- Volumes 84-95 (2024)
-
Volumes 72-83 (2023)
-
Volume 83
Pages 1-258 (December 2023)
-
Volume 82
Pages 1-204 (November 2023)
-
Volume 81
Pages 1-188 (October 2023)
-
Volume 80
Pages 1-202 (September 2023)
-
Volume 79
Pages 1-172 (August 2023)
-
Volume 78
Pages 1-146 (July 2023)
-
Volume 77
Pages 1-152 (June 2023)
-
Volume 76
Pages 1-176 (May 2023)
-
Volume 75
Pages 1-228 (April 2023)
-
Volume 74
Pages 1-200 (March 2023)
-
Volume 73
Pages 1-138 (February 2023)
-
Volume 72
Pages 1-144 (January 2023)
-
Volume 83
-
Volumes 60-71 (2022)
-
Volume 71
Pages 1-108 (December 2022)
-
Volume 70
Pages 1-106 (November 2022)
-
Volume 69
Pages 1-122 (October 2022)
-
Volume 68
Pages 1-124 (September 2022)
-
Volume 67
Pages 1-102 (August 2022)
-
Volume 66
Pages 1-112 (July 2022)
-
Volume 65
Pages 1-138 (June 2022)
-
Volume 64
Pages 1-186 (May 2022)
-
Volume 63
Pages 1-124 (April 2022)
-
Volume 62
Pages 1-104 (March 2022)
-
Volume 61
Pages 1-120 (February 2022)
-
Volume 60
Pages 1-124 (January 2022)
-
Volume 71
- Volumes 54-59 (2021)
- Volumes 48-53 (2020)
- Volumes 42-47 (2019)
- Volumes 36-41 (2018)
- Volumes 30-35 (2017)
- Volumes 24-29 (2016)
- Volumes 18-23 (2015)
- Volumes 12-17 (2014)
- Volume 11 (2013)
- Volume 10 (2012)
- Volume 9 (2011)
- Volume 8 (2010)
- Volume 7 (2009)
- Volume 6 (2008)
- Volume 5 (2007)
- Volume 4 (2006)
- Volume 3 (2005)
- Volume 2 (2004)
- Volume 1 (2003)
• Rheological behaviors of water-based conductive pastes were adjusted by using alcohol co-solvents.
• Paste’s viscosity was increased with the number of hydroxyl groups for the co-solvent.
• Co-solvent with two hydroxyl groups was the best in inducing Marangoni flow.
• The balance between convective and Marangoni flow should be kept during drying.
• Interconnected carbon black particles provided high conductivity for printed pattern.
A series of water-based conductive carbon pastes were prepared by wet ball milling, followed by vacuum defoaming using isopropyl alcohol, propylene glycol or glycerin as co-solvents. Screen printing was then used to prepare conductive patterns. To determine the influence of co-solvent hydroxyl group number on the properties of water-based conductive carbon pastes, the rheological properties of the pastes and the surface morphologies and conductivities of the printed patterns were characterized. The results show that paste viscosity increased with the number of hydroxyl groups and the latter also affected thixotropy. In addition, the boiling points and surface tensions of the co-solvents increased consistently with hydroxyl group number, affecting the hydrodynamic flow. The conductive carbon paste created using propylene glycol as a co-solvent was the best for screen printing because of its weak coffee-ring effect and appropriate rheological properties, resulting in a smooth coating surface and uniform deposition of the fillers. The resistivity of the pattern printed using paste PG, containing the closest packing of conductive carbon black particles, was 0.44 Ω cm.
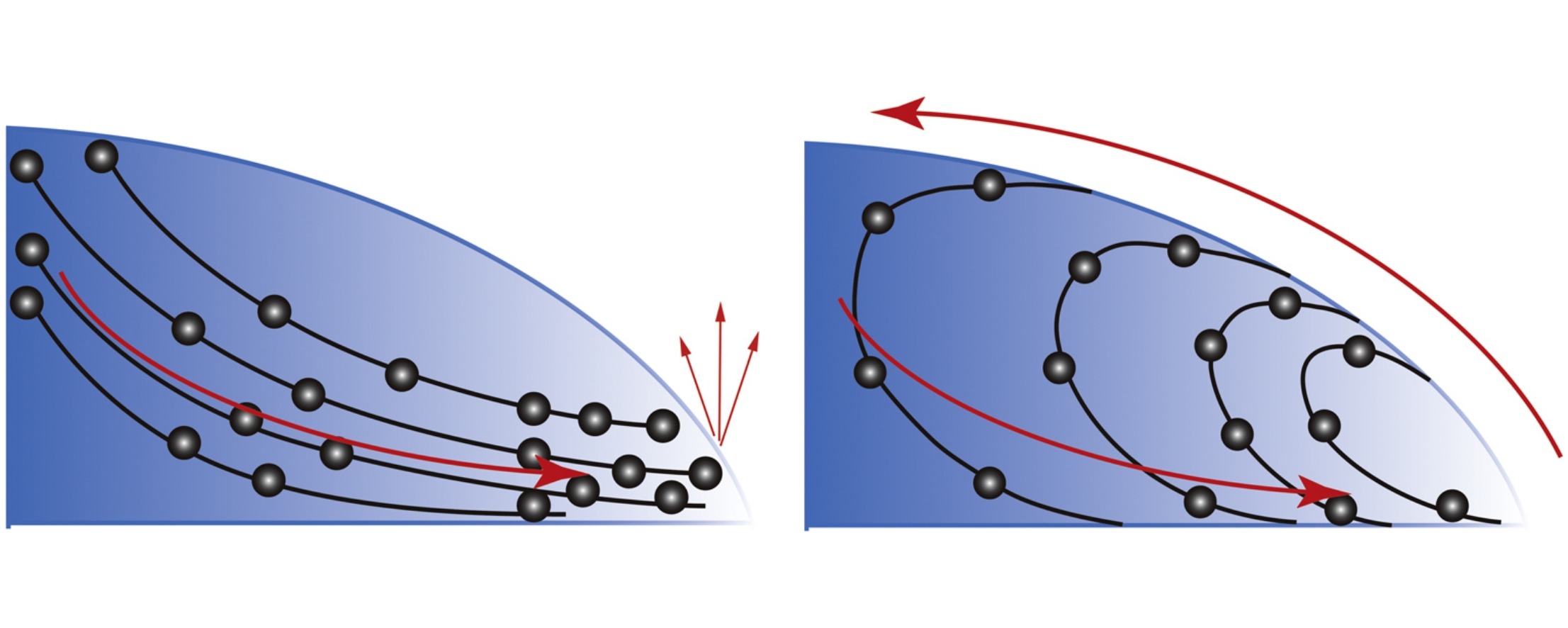