- Volumes 84-95 (2024)
-
Volumes 72-83 (2023)
-
Volume 83
Pages 1-258 (December 2023)
-
Volume 82
Pages 1-204 (November 2023)
-
Volume 81
Pages 1-188 (October 2023)
-
Volume 80
Pages 1-202 (September 2023)
-
Volume 79
Pages 1-172 (August 2023)
-
Volume 78
Pages 1-146 (July 2023)
-
Volume 77
Pages 1-152 (June 2023)
-
Volume 76
Pages 1-176 (May 2023)
-
Volume 75
Pages 1-228 (April 2023)
-
Volume 74
Pages 1-200 (March 2023)
-
Volume 73
Pages 1-138 (February 2023)
-
Volume 72
Pages 1-144 (January 2023)
-
Volume 83
-
Volumes 60-71 (2022)
-
Volume 71
Pages 1-108 (December 2022)
-
Volume 70
Pages 1-106 (November 2022)
-
Volume 69
Pages 1-122 (October 2022)
-
Volume 68
Pages 1-124 (September 2022)
-
Volume 67
Pages 1-102 (August 2022)
-
Volume 66
Pages 1-112 (July 2022)
-
Volume 65
Pages 1-138 (June 2022)
-
Volume 64
Pages 1-186 (May 2022)
-
Volume 63
Pages 1-124 (April 2022)
-
Volume 62
Pages 1-104 (March 2022)
-
Volume 61
Pages 1-120 (February 2022)
-
Volume 60
Pages 1-124 (January 2022)
-
Volume 71
- Volumes 54-59 (2021)
- Volumes 48-53 (2020)
- Volumes 42-47 (2019)
- Volumes 36-41 (2018)
- Volumes 30-35 (2017)
- Volumes 24-29 (2016)
- Volumes 18-23 (2015)
- Volumes 12-17 (2014)
- Volume 11 (2013)
- Volume 10 (2012)
- Volume 9 (2011)
- Volume 8 (2010)
- Volume 7 (2009)
- Volume 6 (2008)
- Volume 5 (2007)
- Volume 4 (2006)
- Volume 3 (2005)
- Volume 2 (2004)
- Volume 1 (2003)
• Powder coating with viscous liquids versus foams is assessed via image analysis.
• Foams with cm size bubbles coat particles best.
• Most important parameters for coating with foams is mixer speed and residence time.
• Rheological properties of the liquid and foams influence coating behaviour.
• Image analysis and SEM are useful tools to deduce the quality of coating achieved.
Particle or powder coating with viscous liquids has been essential in industry for surface modification purposes to induce and enhance specific functionalities. This paper evaluates the performance of using foams (of different bubble diameters) versus liquids as a means of coating powder beds based on viscous liquid formulations. Coating with viscous liquids present numerous industrial challenges and therefore preparing foam equivalents can render the liquid component weak enough (through pre shearing to form the foam), to allow it to break up and coat particles under the shear forces exerted in a mixing device.
In this study, two shear mixers are used; the first type consists of paddles in different configurations attached to a single rotating shaft, whilst the second type is a commercial twin screw mixer (TSM). The quality of coating achieved on the bulk powder bed using liquids and foams (stained with a dye) is assessed by image analysis to determine the homogeneity of the color distribution. In addition, scanning electron microscopy provides a tool to further investigate the coating quality of individual particles from the bulk product.
The results show that large bubble (centimeter size) foams are much more effective at distributing within the fluidized powder bed compared to the starting viscous liquid and small bubble foams (sub-millimeter size). Furthermore, there is a maximum ratio of foam to powder beyond which agglomeration occurs and is insufficient to fully coat the particles. Coating of individual particles is achieved in the case of the TSM, whereas SEM proves that the single shaft paddle mixer crushes the particles and subsequently granulates them together to form granules of a size comparable to the size of coated particles seen after coating with the TSM.
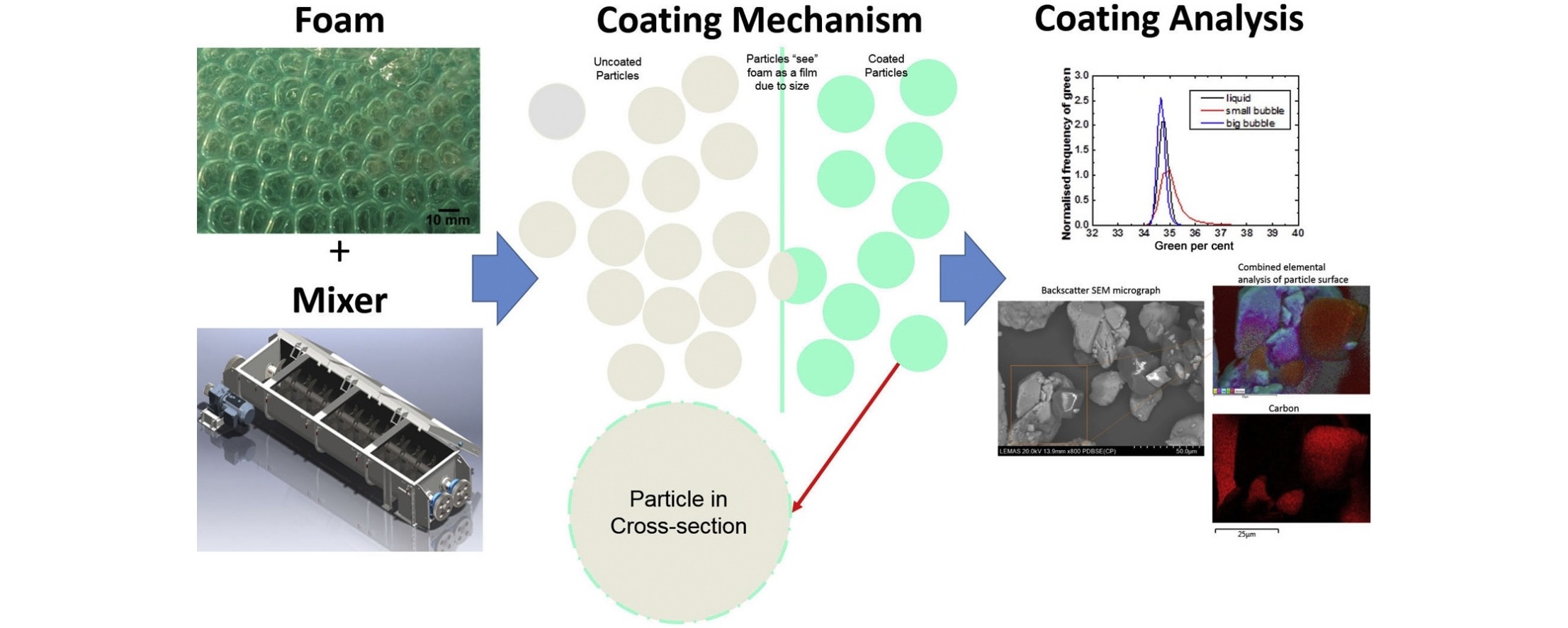