- Volumes 84-95 (2024)
-
Volumes 72-83 (2023)
-
Volume 83
Pages 1-258 (December 2023)
-
Volume 82
Pages 1-204 (November 2023)
-
Volume 81
Pages 1-188 (October 2023)
-
Volume 80
Pages 1-202 (September 2023)
-
Volume 79
Pages 1-172 (August 2023)
-
Volume 78
Pages 1-146 (July 2023)
-
Volume 77
Pages 1-152 (June 2023)
-
Volume 76
Pages 1-176 (May 2023)
-
Volume 75
Pages 1-228 (April 2023)
-
Volume 74
Pages 1-200 (March 2023)
-
Volume 73
Pages 1-138 (February 2023)
-
Volume 72
Pages 1-144 (January 2023)
-
Volume 83
-
Volumes 60-71 (2022)
-
Volume 71
Pages 1-108 (December 2022)
-
Volume 70
Pages 1-106 (November 2022)
-
Volume 69
Pages 1-122 (October 2022)
-
Volume 68
Pages 1-124 (September 2022)
-
Volume 67
Pages 1-102 (August 2022)
-
Volume 66
Pages 1-112 (July 2022)
-
Volume 65
Pages 1-138 (June 2022)
-
Volume 64
Pages 1-186 (May 2022)
-
Volume 63
Pages 1-124 (April 2022)
-
Volume 62
Pages 1-104 (March 2022)
-
Volume 61
Pages 1-120 (February 2022)
-
Volume 60
Pages 1-124 (January 2022)
-
Volume 71
- Volumes 54-59 (2021)
- Volumes 48-53 (2020)
- Volumes 42-47 (2019)
- Volumes 36-41 (2018)
- Volumes 30-35 (2017)
- Volumes 24-29 (2016)
- Volumes 18-23 (2015)
- Volumes 12-17 (2014)
- Volume 11 (2013)
- Volume 10 (2012)
- Volume 9 (2011)
- Volume 8 (2010)
- Volume 7 (2009)
- Volume 6 (2008)
- Volume 5 (2007)
- Volume 4 (2006)
- Volume 3 (2005)
- Volume 2 (2004)
- Volume 1 (2003)
• A core–shell structure of SiC@Al2O3 nanoparticles is designed and prepared.
• Sintering of dense SiC matrix by slow co-precipitation method is optimized.
• The SiC@Al2O3 nanoparticles exhibit better sintering properties.
• The optimized parameters to obtain a dense sintered SiC matrix are determined.
Owing to the difficulty for dense SiC sintering, high sintering temperatures and pressures are usually needed. Lowering the sintering temperature by adding Al2O3 as a sintering additive has previously been shown to be beneficial. However, traditional addition methods limit the effect of the Al2O3 owing to inhomogeneous mixing at the nanoscale. A SiC@Al2O3 composite nanoparticle with a core–shell structure is designed and prepared using the slow co-precipitation method. The differences between this method and the traditional mechanical ball milling method are interpreted by different experimental parameters, such as temperature, pressure, amount of additive, and mixing type. It is found that the method of slow co-precipitation enables homogeneous mixing of Al2O3 and SiC at a smaller scale, and makes the sintered SiC much denser and more homogeneous, when compared with the traditional method. The parameters of sintering at 1900 °C and 30 MPa for 30 min are recommended. The conclusions here are also beneficial for the sintering research of other ceramic materials.
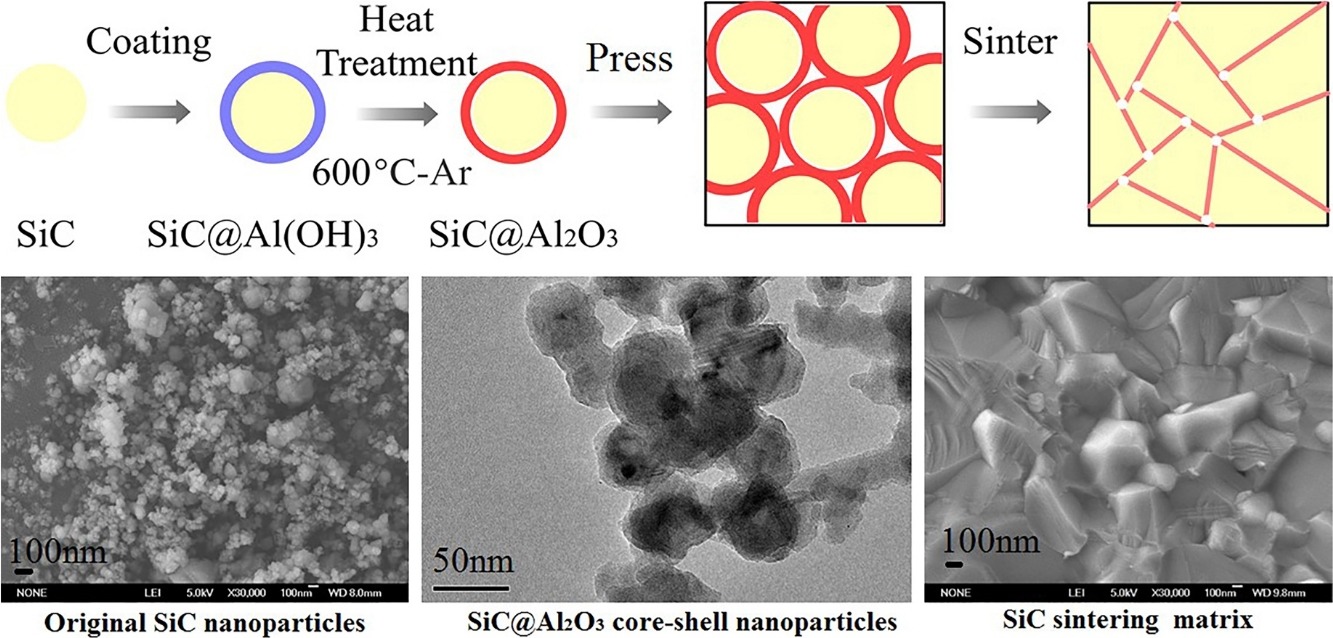