- Volumes 84-95 (2024)
-
Volumes 72-83 (2023)
-
Volume 83
Pages 1-258 (December 2023)
-
Volume 82
Pages 1-204 (November 2023)
-
Volume 81
Pages 1-188 (October 2023)
-
Volume 80
Pages 1-202 (September 2023)
-
Volume 79
Pages 1-172 (August 2023)
-
Volume 78
Pages 1-146 (July 2023)
-
Volume 77
Pages 1-152 (June 2023)
-
Volume 76
Pages 1-176 (May 2023)
-
Volume 75
Pages 1-228 (April 2023)
-
Volume 74
Pages 1-200 (March 2023)
-
Volume 73
Pages 1-138 (February 2023)
-
Volume 72
Pages 1-144 (January 2023)
-
Volume 83
-
Volumes 60-71 (2022)
-
Volume 71
Pages 1-108 (December 2022)
-
Volume 70
Pages 1-106 (November 2022)
-
Volume 69
Pages 1-122 (October 2022)
-
Volume 68
Pages 1-124 (September 2022)
-
Volume 67
Pages 1-102 (August 2022)
-
Volume 66
Pages 1-112 (July 2022)
-
Volume 65
Pages 1-138 (June 2022)
-
Volume 64
Pages 1-186 (May 2022)
-
Volume 63
Pages 1-124 (April 2022)
-
Volume 62
Pages 1-104 (March 2022)
-
Volume 61
Pages 1-120 (February 2022)
-
Volume 60
Pages 1-124 (January 2022)
-
Volume 71
- Volumes 54-59 (2021)
- Volumes 48-53 (2020)
- Volumes 42-47 (2019)
- Volumes 36-41 (2018)
- Volumes 30-35 (2017)
- Volumes 24-29 (2016)
- Volumes 18-23 (2015)
- Volumes 12-17 (2014)
- Volume 11 (2013)
- Volume 10 (2012)
- Volume 9 (2011)
- Volume 8 (2010)
- Volume 7 (2009)
- Volume 6 (2008)
- Volume 5 (2007)
- Volume 4 (2006)
- Volume 3 (2005)
- Volume 2 (2004)
- Volume 1 (2003)
• Vibrated packings of monosized regular icosahedral particles were numerically modeled by DEM.
• Transformation from random loose packing to random close packing was reproduced.
• Influences of operating parameters on the packing densification were identified and optimized.
• Various macro and micro properties of the packing structures were characterized and compared.
Packing densification of monosized regular icosahedral particles under three-dimensional mechanical vibration has been simulated by the discrete element method (DEM). The effects of the vibration conditions and container size on packing densification were systematically investigated. In addition to the macroscale properties (packing density and porosity), the microscale properties, such as the coordination number (CN), radial distribution function (RDF), particle contact type, particle orientation distribution, and stresses/forces, in random loose packing (RLP) and random close packing (RCP) were also characterized and analyzed. The results show that transformation of icosahedral particle packing from RLP to RCP can be realized by properly controlling the vibration conditions. The maximum random packing density without the wall effect reaches 0.7078. Microscale property analysis shows that the average CN increases after vibration. The RDF curves contain two clear peaks for RLP and three for RCP. From RLP to RCP, the probability of face to face contact between two particles increases, while the probabilities of edge to edge, edge to face, and face to vertex contact decrease. The orientation correlation functions indicate the randomness of the vibrated packing structure. In addition, more uniform force and stress distributions are observed within the dense packing structure.
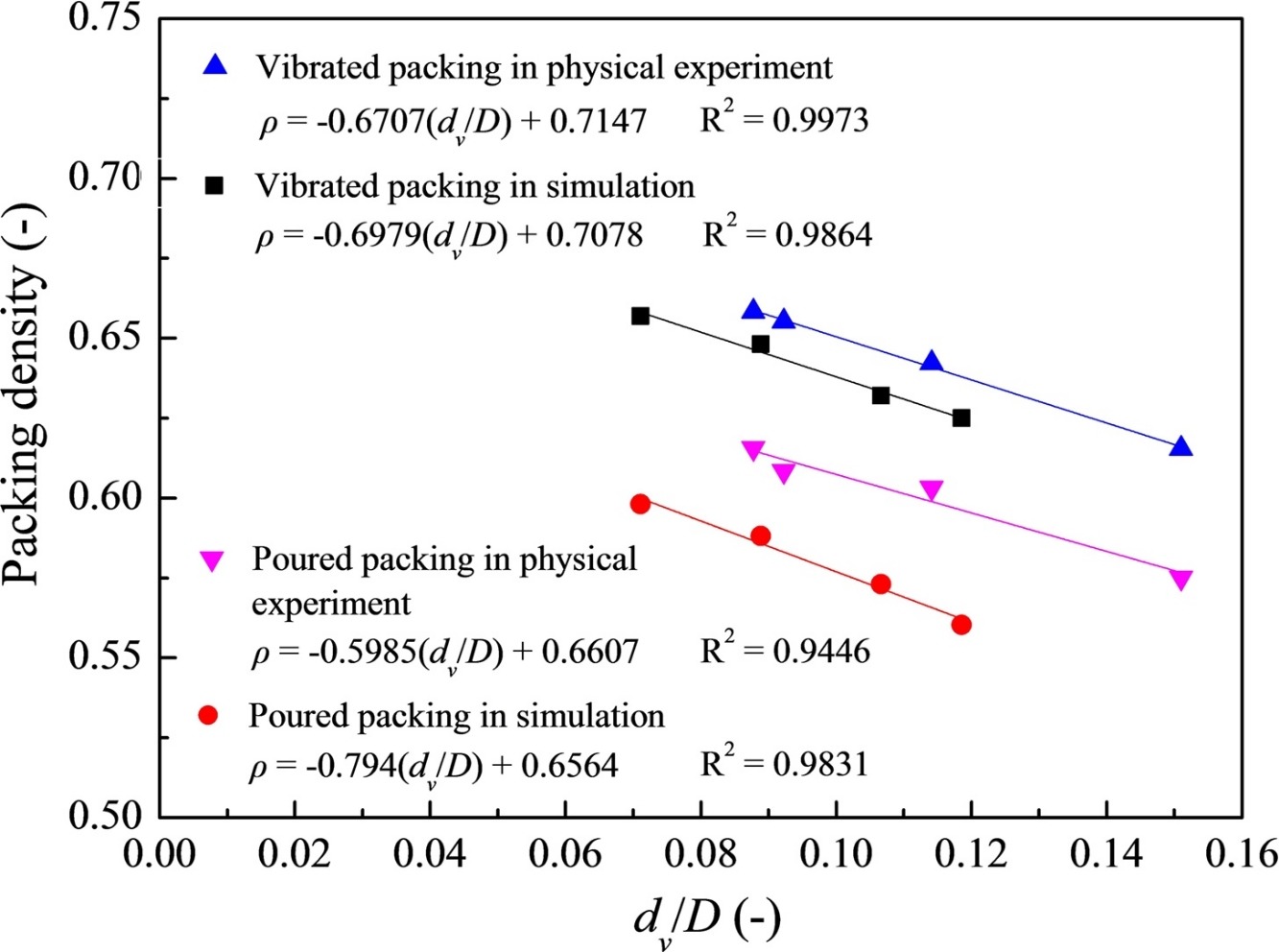