- Volumes 84-95 (2024)
-
Volumes 72-83 (2023)
-
Volume 83
Pages 1-258 (December 2023)
-
Volume 82
Pages 1-204 (November 2023)
-
Volume 81
Pages 1-188 (October 2023)
-
Volume 80
Pages 1-202 (September 2023)
-
Volume 79
Pages 1-172 (August 2023)
-
Volume 78
Pages 1-146 (July 2023)
-
Volume 77
Pages 1-152 (June 2023)
-
Volume 76
Pages 1-176 (May 2023)
-
Volume 75
Pages 1-228 (April 2023)
-
Volume 74
Pages 1-200 (March 2023)
-
Volume 73
Pages 1-138 (February 2023)
-
Volume 72
Pages 1-144 (January 2023)
-
Volume 83
-
Volumes 60-71 (2022)
-
Volume 71
Pages 1-108 (December 2022)
-
Volume 70
Pages 1-106 (November 2022)
-
Volume 69
Pages 1-122 (October 2022)
-
Volume 68
Pages 1-124 (September 2022)
-
Volume 67
Pages 1-102 (August 2022)
-
Volume 66
Pages 1-112 (July 2022)
-
Volume 65
Pages 1-138 (June 2022)
-
Volume 64
Pages 1-186 (May 2022)
-
Volume 63
Pages 1-124 (April 2022)
-
Volume 62
Pages 1-104 (March 2022)
-
Volume 61
Pages 1-120 (February 2022)
-
Volume 60
Pages 1-124 (January 2022)
-
Volume 71
- Volumes 54-59 (2021)
- Volumes 48-53 (2020)
- Volumes 42-47 (2019)
- Volumes 36-41 (2018)
- Volumes 30-35 (2017)
- Volumes 24-29 (2016)
- Volumes 18-23 (2015)
- Volumes 12-17 (2014)
- Volume 11 (2013)
- Volume 10 (2012)
- Volume 9 (2011)
- Volume 8 (2010)
- Volume 7 (2009)
- Volume 6 (2008)
- Volume 5 (2007)
- Volume 4 (2006)
- Volume 3 (2005)
- Volume 2 (2004)
- Volume 1 (2003)
• A robust method to determine the residence time in roll compaction/dry granulation was established based on image analysis.
• The effect of roll and impeller speed in the granulation unit was statistically analyzed in a central composite circumscribed design of experiments.
• The impact of fill level in the hopper of the roll compactor was evaluated and compared to the behavior of continuous feeders/blenders.
• Results were evaluated for the effect they would have on a continuous process with an out-of-specification event.
Knowledge of residence time is a critical aspect in developing control and material diversion strategies for continuous manufacturing processes in pharmaceutical manufacturing. Dry granulation is a promising continuous granulation technique as it is fast and economical. In this study, a step-change method to determine residence time in roll compaction/dry granulation is introduced. The factors roll speed and rotational speed of the impeller in the powder inlet unit of the compactor were evaluated using a central composite circumscribed statistical design of experiments in order to optimize the residence time. The fill volume in the compactor was varied exemplarily. It was found that high roll speed, low rotational speed of the impeller and low fill volume in the compactor are beneficial to generate fast transition through the compactor. The impact of roll speed increase was estimated. It can be concluded that despite fast residence time in the process, high roll speed and its subsequent high material throughput can generate a large amount of material that has to be discarded if material diversion is required.
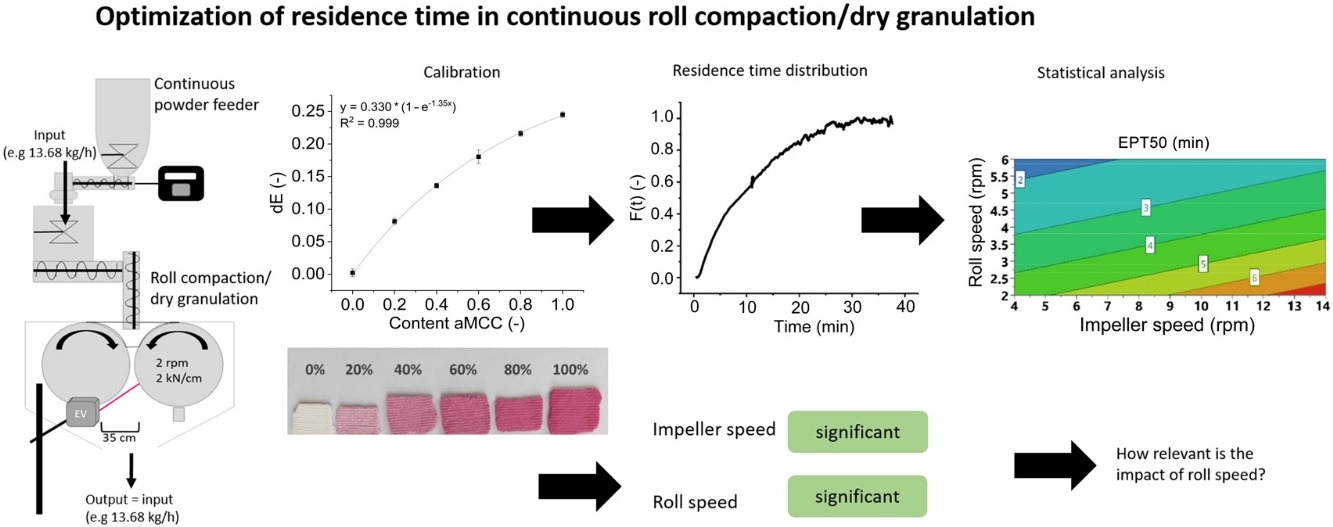