- Volumes 84-95 (2024)
-
Volumes 72-83 (2023)
-
Volume 83
Pages 1-258 (December 2023)
-
Volume 82
Pages 1-204 (November 2023)
-
Volume 81
Pages 1-188 (October 2023)
-
Volume 80
Pages 1-202 (September 2023)
-
Volume 79
Pages 1-172 (August 2023)
-
Volume 78
Pages 1-146 (July 2023)
-
Volume 77
Pages 1-152 (June 2023)
-
Volume 76
Pages 1-176 (May 2023)
-
Volume 75
Pages 1-228 (April 2023)
-
Volume 74
Pages 1-200 (March 2023)
-
Volume 73
Pages 1-138 (February 2023)
-
Volume 72
Pages 1-144 (January 2023)
-
Volume 83
-
Volumes 60-71 (2022)
-
Volume 71
Pages 1-108 (December 2022)
-
Volume 70
Pages 1-106 (November 2022)
-
Volume 69
Pages 1-122 (October 2022)
-
Volume 68
Pages 1-124 (September 2022)
-
Volume 67
Pages 1-102 (August 2022)
-
Volume 66
Pages 1-112 (July 2022)
-
Volume 65
Pages 1-138 (June 2022)
-
Volume 64
Pages 1-186 (May 2022)
-
Volume 63
Pages 1-124 (April 2022)
-
Volume 62
Pages 1-104 (March 2022)
-
Volume 61
Pages 1-120 (February 2022)
-
Volume 60
Pages 1-124 (January 2022)
-
Volume 71
- Volumes 54-59 (2021)
- Volumes 48-53 (2020)
- Volumes 42-47 (2019)
- Volumes 36-41 (2018)
- Volumes 30-35 (2017)
- Volumes 24-29 (2016)
- Volumes 18-23 (2015)
- Volumes 12-17 (2014)
- Volume 11 (2013)
- Volume 10 (2012)
- Volume 9 (2011)
- Volume 8 (2010)
- Volume 7 (2009)
- Volume 6 (2008)
- Volume 5 (2007)
- Volume 4 (2006)
- Volume 3 (2005)
- Volume 2 (2004)
- Volume 1 (2003)
• Effect of pulsating flow on gas–solid flow and performance of FCC riser was investigated.
• CFD simulations of both cold flow and reactive flow in FCC riser were conducted.
• Pulsating flow resulted in a slug flow of solids with more homogeneous radial profiles.
• Pulsating flow also significantly increased feedstock conversion in initial riser height.
Gas–solid flow in a fluid catalytic cracking (FCC) riser exhibits poor mixing in the form of a core–annulus flow pattern and a dense bottom/dilute top distribution of solids. To enhance gas–solid mixing, studies on dense fluidized beds have suggested using a pulsating flow of gas. The present study investigates the effect of pulsating flow on gas–solid hydrodynamics inside the FCC riser employing computational fluid dynamics. Two flow conditions are investigated: a cold flow of air-FCC catalyst in a pilot-scale riser and a reactive flow in an industrial-scale FCC riser. In the cold-flow riser, pulsating flows cause the slug flow of solids and thus increase the average solid accumulation in the flow domain and solid segregation towards the wall. In the industrial FCC riser, pulsating flows produce radial profiles that are more homogeneous. Pulsating flows further improve the conversion and yield in the initial few metres of height. At 7 m, the conversion from pulsating flow is 59%, compared with 44% in without pulsating flow. The results and analysis presented here will help optimize flow conditions in the circulating fluidized bed riser, in not only FCC but also applications such as fast pyrolysis and combustion.
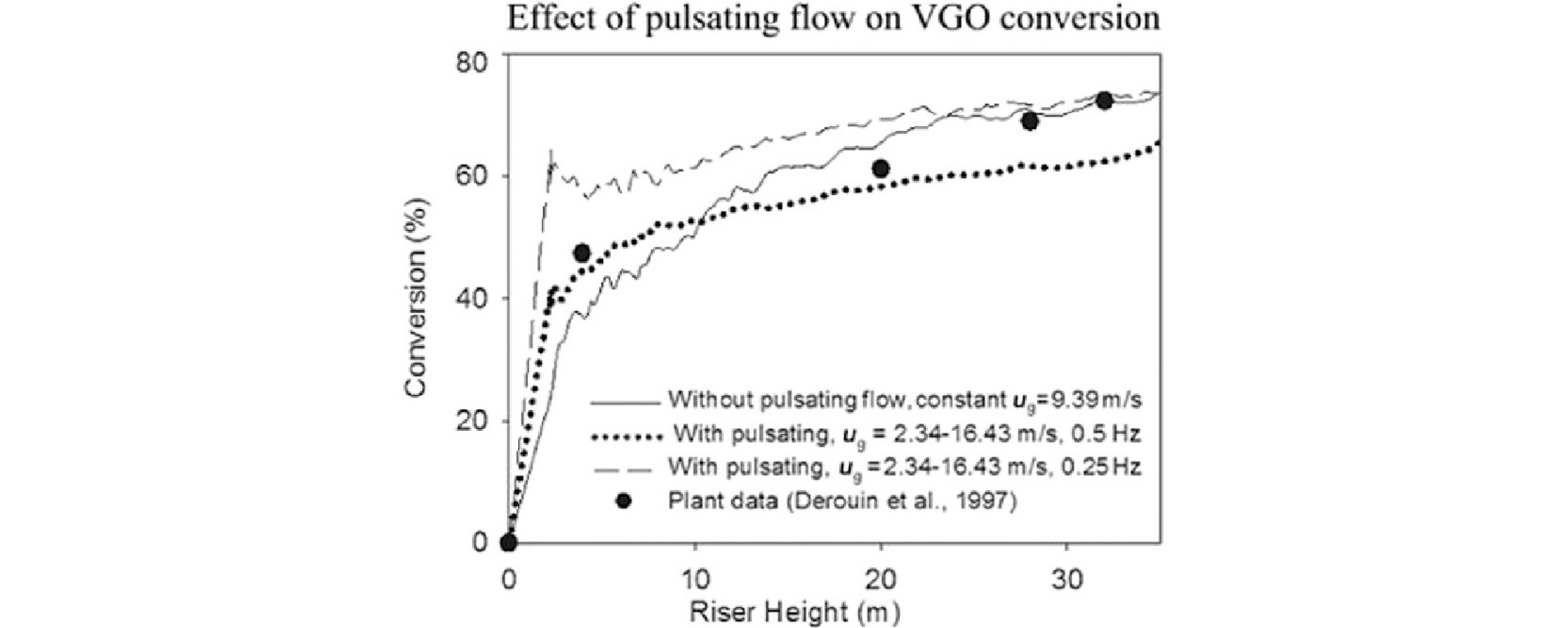