- Volumes 84-95 (2024)
-
Volumes 72-83 (2023)
-
Volume 83
Pages 1-258 (December 2023)
-
Volume 82
Pages 1-204 (November 2023)
-
Volume 81
Pages 1-188 (October 2023)
-
Volume 80
Pages 1-202 (September 2023)
-
Volume 79
Pages 1-172 (August 2023)
-
Volume 78
Pages 1-146 (July 2023)
-
Volume 77
Pages 1-152 (June 2023)
-
Volume 76
Pages 1-176 (May 2023)
-
Volume 75
Pages 1-228 (April 2023)
-
Volume 74
Pages 1-200 (March 2023)
-
Volume 73
Pages 1-138 (February 2023)
-
Volume 72
Pages 1-144 (January 2023)
-
Volume 83
-
Volumes 60-71 (2022)
-
Volume 71
Pages 1-108 (December 2022)
-
Volume 70
Pages 1-106 (November 2022)
-
Volume 69
Pages 1-122 (October 2022)
-
Volume 68
Pages 1-124 (September 2022)
-
Volume 67
Pages 1-102 (August 2022)
-
Volume 66
Pages 1-112 (July 2022)
-
Volume 65
Pages 1-138 (June 2022)
-
Volume 64
Pages 1-186 (May 2022)
-
Volume 63
Pages 1-124 (April 2022)
-
Volume 62
Pages 1-104 (March 2022)
-
Volume 61
Pages 1-120 (February 2022)
-
Volume 60
Pages 1-124 (January 2022)
-
Volume 71
- Volumes 54-59 (2021)
- Volumes 48-53 (2020)
- Volumes 42-47 (2019)
- Volumes 36-41 (2018)
- Volumes 30-35 (2017)
- Volumes 24-29 (2016)
- Volumes 18-23 (2015)
- Volumes 12-17 (2014)
- Volume 11 (2013)
- Volume 10 (2012)
- Volume 9 (2011)
- Volume 8 (2010)
- Volume 7 (2009)
- Volume 6 (2008)
- Volume 5 (2007)
- Volume 4 (2006)
- Volume 3 (2005)
- Volume 2 (2004)
- Volume 1 (2003)
• Stirred tanks with solid loadings up to 40 wt% were simulated using CFD.
• Euler–Euler with KTGF approach provided accurate results for simulating solid suspension.
• Syamlal–O'Brien drag model was found to be applicable over a wide range of conditions.
• Turbulent dispersion force contributed marginally in improving the prediction.
• Reynolds stress model captured the anisotropic turbulence prevalent in the system.
The hydrodynamics of suspension of solids in liquids are critical to the design and performance of stirred tanks as mixing systems. Modelling a multiphase stirred tank at a high solids concentration is complex owing to particle–particle and particle–wall interactions which are generally neglected at low concentrations. Most models do not consider such interactions and deviate significantly from experimental data. Furthermore, drag force, turbulence and turbulent dispersion play a crucial role and need to be precisely known in predicting local hydrodynamics. Therefore, critical factors such as the modelling approach, drag, dispersion, coefficient of restitution and turbulence are examined and discussed exhaustively in this paper. The Euler–Euler approach with kinetic theory of granular flow, Syamlal–O'Brien drag model and Reynolds stress turbulence model provide realistic predictions for such systems. The contribution of the turbulent dispersion force in improving the prediction is marginal but cannot be neglected at low solids volume fractions. Inferences drawn from the study and the finalised models will be instrumental in accurately simulating the solids suspension in stirred tanks for a wide range of conditions. These models can be used in simulations to obtain precise results needed for an in-depth understanding of hydrodynamics in stirred tanks.
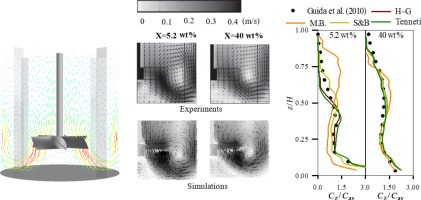