- Volumes 84-95 (2024)
-
Volumes 72-83 (2023)
-
Volume 83
Pages 1-258 (December 2023)
-
Volume 82
Pages 1-204 (November 2023)
-
Volume 81
Pages 1-188 (October 2023)
-
Volume 80
Pages 1-202 (September 2023)
-
Volume 79
Pages 1-172 (August 2023)
-
Volume 78
Pages 1-146 (July 2023)
-
Volume 77
Pages 1-152 (June 2023)
-
Volume 76
Pages 1-176 (May 2023)
-
Volume 75
Pages 1-228 (April 2023)
-
Volume 74
Pages 1-200 (March 2023)
-
Volume 73
Pages 1-138 (February 2023)
-
Volume 72
Pages 1-144 (January 2023)
-
Volume 83
-
Volumes 60-71 (2022)
-
Volume 71
Pages 1-108 (December 2022)
-
Volume 70
Pages 1-106 (November 2022)
-
Volume 69
Pages 1-122 (October 2022)
-
Volume 68
Pages 1-124 (September 2022)
-
Volume 67
Pages 1-102 (August 2022)
-
Volume 66
Pages 1-112 (July 2022)
-
Volume 65
Pages 1-138 (June 2022)
-
Volume 64
Pages 1-186 (May 2022)
-
Volume 63
Pages 1-124 (April 2022)
-
Volume 62
Pages 1-104 (March 2022)
-
Volume 61
Pages 1-120 (February 2022)
-
Volume 60
Pages 1-124 (January 2022)
-
Volume 71
- Volumes 54-59 (2021)
- Volumes 48-53 (2020)
- Volumes 42-47 (2019)
- Volumes 36-41 (2018)
- Volumes 30-35 (2017)
- Volumes 24-29 (2016)
- Volumes 18-23 (2015)
- Volumes 12-17 (2014)
- Volume 11 (2013)
- Volume 10 (2012)
- Volume 9 (2011)
- Volume 8 (2010)
- Volume 7 (2009)
- Volume 6 (2008)
- Volume 5 (2007)
- Volume 4 (2006)
- Volume 3 (2005)
- Volume 2 (2004)
- Volume 1 (2003)
• A triaxial vibration method of particle size distribution (PSD) characterization in gas‒solid flow is proposed.
• A model for the vibration energy variations with particle size and shape is found.
• The best frequency features are found for PSD calculation in multiple directions.
• The particle number and its vibration energy are estimated with good accuracy.
A novel triaxial vibration method is developed for the real-time characterization of the solid particle size distribution (PSD) in pneumatic particulate flow, which is critical for chemical industry. In this work, the particle‒wall collision and friction behaviours were analysed by the time-domain statistical and time-frequency joint methods to narrow the high-frequency response range by the initial experiment of free fall for a single particle, interparticle, and multiple particles. Subsequently, verification experiments of PSD characterization in pneumatic flow were performed. First, the quantitative triaxial energy response model that considers the particle size, shape, and mass factors were established. Second, a good agreement of the particle number identification was found between the triaxial vibration energy and mean particle size of 150–550 μm. Moreover, the performance with the best accuracy was focused on a range of 42–43 kHz in the x-axis and z-axis and 36.8–38.8 kHz in the y-axis. Finally, the individual particle energy was inversely analysed by the triaxial vibration response within the optimized frequency bands, and the PSD was characterized in real-time by a low error rate, that is, 5.2% from the XZ-axis direction of sand (42–43 kHz) and 5.6% from the XYZ-axis of glass (30.9–33.9 kHz, 46.2–47.2 kHz, 38.3–41.3 kHz for each axis response). Therefore, this research complements the existing approaches for PSD characterization in particulate multiphase flow.
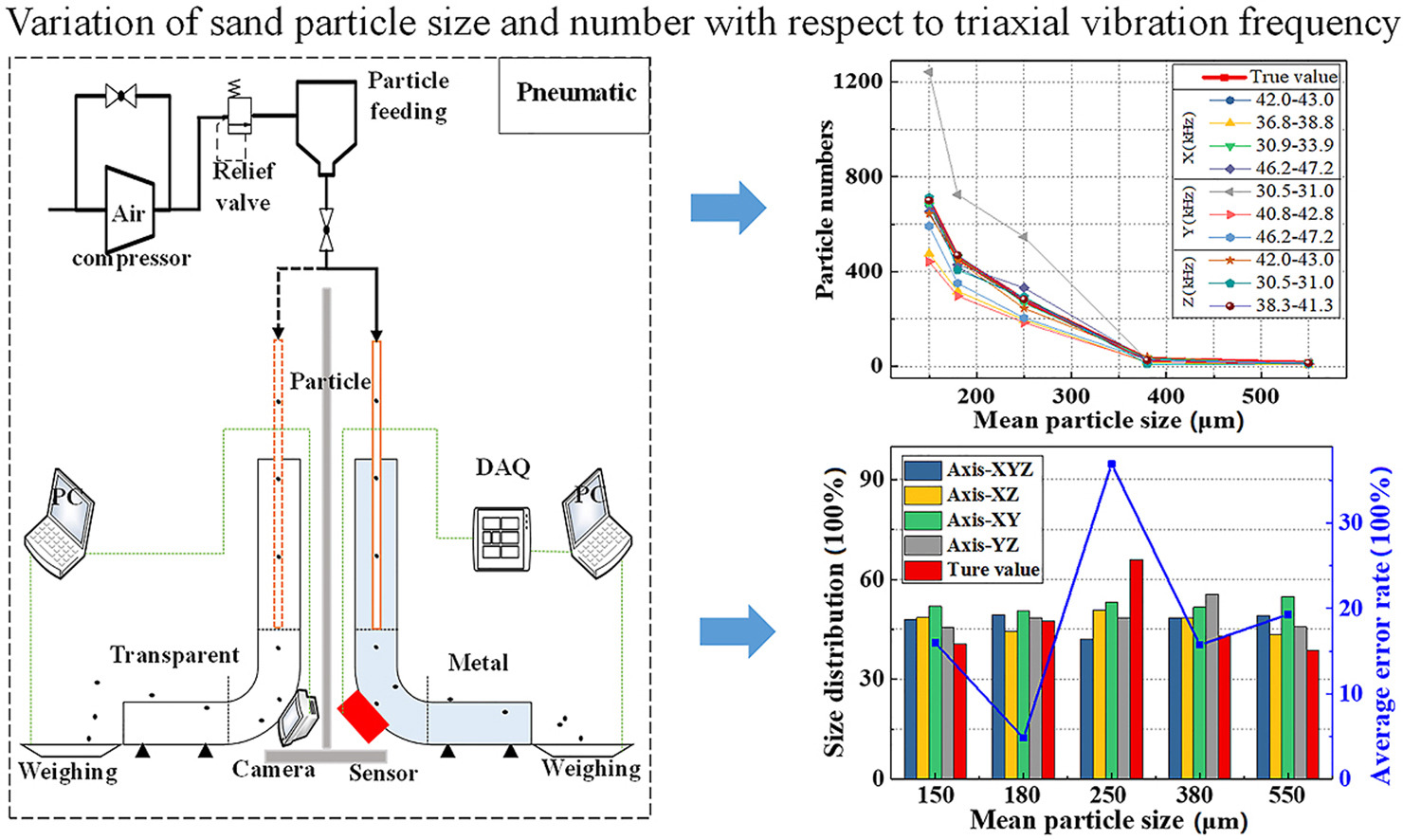