- Volumes 84-95 (2024)
-
Volumes 72-83 (2023)
-
Volume 83
Pages 1-258 (December 2023)
-
Volume 82
Pages 1-204 (November 2023)
-
Volume 81
Pages 1-188 (October 2023)
-
Volume 80
Pages 1-202 (September 2023)
-
Volume 79
Pages 1-172 (August 2023)
-
Volume 78
Pages 1-146 (July 2023)
-
Volume 77
Pages 1-152 (June 2023)
-
Volume 76
Pages 1-176 (May 2023)
-
Volume 75
Pages 1-228 (April 2023)
-
Volume 74
Pages 1-200 (March 2023)
-
Volume 73
Pages 1-138 (February 2023)
-
Volume 72
Pages 1-144 (January 2023)
-
Volume 83
-
Volumes 60-71 (2022)
-
Volume 71
Pages 1-108 (December 2022)
-
Volume 70
Pages 1-106 (November 2022)
-
Volume 69
Pages 1-122 (October 2022)
-
Volume 68
Pages 1-124 (September 2022)
-
Volume 67
Pages 1-102 (August 2022)
-
Volume 66
Pages 1-112 (July 2022)
-
Volume 65
Pages 1-138 (June 2022)
-
Volume 64
Pages 1-186 (May 2022)
-
Volume 63
Pages 1-124 (April 2022)
-
Volume 62
Pages 1-104 (March 2022)
-
Volume 61
Pages 1-120 (February 2022)
-
Volume 60
Pages 1-124 (January 2022)
-
Volume 71
- Volumes 54-59 (2021)
- Volumes 48-53 (2020)
- Volumes 42-47 (2019)
- Volumes 36-41 (2018)
- Volumes 30-35 (2017)
- Volumes 24-29 (2016)
- Volumes 18-23 (2015)
- Volumes 12-17 (2014)
- Volume 11 (2013)
- Volume 10 (2012)
- Volume 9 (2011)
- Volume 8 (2010)
- Volume 7 (2009)
- Volume 6 (2008)
- Volume 5 (2007)
- Volume 4 (2006)
- Volume 3 (2005)
- Volume 2 (2004)
- Volume 1 (2003)
• Conveying of spherical and non-spherical granular materials is simulated by DEM.
• Effect of particle shape on conveying performance is investigated.
• Possibility of particle breakage in collisions is predicted using collision energy.
• Wear rate of screw blade is obtained by SIEM based on DEM.
Screw conveyors are extensively used in modern industry such as metallurgy, architecture and pharmaceutical due to their high-efficiency in the transportation of granular materials. And substantial efforts have been devoted to the study of the screw conveyors. Numerical method is an effective way to study screw conveyor. However, previous studies have mainly focused in the regime of spherical particles while the in-depth investigations for non-spherical particles that should be the most encountered in practical applications are still limited. In view of the above situations, discrete element method (DEM), which has been widely accepted in simulating the discrete systems, is utilized to investigate the conveying process of non-spherical particles in a horizontal screw conveyor, with particles being modeled by super-ellipsoids. In addition, a wear model called SIEM (Shear Impact Energy Model) is incorporated into DEM to predict the wear of screw conveyor. The DEM simulation results demonstrate that the particle shape is influential for the flow behaviors of particles and the wear of conveyor. The conveying performance evaluated quantitatively of both mass flow rate and power consumption is subsequently obtained to investigate the effect of sphericity of particle with different operation parameters. Moreover, particle collision frequency and collision energy consumption are acquired to investigate the possible particle breakage between particles and screw blade. The comparisons between particle–particle collision and particle–wall collision reveal that particles with large shape index have more possibility to be damaged in particle–wall impingement.
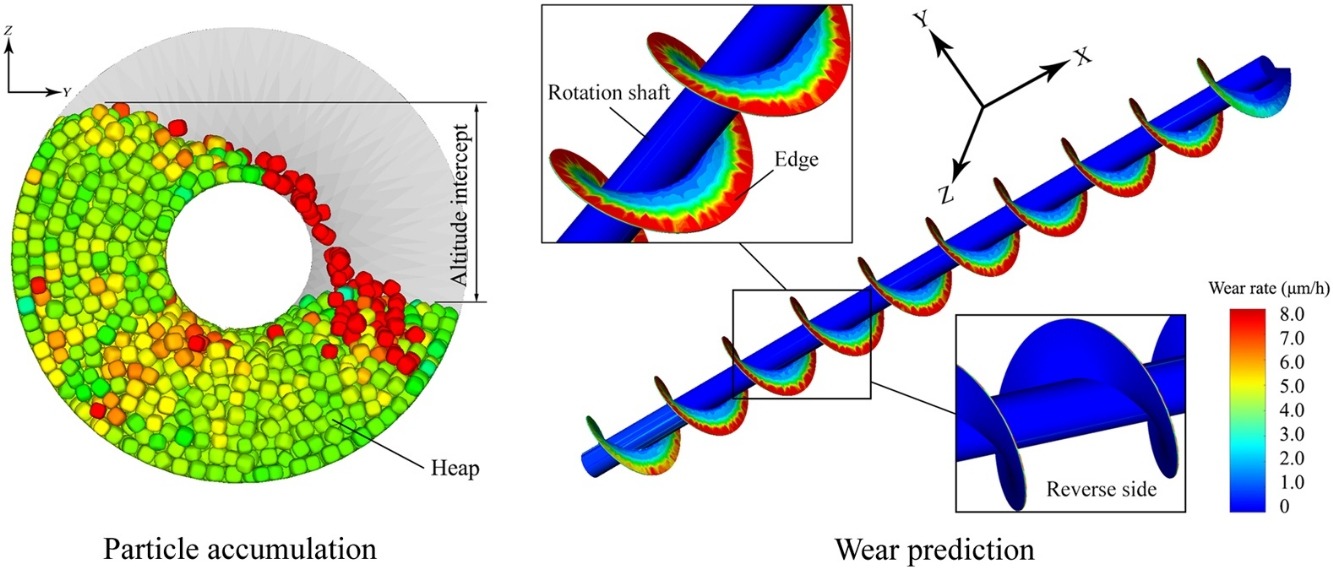