- Volumes 84-95 (2024)
-
Volumes 72-83 (2023)
-
Volume 83
Pages 1-258 (December 2023)
-
Volume 82
Pages 1-204 (November 2023)
-
Volume 81
Pages 1-188 (October 2023)
-
Volume 80
Pages 1-202 (September 2023)
-
Volume 79
Pages 1-172 (August 2023)
-
Volume 78
Pages 1-146 (July 2023)
-
Volume 77
Pages 1-152 (June 2023)
-
Volume 76
Pages 1-176 (May 2023)
-
Volume 75
Pages 1-228 (April 2023)
-
Volume 74
Pages 1-200 (March 2023)
-
Volume 73
Pages 1-138 (February 2023)
-
Volume 72
Pages 1-144 (January 2023)
-
Volume 83
-
Volumes 60-71 (2022)
-
Volume 71
Pages 1-108 (December 2022)
-
Volume 70
Pages 1-106 (November 2022)
-
Volume 69
Pages 1-122 (October 2022)
-
Volume 68
Pages 1-124 (September 2022)
-
Volume 67
Pages 1-102 (August 2022)
-
Volume 66
Pages 1-112 (July 2022)
-
Volume 65
Pages 1-138 (June 2022)
-
Volume 64
Pages 1-186 (May 2022)
-
Volume 63
Pages 1-124 (April 2022)
-
Volume 62
Pages 1-104 (March 2022)
-
Volume 61
Pages 1-120 (February 2022)
-
Volume 60
Pages 1-124 (January 2022)
-
Volume 71
- Volumes 54-59 (2021)
- Volumes 48-53 (2020)
- Volumes 42-47 (2019)
- Volumes 36-41 (2018)
- Volumes 30-35 (2017)
- Volumes 24-29 (2016)
- Volumes 18-23 (2015)
- Volumes 12-17 (2014)
- Volume 11 (2013)
- Volume 10 (2012)
- Volume 9 (2011)
- Volume 8 (2010)
- Volume 7 (2009)
- Volume 6 (2008)
- Volume 5 (2007)
- Volume 4 (2006)
- Volume 3 (2005)
- Volume 2 (2004)
- Volume 1 (2003)
• Two-fluid CFD model is used for simulation of airlift reactor with net draft tube.
• The CFD model properly accounts for geometric effects.
• Gas holdup, liquid velocity and mass transfer coefficient are evaluated in simulations.
• CFD approach leads to more accurate and reasonable results than empirical modelling.
• Complex dynamic behavior of ALR-NDTs is evaluated numerically.
In terms of gas holdup, liquid velocity, and volumetric mass transfer coefficient for oxygen (KLa), the hydrodynamic behavior of four configurations of an airlift reactor (ALR) with a net draft tube (NDT) of different net mesh sizes (ALR-NDT-3, 6, 12, and ALR) have been numerically simulated for a range of inlet air flow rates. The effect of various levels of ratio of height (H) to inner tube diameter (D) of the net draft tube (H/D: 9.3, 10.7, 17.5, and 20) and ratio of inner cross-sectional area of the riser (Ar) to the inner cross sectional area of the downcomer (Ad) (Ad/Ar: 1.3 and 7) for different air flow rates is also evaluated for each reactor configuration operating with an air–water system. The two-fluid formulation coupled with the k–ε turbulence model is used for computational fluid dynamics (CFD) analysis of flow with Eulerian descriptions for the gas and liquid phases. Interactions between air bubbles and liquid are taken into account using momentum exchange and drag coefficient based on two different correlations. Trends in the predicted dynamical behavior are similar to those found experimentally. A good agreement was achieved suggesting that geometric effects are properly accounted for by the CFD model. After a comparison with experimental data, numerical simulations show significant enhanced gas holdup, liquid velocity, and KLa for the ALR-NDTs compared with the conventional ALR. Higher gas holdup values are achieved for ALR-NDT-3 than that for the other ALRs because it acts like a bubble column reactor as the holes present in the NDT are large. Maximum liquid velocities are seen in ALR-NDT-12, which operates like a conventional ALR. Moreover, the interaction between the NDT and upward gas flow leads to cross flow through the net, small bubbles, and high interfacial area as well as good mass transfer. This was significant in ALR-NDT-6 with maximum KLa value of 0.031 s−1. The applied methodology provides an insightful understanding of the complex dynamic behavior of ALR-NDTs and may be helpful in optimizing the design and scale-up of reactors.
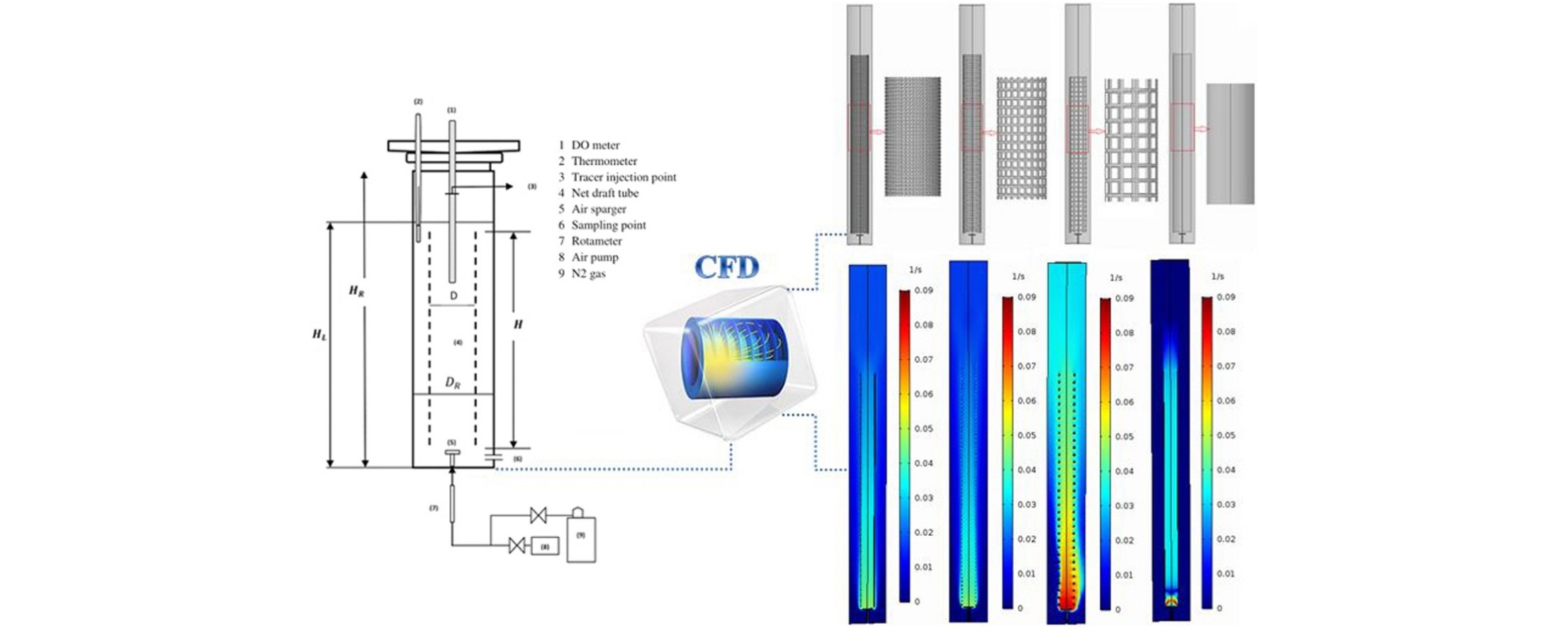