- Volumes 84-95 (2024)
-
Volumes 72-83 (2023)
-
Volume 83
Pages 1-258 (December 2023)
-
Volume 82
Pages 1-204 (November 2023)
-
Volume 81
Pages 1-188 (October 2023)
-
Volume 80
Pages 1-202 (September 2023)
-
Volume 79
Pages 1-172 (August 2023)
-
Volume 78
Pages 1-146 (July 2023)
-
Volume 77
Pages 1-152 (June 2023)
-
Volume 76
Pages 1-176 (May 2023)
-
Volume 75
Pages 1-228 (April 2023)
-
Volume 74
Pages 1-200 (March 2023)
-
Volume 73
Pages 1-138 (February 2023)
-
Volume 72
Pages 1-144 (January 2023)
-
Volume 83
-
Volumes 60-71 (2022)
-
Volume 71
Pages 1-108 (December 2022)
-
Volume 70
Pages 1-106 (November 2022)
-
Volume 69
Pages 1-122 (October 2022)
-
Volume 68
Pages 1-124 (September 2022)
-
Volume 67
Pages 1-102 (August 2022)
-
Volume 66
Pages 1-112 (July 2022)
-
Volume 65
Pages 1-138 (June 2022)
-
Volume 64
Pages 1-186 (May 2022)
-
Volume 63
Pages 1-124 (April 2022)
-
Volume 62
Pages 1-104 (March 2022)
-
Volume 61
Pages 1-120 (February 2022)
-
Volume 60
Pages 1-124 (January 2022)
-
Volume 71
- Volumes 54-59 (2021)
- Volumes 48-53 (2020)
- Volumes 42-47 (2019)
- Volumes 36-41 (2018)
- Volumes 30-35 (2017)
- Volumes 24-29 (2016)
- Volumes 18-23 (2015)
- Volumes 12-17 (2014)
- Volume 11 (2013)
- Volume 10 (2012)
- Volume 9 (2011)
- Volume 8 (2010)
- Volume 7 (2009)
- Volume 6 (2008)
- Volume 5 (2007)
- Volume 4 (2006)
- Volume 3 (2005)
- Volume 2 (2004)
- Volume 1 (2003)
• New approach for coating fine dispersed particles (d < 50 μm).
• Comparison between the measured and calculated suspension viscosity.
• Calculated liquid film thickness to be used to predict the formation of agglomerates.
• Influence of significant (process) parameters on product quality of coated particles.
Particle coatings are used extensively to generate dispersed solids with well-defined properties, e.g., to protect active ingredients, with most coating processes using core particles of a diameter larger than 200 μm. This work contributes to the development of a coating process for fine dispersed particles (diameter less than 50 μm) by combining two particle-formulation processes, namely, coating and spray drying. The feasibility of the operation is based on and demonstrated by the innovative application of a two-fluid nozzle. Experiments were conducted by using glass particles as core particles and sodium benzoate as the coating agent. The coating of finely dispersed particles is achieved by the spraying of particles and coating solution as a homogeneous suspension. The aim is to create droplets with only one contained particle at the nozzle outlet. After evaporation of the water in the droplet, a thin solid film is built on the particle surface. The suspension viscosity was measured and compared with empirical equations from the literature. The liquid-film thickness on the particle surface was calculated to predict the building of a uniform coating layer or agglomerates. In this study, the feasibility of pneumatic transport through the nozzle and an investigation of the process were illustrated. The agglomeration fraction and degree of coating of the particle surface were analyzed optically by scanning electron microscopy. In this way, the influence of different processes and suspension parameters on the product quality were determined.
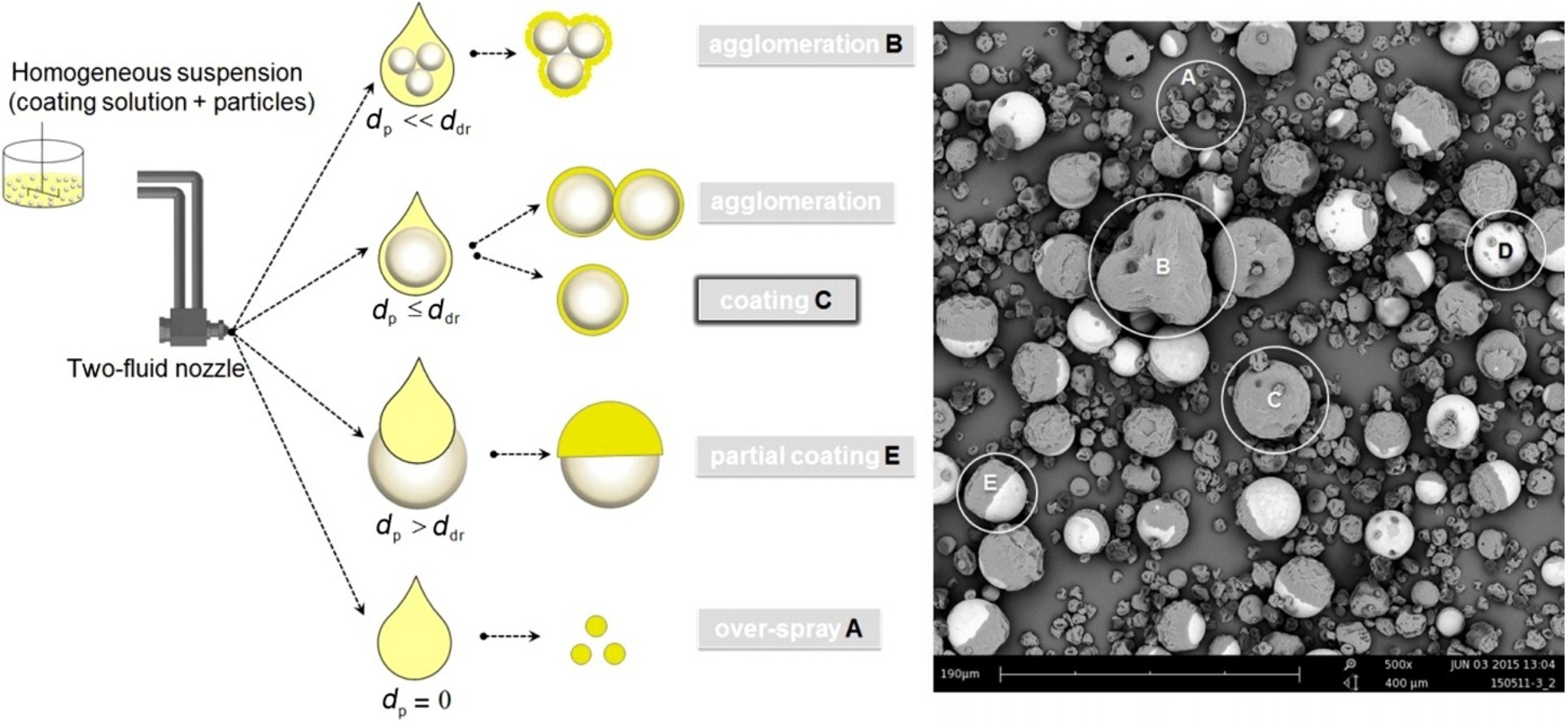