- Volumes 84-95 (2024)
-
Volumes 72-83 (2023)
-
Volume 83
Pages 1-258 (December 2023)
-
Volume 82
Pages 1-204 (November 2023)
-
Volume 81
Pages 1-188 (October 2023)
-
Volume 80
Pages 1-202 (September 2023)
-
Volume 79
Pages 1-172 (August 2023)
-
Volume 78
Pages 1-146 (July 2023)
-
Volume 77
Pages 1-152 (June 2023)
-
Volume 76
Pages 1-176 (May 2023)
-
Volume 75
Pages 1-228 (April 2023)
-
Volume 74
Pages 1-200 (March 2023)
-
Volume 73
Pages 1-138 (February 2023)
-
Volume 72
Pages 1-144 (January 2023)
-
Volume 83
-
Volumes 60-71 (2022)
-
Volume 71
Pages 1-108 (December 2022)
-
Volume 70
Pages 1-106 (November 2022)
-
Volume 69
Pages 1-122 (October 2022)
-
Volume 68
Pages 1-124 (September 2022)
-
Volume 67
Pages 1-102 (August 2022)
-
Volume 66
Pages 1-112 (July 2022)
-
Volume 65
Pages 1-138 (June 2022)
-
Volume 64
Pages 1-186 (May 2022)
-
Volume 63
Pages 1-124 (April 2022)
-
Volume 62
Pages 1-104 (March 2022)
-
Volume 61
Pages 1-120 (February 2022)
-
Volume 60
Pages 1-124 (January 2022)
-
Volume 71
- Volumes 54-59 (2021)
- Volumes 48-53 (2020)
- Volumes 42-47 (2019)
- Volumes 36-41 (2018)
- Volumes 30-35 (2017)
- Volumes 24-29 (2016)
- Volumes 18-23 (2015)
- Volumes 12-17 (2014)
- Volume 11 (2013)
- Volume 10 (2012)
- Volume 9 (2011)
- Volume 8 (2010)
- Volume 7 (2009)
- Volume 6 (2008)
- Volume 5 (2007)
- Volume 4 (2006)
- Volume 3 (2005)
- Volume 2 (2004)
- Volume 1 (2003)
• A particle-scale numerical model of iron ore reduction was developed and systematically validated.
• Reduction rates obtained with and without accounting for gas film resistance differ slightly (by ∼3%).
• The reduction rate increases significantly with increasing pressure up to ∼5 atm.
• Under non-isothermal conditions, the entire reduction process slows down.
Iron ore reduction is a primary unit operation in current metallurgy processes and dominates the energy consumption and greenhouse gas (GHG) emissions of the iron-making process. Therefore, even a slight improvement of the energy efficiency or GHG emissions of iron ore reduction would yield considerable benefits to the cost of pig iron and, more importantly, to mitigation of the associated carbon footprint. The current study presents a discrete model that describes the iron ore reduction process for a single pellet. The transient reaction progress can be predicted and is validated against experimental measurements under various operating conditions, including different reducing gases and temperatures. The effects of pressure, isothermality, gas composition, and flow rate on reduction are investigated. The reduction rate increases significantly with increasing pressure until 5 atm, and the entire reduction process occurs more slowly under non-isothermal conditions than under isothermal conditions. This work provides a solid foundation for the development of a comprehensive particulate system model that considers both heat and mass transfer.
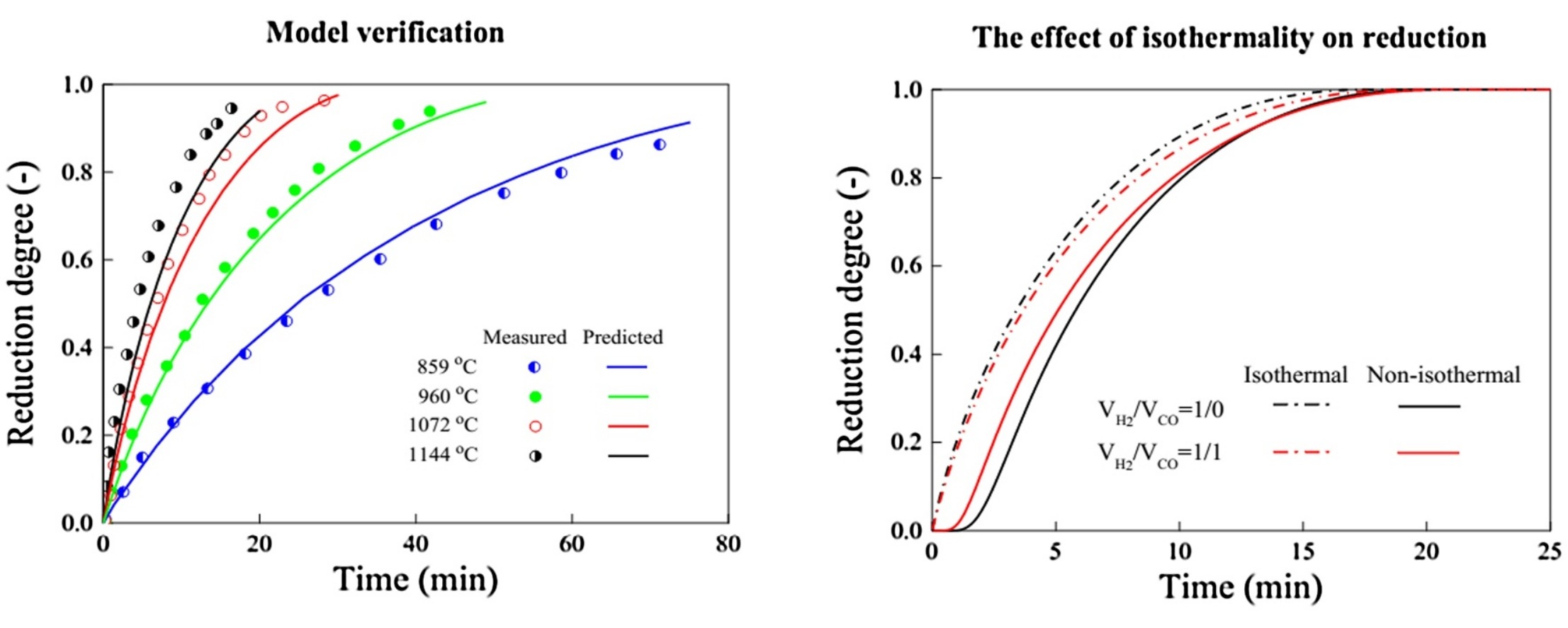