- Volumes 84-95 (2024)
-
Volumes 72-83 (2023)
-
Volume 83
Pages 1-258 (December 2023)
-
Volume 82
Pages 1-204 (November 2023)
-
Volume 81
Pages 1-188 (October 2023)
-
Volume 80
Pages 1-202 (September 2023)
-
Volume 79
Pages 1-172 (August 2023)
-
Volume 78
Pages 1-146 (July 2023)
-
Volume 77
Pages 1-152 (June 2023)
-
Volume 76
Pages 1-176 (May 2023)
-
Volume 75
Pages 1-228 (April 2023)
-
Volume 74
Pages 1-200 (March 2023)
-
Volume 73
Pages 1-138 (February 2023)
-
Volume 72
Pages 1-144 (January 2023)
-
Volume 83
-
Volumes 60-71 (2022)
-
Volume 71
Pages 1-108 (December 2022)
-
Volume 70
Pages 1-106 (November 2022)
-
Volume 69
Pages 1-122 (October 2022)
-
Volume 68
Pages 1-124 (September 2022)
-
Volume 67
Pages 1-102 (August 2022)
-
Volume 66
Pages 1-112 (July 2022)
-
Volume 65
Pages 1-138 (June 2022)
-
Volume 64
Pages 1-186 (May 2022)
-
Volume 63
Pages 1-124 (April 2022)
-
Volume 62
Pages 1-104 (March 2022)
-
Volume 61
Pages 1-120 (February 2022)
-
Volume 60
Pages 1-124 (January 2022)
-
Volume 71
- Volumes 54-59 (2021)
- Volumes 48-53 (2020)
- Volumes 42-47 (2019)
- Volumes 36-41 (2018)
- Volumes 30-35 (2017)
- Volumes 24-29 (2016)
- Volumes 18-23 (2015)
- Volumes 12-17 (2014)
- Volume 11 (2013)
- Volume 10 (2012)
- Volume 9 (2011)
- Volume 8 (2010)
- Volume 7 (2009)
- Volume 6 (2008)
- Volume 5 (2007)
- Volume 4 (2006)
- Volume 3 (2005)
- Volume 2 (2004)
- Volume 1 (2003)
• Movement trajectory of particles in roller-spreading is more complicated.
• Particles have relatively weak dispersion in blade-spreading.
• Spreading methods affect particle segregation and powder layer density.
• Higher density can be obtained by roller-spreading at thicker powder layer.
• Blade-spreading limits its application to thicker powder layer.
The roller-spreading and blade-spreading are main powder spreading methods in powder-bed additive manufacturing. The discrete element method was introduced to simulate nylon powder spreading by both roller and blade spreaders. The two spreading processes were compared from several aspects including particle flow behavior, particle contact forces, forces exerted on spreaders, particle segregation and powder layer density. It is found that powder spreading methods mainly affect the movement trajectory of particles, particle contact forces and forces exerted on spreaders. Complicated dispersion and circulation movement of particles occur inside the powder pile by roller-spreading, while particles have relatively weak dispersion by the blade-spreading. The normal force applied to the roller introduces a compacting effect on the powder pile and creates strong force chains that distribute uniformly in the powder pile. Therefore, the powder bed with higher density can be obtained by roller-spreading in thicker powder layer due to the compacting effect. The blade spreader sustains tangential force mainly, so the blade-spreading process limits its application to thicker powder layer. As the powder layer thickness increases, the roller-spreading is more sensitive to segregation index than that of the blade-spreading. The comprehensive comparison of two spreading processes provides criteria for selecting spreading methods.
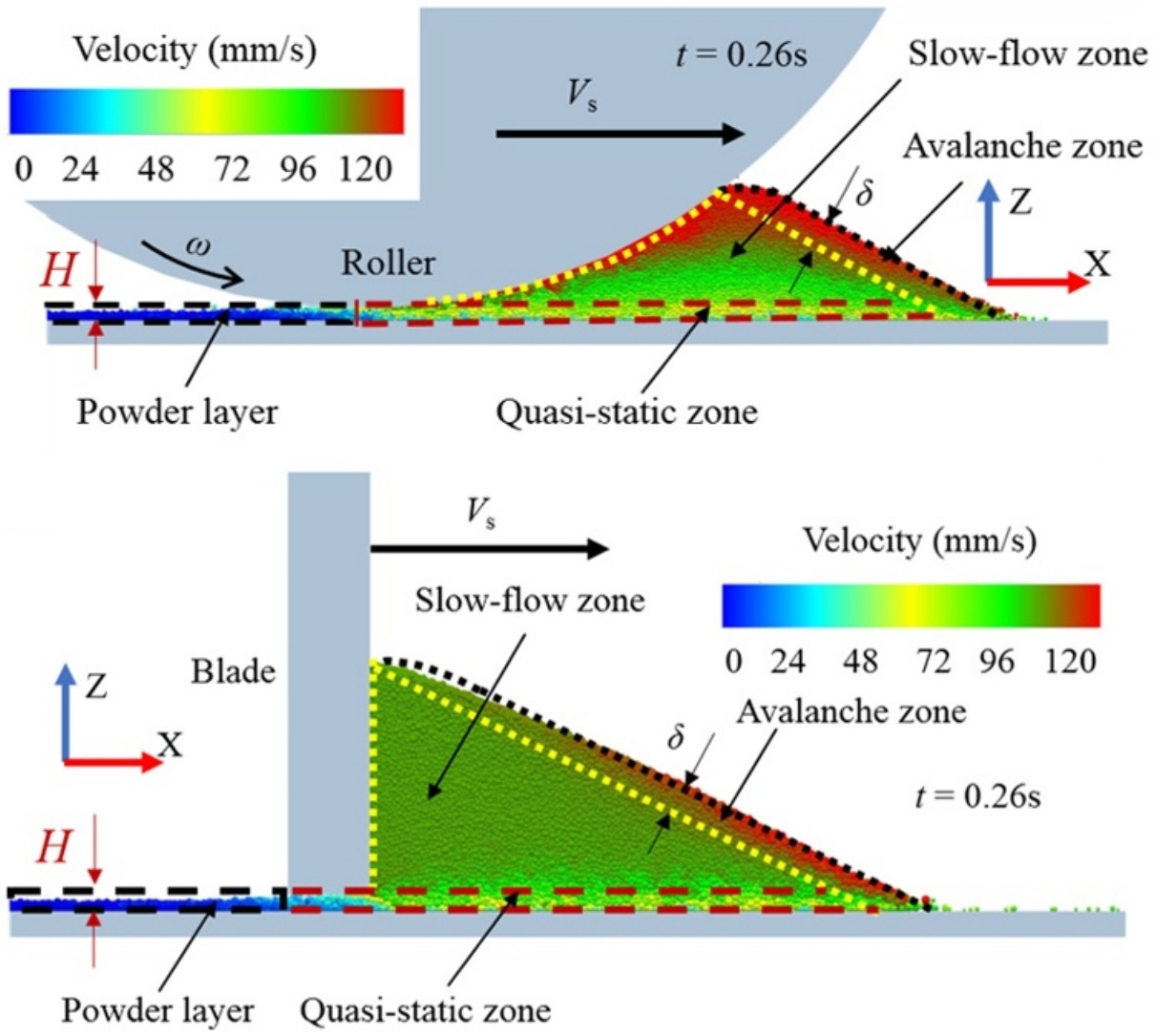