- Volumes 84-95 (2024)
-
Volumes 72-83 (2023)
-
Volume 83
Pages 1-258 (December 2023)
-
Volume 82
Pages 1-204 (November 2023)
-
Volume 81
Pages 1-188 (October 2023)
-
Volume 80
Pages 1-202 (September 2023)
-
Volume 79
Pages 1-172 (August 2023)
-
Volume 78
Pages 1-146 (July 2023)
-
Volume 77
Pages 1-152 (June 2023)
-
Volume 76
Pages 1-176 (May 2023)
-
Volume 75
Pages 1-228 (April 2023)
-
Volume 74
Pages 1-200 (March 2023)
-
Volume 73
Pages 1-138 (February 2023)
-
Volume 72
Pages 1-144 (January 2023)
-
Volume 83
-
Volumes 60-71 (2022)
-
Volume 71
Pages 1-108 (December 2022)
-
Volume 70
Pages 1-106 (November 2022)
-
Volume 69
Pages 1-122 (October 2022)
-
Volume 68
Pages 1-124 (September 2022)
-
Volume 67
Pages 1-102 (August 2022)
-
Volume 66
Pages 1-112 (July 2022)
-
Volume 65
Pages 1-138 (June 2022)
-
Volume 64
Pages 1-186 (May 2022)
-
Volume 63
Pages 1-124 (April 2022)
-
Volume 62
Pages 1-104 (March 2022)
-
Volume 61
Pages 1-120 (February 2022)
-
Volume 60
Pages 1-124 (January 2022)
-
Volume 71
- Volumes 54-59 (2021)
- Volumes 48-53 (2020)
- Volumes 42-47 (2019)
- Volumes 36-41 (2018)
- Volumes 30-35 (2017)
- Volumes 24-29 (2016)
- Volumes 18-23 (2015)
- Volumes 12-17 (2014)
- Volume 11 (2013)
- Volume 10 (2012)
- Volume 9 (2011)
- Volume 8 (2010)
- Volume 7 (2009)
- Volume 6 (2008)
- Volume 5 (2007)
- Volume 4 (2006)
- Volume 3 (2005)
- Volume 2 (2004)
- Volume 1 (2003)
• CNTs coating on Cu powder was performed in two types of ball mills.
• CNTs coating on Cu powder was obtained at low rotation speed.
• Cracks formed on the Cu particle surface during ball milling process.
We investigated the effect of the raw powder properties of carbon nanotube surface coatings on metal powder, with the goal of obtaining high-quality nanocomposites. The mechanical dry coating technique was used to fabricate CNT coatings (guest particles) on the surface of copper (Cu, host) particles using a traditional ball mill and a stirred ball mill. The coatings were produced under various experimental conditions (varying rotation speed and grinding duration, with a ball diameter of 5 mm), and the effect of these conditions on the surface of the powder was determined. The coated surfaces were characterized using scanning electron microscopy and field emission scanning electron microscopy. We compared prolonged milling (48 h) at a low rotation speed (50 rpm), with a short milling period (12 h) at high rotation speed. We found that for the TBM, successful CNT coating was achieved at 50 rpm over 48 h. In contrast, for the SBM, CNT coatings were obtained after a short milling period (12 h) at low rotation speed (50 rpm).
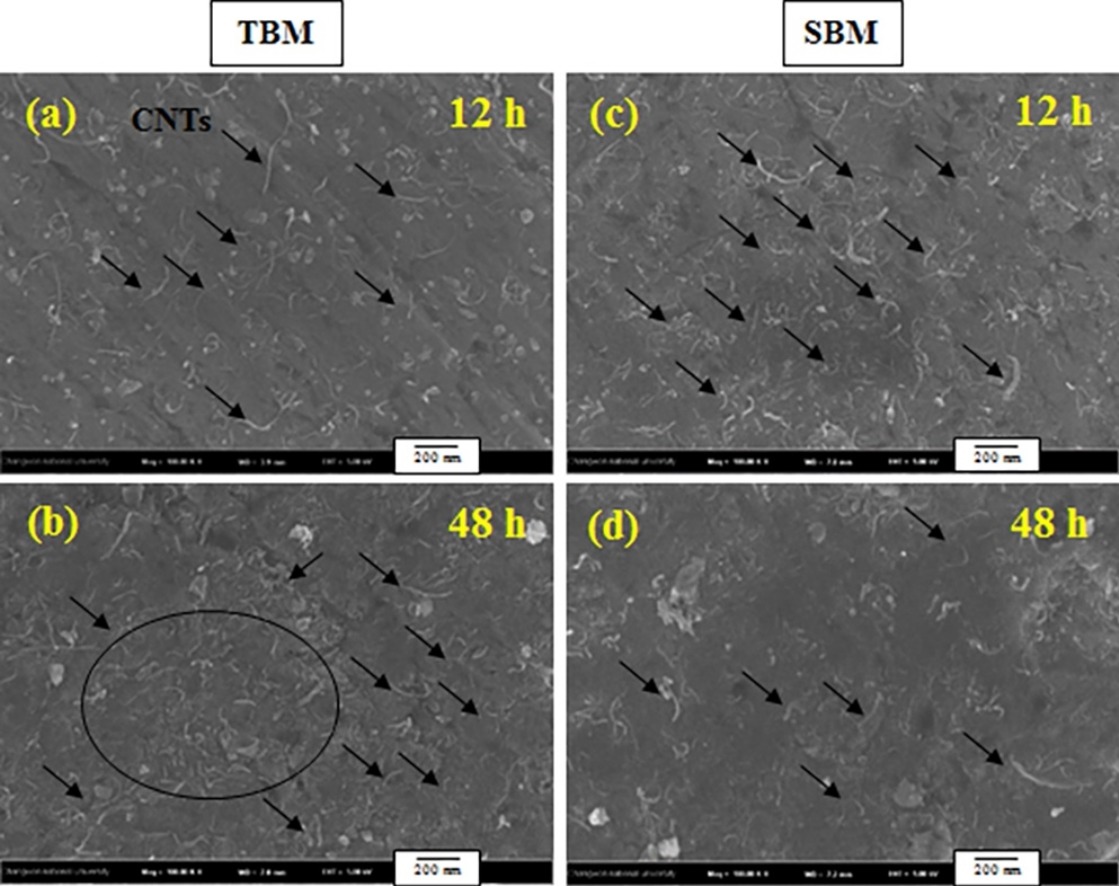