- Volumes 84-95 (2024)
-
Volumes 72-83 (2023)
-
Volume 83
Pages 1-258 (December 2023)
-
Volume 82
Pages 1-204 (November 2023)
-
Volume 81
Pages 1-188 (October 2023)
-
Volume 80
Pages 1-202 (September 2023)
-
Volume 79
Pages 1-172 (August 2023)
-
Volume 78
Pages 1-146 (July 2023)
-
Volume 77
Pages 1-152 (June 2023)
-
Volume 76
Pages 1-176 (May 2023)
-
Volume 75
Pages 1-228 (April 2023)
-
Volume 74
Pages 1-200 (March 2023)
-
Volume 73
Pages 1-138 (February 2023)
-
Volume 72
Pages 1-144 (January 2023)
-
Volume 83
-
Volumes 60-71 (2022)
-
Volume 71
Pages 1-108 (December 2022)
-
Volume 70
Pages 1-106 (November 2022)
-
Volume 69
Pages 1-122 (October 2022)
-
Volume 68
Pages 1-124 (September 2022)
-
Volume 67
Pages 1-102 (August 2022)
-
Volume 66
Pages 1-112 (July 2022)
-
Volume 65
Pages 1-138 (June 2022)
-
Volume 64
Pages 1-186 (May 2022)
-
Volume 63
Pages 1-124 (April 2022)
-
Volume 62
Pages 1-104 (March 2022)
-
Volume 61
Pages 1-120 (February 2022)
-
Volume 60
Pages 1-124 (January 2022)
-
Volume 71
- Volumes 54-59 (2021)
- Volumes 48-53 (2020)
- Volumes 42-47 (2019)
- Volumes 36-41 (2018)
- Volumes 30-35 (2017)
- Volumes 24-29 (2016)
- Volumes 18-23 (2015)
- Volumes 12-17 (2014)
- Volume 11 (2013)
- Volume 10 (2012)
- Volume 9 (2011)
- Volume 8 (2010)
- Volume 7 (2009)
- Volume 6 (2008)
- Volume 5 (2007)
- Volume 4 (2006)
- Volume 3 (2005)
- Volume 2 (2004)
- Volume 1 (2003)
• Lacy cylinder drum and lacy-lifter cylinder drum are designed and particle behavior is investigated.
• Rheological characteristics in cylinder drum, lacy cylinder drum and lacy-lifter cylinder drum are compared.
• Active layer thickness is decreased and the particle exchange is inhibited by lifters.
• Particle mixing quality is improved by the lacy drum wall and lifters.
The optimization of the drum structure is beneficial to improve the particle motion and mixing in rotary drums. In this work, two kinds of drum structures, Lacy cylinder drum (LC) and Lacy-lifters cylinder drum (LLC), are developed on the basic of cylinder drum to enhance the heat transfer area. The particle motion and mixing process are simulated by DEM method. Based on the grid independence and model validation, the contact number between particles and wall, particle velocity profile, thickness of active layer, particle exchange coefficient, particle concentration profile and mixing index are demonstrated. The influences of the drum structure and the operation parameters are further evaluated. The results show that the contact number between particles and wall is improved in LC and LLC compared to cylinder drum. The particle velocity in LC is higher than that in cylinder drum at high rotating speed, and the particle velocity of the particle falling region is significantly improved in LLC. Compared to cylinder drum and LC, the thickness of active layer in LLC is smaller, while the local particle mixing quality is proved to be the best in the active region. In addition, the particle exchange coefficients between static region and active region in the three drums are compared and LLC is found tending to weaken the particle flow. Besides, the fluctuations of particle concentration in the active region, static region, and boundary region are weakened in LLC, and the equilibrium state is reached earlier. In addition, the overall particle mixing performance in cylinder drum, LC and LLC is analyzed. The particle mixing performance in cylinder drum is the worst, while the difference in mixing quality of LC and LLC depends on the operation conditions.
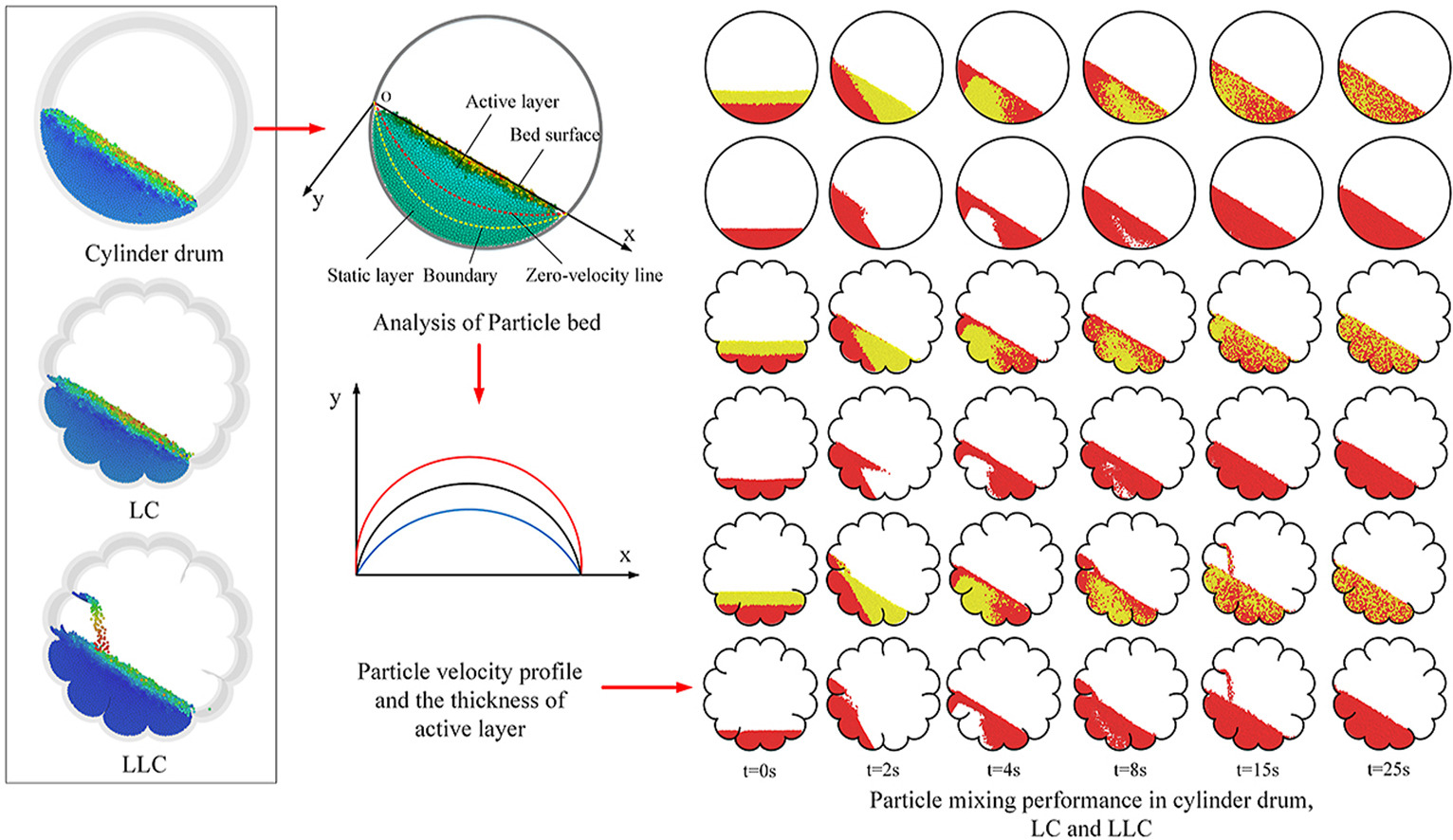