- Volumes 84-95 (2024)
-
Volumes 72-83 (2023)
-
Volume 83
Pages 1-258 (December 2023)
-
Volume 82
Pages 1-204 (November 2023)
-
Volume 81
Pages 1-188 (October 2023)
-
Volume 80
Pages 1-202 (September 2023)
-
Volume 79
Pages 1-172 (August 2023)
-
Volume 78
Pages 1-146 (July 2023)
-
Volume 77
Pages 1-152 (June 2023)
-
Volume 76
Pages 1-176 (May 2023)
-
Volume 75
Pages 1-228 (April 2023)
-
Volume 74
Pages 1-200 (March 2023)
-
Volume 73
Pages 1-138 (February 2023)
-
Volume 72
Pages 1-144 (January 2023)
-
Volume 83
-
Volumes 60-71 (2022)
-
Volume 71
Pages 1-108 (December 2022)
-
Volume 70
Pages 1-106 (November 2022)
-
Volume 69
Pages 1-122 (October 2022)
-
Volume 68
Pages 1-124 (September 2022)
-
Volume 67
Pages 1-102 (August 2022)
-
Volume 66
Pages 1-112 (July 2022)
-
Volume 65
Pages 1-138 (June 2022)
-
Volume 64
Pages 1-186 (May 2022)
-
Volume 63
Pages 1-124 (April 2022)
-
Volume 62
Pages 1-104 (March 2022)
-
Volume 61
Pages 1-120 (February 2022)
-
Volume 60
Pages 1-124 (January 2022)
-
Volume 71
- Volumes 54-59 (2021)
- Volumes 48-53 (2020)
- Volumes 42-47 (2019)
- Volumes 36-41 (2018)
- Volumes 30-35 (2017)
- Volumes 24-29 (2016)
- Volumes 18-23 (2015)
- Volumes 12-17 (2014)
- Volume 11 (2013)
- Volume 10 (2012)
- Volume 9 (2011)
- Volume 8 (2010)
- Volume 7 (2009)
- Volume 6 (2008)
- Volume 5 (2007)
- Volume 4 (2006)
- Volume 3 (2005)
- Volume 2 (2004)
- Volume 1 (2003)
• A novel approach is proposed for phase change of iron ore particle simulation.
• The model is extensively tested against available experimental data.
• Phase change of inner iron ore particle is resolved in time and space.
• Effects of key operating parameters on the phase change activities are analyzed.
Cohesive zone plays a vital role in the stable operation of a blast furnace (BF), yet the complex phase change process of iron ore particles in this zone is still not well understood. In this study, a novel one-dimensional (1D) unsteady phase change model was developed to elucidate the heat transfer and melting mechanisms of iron ore particles. After model validation, the effects of several key operating parameters (e.g., particle diameter, gas velocity, initial temperature) on the phase change behavior of iron ore particles were analyzed, and the joint effect of multiple parameters was discussed. The results show that larger-sized iron ore particles possess lower specific surface areas, which in turn reduces their convective heat absorption capacity. Consequently, the distance from the solid-liquid phase interface to the particle surface increases, thereby slowing down the movement of the phase interface and prolonging the melting duration of the particles. Increasing the gas velocity and the initial temperature does not have a significant impact on reducing the duration of the complete melting process. Under the specified conditions, it is observed that increasing the gas velocity by 3-fold and 9-fold results in a reduction of the melting duration by 2.4% and 8.3%, respectively. Elevating the initial temperature of iron ore particles results in a decrease in the core-to-surface temperature difference, a slower heating rate, and a shorter duration to achieve melting. Among the factors affecting the melting process, the particle diameter is found to be the most significant in terms of the liquid phase precipitation, mushy zone thickness, and core-to-surface temperature difference of iron ore particles.
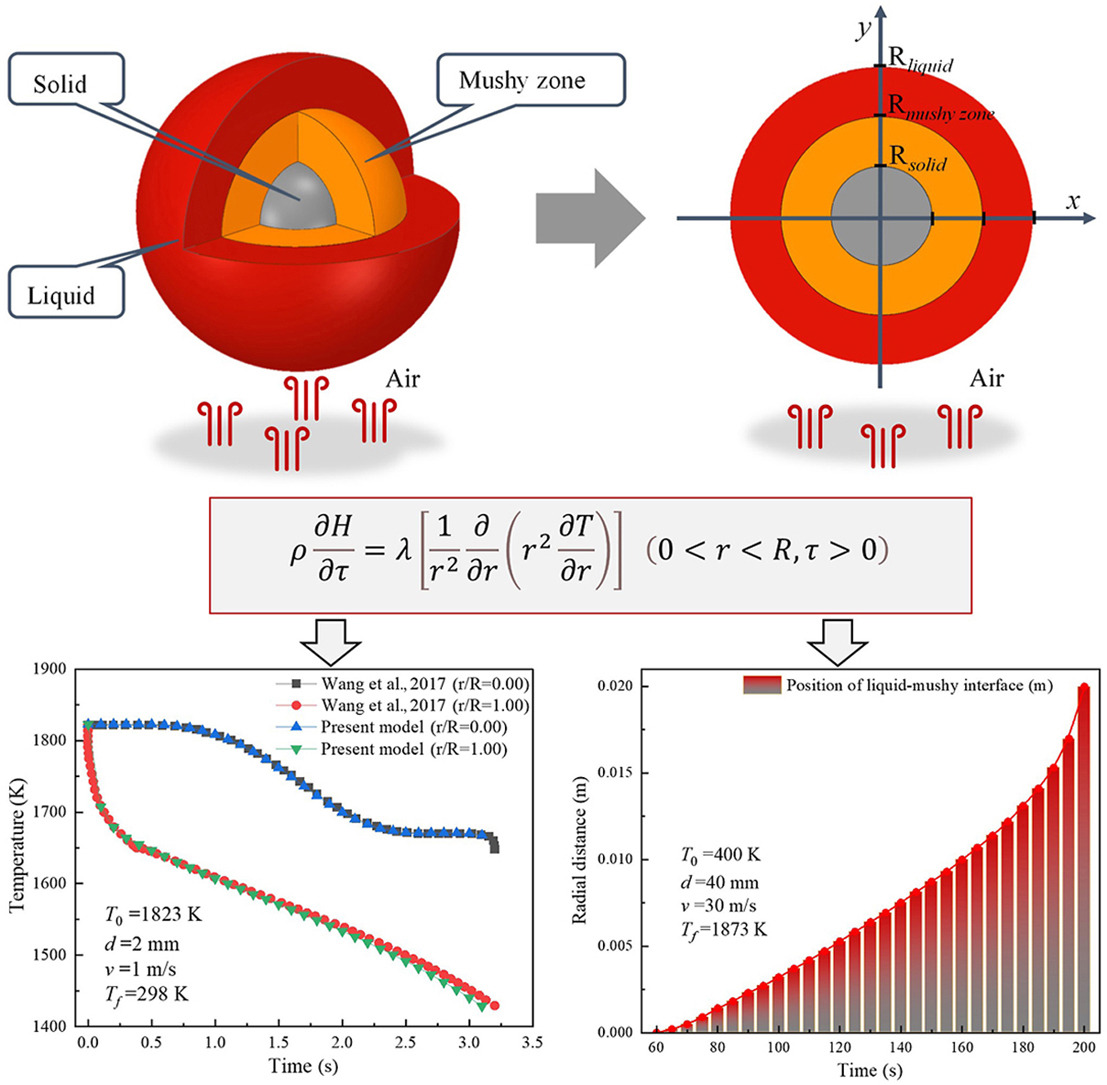