- Volumes 84-95 (2024)
-
Volumes 72-83 (2023)
-
Volume 83
Pages 1-258 (December 2023)
-
Volume 82
Pages 1-204 (November 2023)
-
Volume 81
Pages 1-188 (October 2023)
-
Volume 80
Pages 1-202 (September 2023)
-
Volume 79
Pages 1-172 (August 2023)
-
Volume 78
Pages 1-146 (July 2023)
-
Volume 77
Pages 1-152 (June 2023)
-
Volume 76
Pages 1-176 (May 2023)
-
Volume 75
Pages 1-228 (April 2023)
-
Volume 74
Pages 1-200 (March 2023)
-
Volume 73
Pages 1-138 (February 2023)
-
Volume 72
Pages 1-144 (January 2023)
-
Volume 83
-
Volumes 60-71 (2022)
-
Volume 71
Pages 1-108 (December 2022)
-
Volume 70
Pages 1-106 (November 2022)
-
Volume 69
Pages 1-122 (October 2022)
-
Volume 68
Pages 1-124 (September 2022)
-
Volume 67
Pages 1-102 (August 2022)
-
Volume 66
Pages 1-112 (July 2022)
-
Volume 65
Pages 1-138 (June 2022)
-
Volume 64
Pages 1-186 (May 2022)
-
Volume 63
Pages 1-124 (April 2022)
-
Volume 62
Pages 1-104 (March 2022)
-
Volume 61
Pages 1-120 (February 2022)
-
Volume 60
Pages 1-124 (January 2022)
-
Volume 71
- Volumes 54-59 (2021)
- Volumes 48-53 (2020)
- Volumes 42-47 (2019)
- Volumes 36-41 (2018)
- Volumes 30-35 (2017)
- Volumes 24-29 (2016)
- Volumes 18-23 (2015)
- Volumes 12-17 (2014)
- Volume 11 (2013)
- Volume 10 (2012)
- Volume 9 (2011)
- Volume 8 (2010)
- Volume 7 (2009)
- Volume 6 (2008)
- Volume 5 (2007)
- Volume 4 (2006)
- Volume 3 (2005)
- Volume 2 (2004)
- Volume 1 (2003)
• A simulation of fluid dynamics of PCM particles in a Wurster spout–fluid bed was performed.
• Higher air flow rate was appropriate for an upward movement of particles in Wurster tube.
• Uniform thermal profile lower than air inlet temperature was obtained experimentally in reactor.
Spout–fluid-bed coating of solid–lipid materials, including some Phase Change Materials (PCMs), is a rarely used approach because of the probability of a phase change during the process. However, if mastered, this process could enable the commercialization of high-load PCM particles to develop new materials. An understanding of the thermal and fluid dynamics profiles inside a reactor can be used to establish optimized coating conditions, to avoid premature PCM melting and to maximize the drying rate. This research studies, through computational simulation, the behavior of particles and the experimental thermal profile inside a Wurster spout–fluid bed. A simplified model approach of momentum was simulated using OpenFOAM and carnauba wax particles as a PCM material. The simulation showed that appropriate flow conditions inside the Wurster tube must vary between 200 and 300 m3/h to ensure a better particle coating. The measured experimental thermal profile was uniform in the reactor and it was 5–10 °C lower than the set temperature. Thus, a maximum airflow at 70 °C that was used in the equipment is considered suitable for the further coating of PCM particles. The methodology proved useful for the preliminary identification of flow and temperature conditions in the spout–fluid process.
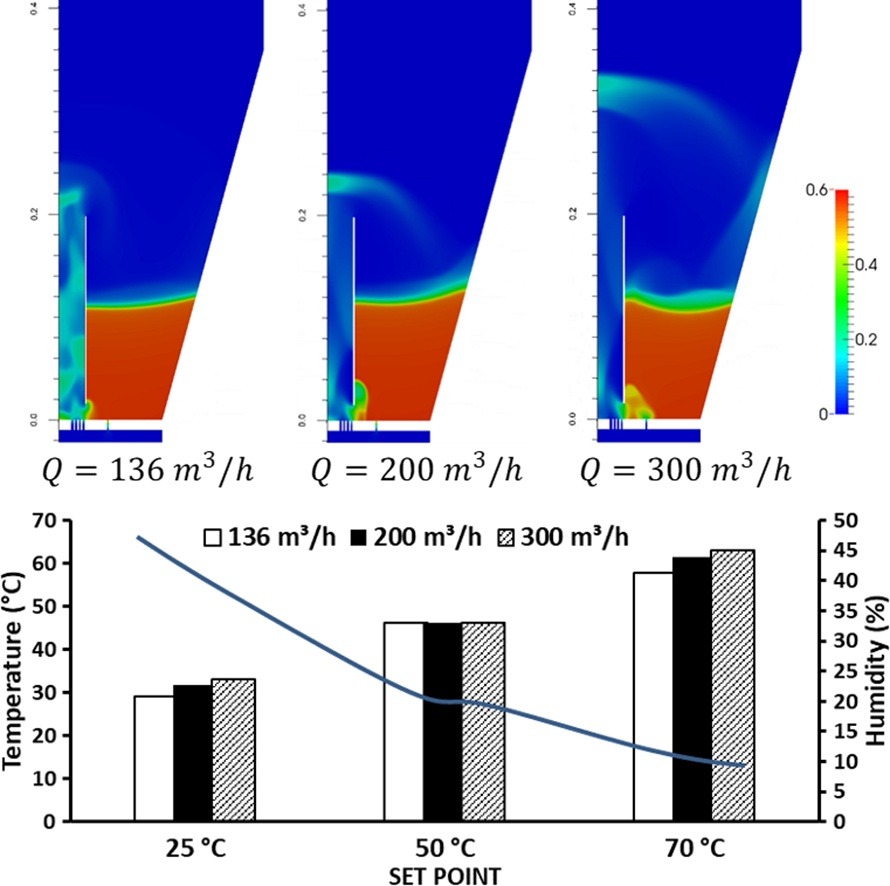