- Volumes 84-95 (2024)
-
Volumes 72-83 (2023)
-
Volume 83
Pages 1-258 (December 2023)
-
Volume 82
Pages 1-204 (November 2023)
-
Volume 81
Pages 1-188 (October 2023)
-
Volume 80
Pages 1-202 (September 2023)
-
Volume 79
Pages 1-172 (August 2023)
-
Volume 78
Pages 1-146 (July 2023)
-
Volume 77
Pages 1-152 (June 2023)
-
Volume 76
Pages 1-176 (May 2023)
-
Volume 75
Pages 1-228 (April 2023)
-
Volume 74
Pages 1-200 (March 2023)
-
Volume 73
Pages 1-138 (February 2023)
-
Volume 72
Pages 1-144 (January 2023)
-
Volume 83
-
Volumes 60-71 (2022)
-
Volume 71
Pages 1-108 (December 2022)
-
Volume 70
Pages 1-106 (November 2022)
-
Volume 69
Pages 1-122 (October 2022)
-
Volume 68
Pages 1-124 (September 2022)
-
Volume 67
Pages 1-102 (August 2022)
-
Volume 66
Pages 1-112 (July 2022)
-
Volume 65
Pages 1-138 (June 2022)
-
Volume 64
Pages 1-186 (May 2022)
-
Volume 63
Pages 1-124 (April 2022)
-
Volume 62
Pages 1-104 (March 2022)
-
Volume 61
Pages 1-120 (February 2022)
-
Volume 60
Pages 1-124 (January 2022)
-
Volume 71
- Volumes 54-59 (2021)
- Volumes 48-53 (2020)
- Volumes 42-47 (2019)
- Volumes 36-41 (2018)
- Volumes 30-35 (2017)
- Volumes 24-29 (2016)
- Volumes 18-23 (2015)
- Volumes 12-17 (2014)
- Volume 11 (2013)
- Volume 10 (2012)
- Volume 9 (2011)
- Volume 8 (2010)
- Volume 7 (2009)
- Volume 6 (2008)
- Volume 5 (2007)
- Volume 4 (2006)
- Volume 3 (2005)
- Volume 2 (2004)
- Volume 1 (2003)
• A CFD model of a reactive flow of gas, catalyst and droplets was developed.
• The model was used to investigate effect of baffles on performance of FCC riser.
• Baffles enhanced radial dispersion of catalyst and heat transfer inside the riser.
• Baffles increased conversion of VGO, yield of the gasoline and pressure drop.
• Optimization of baffle configurations was required for desired performance.
Increasing demand of automobile fuel and a need to process heavier crude oil makes it imperative to find improvements to the design of existing fluid catalytic cracking (FCC) units. Several modifications to the design of the riser section of FCC units have been suggested in previous studies including: improved feed nozzle designs, multiple nozzle configurations, internal baffles, and novel two-stage-riser systems. In this study, we investigate the effects of baffles on the performance of FCC risers using computational fluid dynamics simulations. In this study, predictions from a basis model (without baffles) are compared with those from four different configurations including: (i) 5-cm baffles at 5-m spacing, (ii) 7.5-cm baffles at 5-m spacing, (iii) 10-cm baffles with 5-m spacing, (iv) 10-cm baffles at 2.5-m spacing, and (v) 10-cm baffles at 1-m spacing. The baffles force the catalyst away from walls toward the center of the riser, enhancing the radial dispersion of the catalyst and the heat transfer inside the riser. The use of longer baffles and smaller spacings further increases the dispersion, yielding more homogeneous radial profiles. The changes in the radial dispersion result in variations in the conversion, yields, and pressure drops. The baffles increase conversion of vacuum gas oil (VGO) and the yield of gasoline. However, the simulations showed that longer baffles and a larger number of baffles did not always give a higher yield or higher conversion. Among the simulated configurations, the 5-cm baffles at 5-m spacing gave the highest conversion of VGO, whereas the 10-cm baffles at 1-m spacing resulted in the highest yield of the gasoline. Thus, rational optimization of baffle configurations is required to achieve optimal performance.
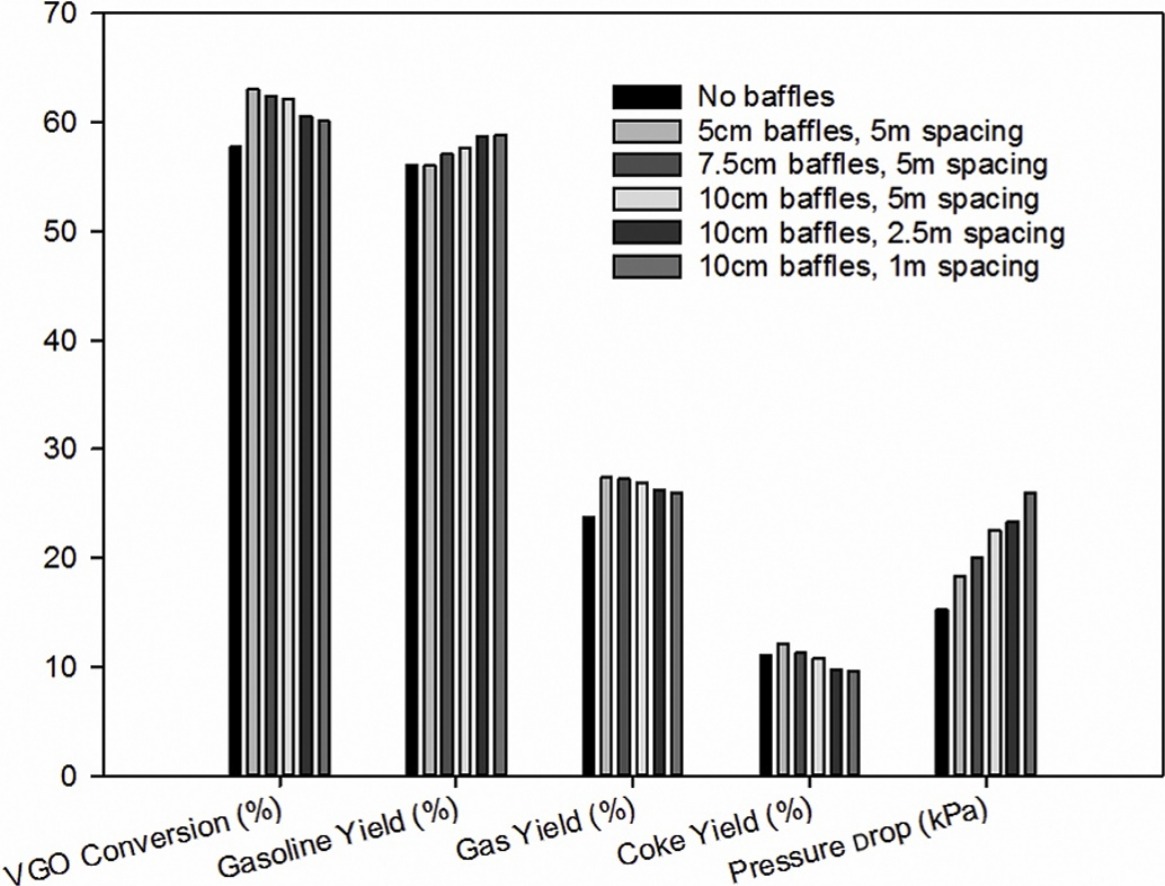