- Volumes 84-95 (2024)
-
Volumes 72-83 (2023)
-
Volume 83
Pages 1-258 (December 2023)
-
Volume 82
Pages 1-204 (November 2023)
-
Volume 81
Pages 1-188 (October 2023)
-
Volume 80
Pages 1-202 (September 2023)
-
Volume 79
Pages 1-172 (August 2023)
-
Volume 78
Pages 1-146 (July 2023)
-
Volume 77
Pages 1-152 (June 2023)
-
Volume 76
Pages 1-176 (May 2023)
-
Volume 75
Pages 1-228 (April 2023)
-
Volume 74
Pages 1-200 (March 2023)
-
Volume 73
Pages 1-138 (February 2023)
-
Volume 72
Pages 1-144 (January 2023)
-
Volume 83
-
Volumes 60-71 (2022)
-
Volume 71
Pages 1-108 (December 2022)
-
Volume 70
Pages 1-106 (November 2022)
-
Volume 69
Pages 1-122 (October 2022)
-
Volume 68
Pages 1-124 (September 2022)
-
Volume 67
Pages 1-102 (August 2022)
-
Volume 66
Pages 1-112 (July 2022)
-
Volume 65
Pages 1-138 (June 2022)
-
Volume 64
Pages 1-186 (May 2022)
-
Volume 63
Pages 1-124 (April 2022)
-
Volume 62
Pages 1-104 (March 2022)
-
Volume 61
Pages 1-120 (February 2022)
-
Volume 60
Pages 1-124 (January 2022)
-
Volume 71
- Volumes 54-59 (2021)
- Volumes 48-53 (2020)
- Volumes 42-47 (2019)
- Volumes 36-41 (2018)
- Volumes 30-35 (2017)
- Volumes 24-29 (2016)
- Volumes 18-23 (2015)
- Volumes 12-17 (2014)
- Volume 11 (2013)
- Volume 10 (2012)
- Volume 9 (2011)
- Volume 8 (2010)
- Volume 7 (2009)
- Volume 6 (2008)
- Volume 5 (2007)
- Volume 4 (2006)
- Volume 3 (2005)
- Volume 2 (2004)
- Volume 1 (2003)
• A spray fluidized bed of coating process is simulated by a CFD-DEM model.
• Cycle time distribution of particles becomes narrower by optimizing bed structure.
• Coating uniformity is improved as cycle time distribution becomes narrower.
• Properly increasing gas velocity and temperature the coating uniformity increases.
• Properly reducing liquid spray rate the coating uniformity increases.
Cycle Time Distribution (CTD) plays a critical role for determining uniformity of particle coating in spray fluidized beds. However, the CTD is influenced by both geometrical structure and operating conditions of fluidized bed. In this study, a spray fluidized bed of coating process is simulated by a comprehensive Computational Fluid Dynamics-Discrete Element Model (CFD-DEM). To achieve different behaviors of CTD, some modifications are designed on a pseudo-2D internally circulating fluidized bed, which traditionally composes of a high-velocity upward bed and low-velocity downward bed. These modifications include making the air distributor slope and/or laying a baffle in the downward bed. First, the CTD and evolution of particle size distribution under different bed structures are compared. The CTD directly influences the coating uniformity. By making the particles flowing along a parallel direction in the downward bed through the geometrical modifications, the CTD becomes narrower and the coating uniformity is significantly improved. Second, under the optimized bed structure, the influence of operating conditions on the coating uniformity is studied. Properly increasing the fluidization gas velocity and the fluidization gas temperature and reducing the liquid spray rate can improve the coating uniformity.
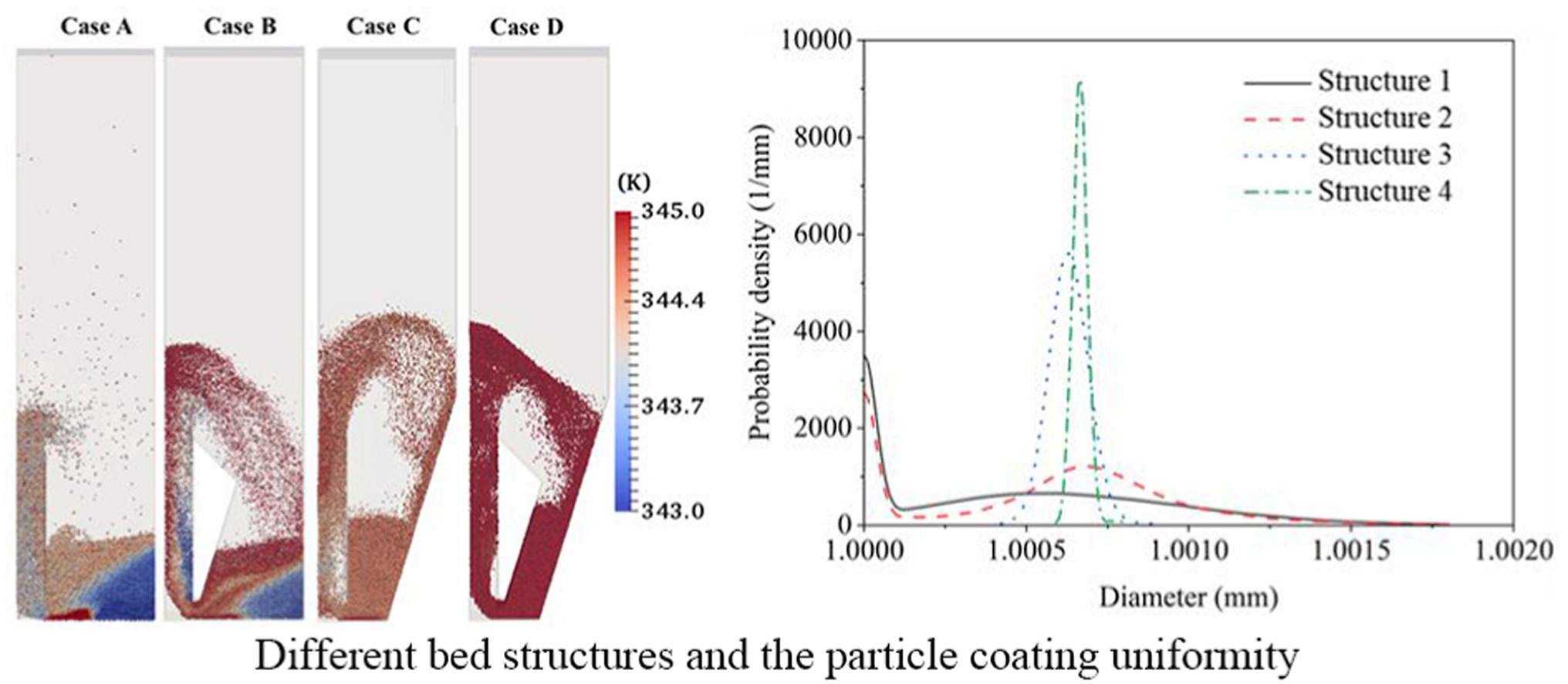