several submodels, where different numerical approaches can be used to resolve gas–solid transport. The interactions between computational domains were taken into account by connecting the inlets/outlets of each section using a set of user-defined functions implemented into the solution procedure. The proposed approach ensures stable and accurate solution within the separated boiler zones.
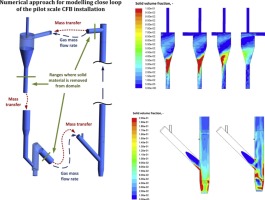