- Volumes 84-95 (2024)
-
Volumes 72-83 (2023)
-
Volume 83
Pages 1-258 (December 2023)
-
Volume 82
Pages 1-204 (November 2023)
-
Volume 81
Pages 1-188 (October 2023)
-
Volume 80
Pages 1-202 (September 2023)
-
Volume 79
Pages 1-172 (August 2023)
-
Volume 78
Pages 1-146 (July 2023)
-
Volume 77
Pages 1-152 (June 2023)
-
Volume 76
Pages 1-176 (May 2023)
-
Volume 75
Pages 1-228 (April 2023)
-
Volume 74
Pages 1-200 (March 2023)
-
Volume 73
Pages 1-138 (February 2023)
-
Volume 72
Pages 1-144 (January 2023)
-
Volume 83
-
Volumes 60-71 (2022)
-
Volume 71
Pages 1-108 (December 2022)
-
Volume 70
Pages 1-106 (November 2022)
-
Volume 69
Pages 1-122 (October 2022)
-
Volume 68
Pages 1-124 (September 2022)
-
Volume 67
Pages 1-102 (August 2022)
-
Volume 66
Pages 1-112 (July 2022)
-
Volume 65
Pages 1-138 (June 2022)
-
Volume 64
Pages 1-186 (May 2022)
-
Volume 63
Pages 1-124 (April 2022)
-
Volume 62
Pages 1-104 (March 2022)
-
Volume 61
Pages 1-120 (February 2022)
-
Volume 60
Pages 1-124 (January 2022)
-
Volume 71
- Volumes 54-59 (2021)
- Volumes 48-53 (2020)
- Volumes 42-47 (2019)
- Volumes 36-41 (2018)
- Volumes 30-35 (2017)
- Volumes 24-29 (2016)
- Volumes 18-23 (2015)
- Volumes 12-17 (2014)
- Volume 11 (2013)
- Volume 10 (2012)
- Volume 9 (2011)
- Volume 8 (2010)
- Volume 7 (2009)
- Volume 6 (2008)
- Volume 5 (2007)
- Volume 4 (2006)
- Volume 3 (2005)
- Volume 2 (2004)
- Volume 1 (2003)
• Gravity-driven vibration-based approach to improve the flow of dry particles.
• A minimum amount of vibration is required to break the arch formed inside the hopper.
• Optimal vibration intensity is required to achieve a maximum mass flow rate.
• High vibration intensity restricts particle travel in the flow direction.
The controlled and homogeneous flow of dry granular powders through hoppers is essential for applications, namely, packaging of food grains, fertilizers and additive manufacturing processes such as directed energy deposition for better product quality. One of the major issues encountered in the granular flows through hoppers is flow stagnation due to the well-known arching phenomenon. Vibration-assisted granular flow through hoppers is one of the mechanisms used for better mass flow control. In this work, the influence of external mechanical vibration on the powder flow is investigated experimentally and using discrete element simulations. First, the mass flow rate through the hopper increases with an increase in vibration amplitude and then decreases, signifying the existence of an optimal amplitude of vibration. The DEM simulations explained the underlying mechanisms for the existence of an optimal amplitude of vibration corresponding to the maximum mass flow rate. A range of vibration amplitudes from 0 mm to 3.5 mm is used to study the flow behaviour; the maximum flow of around 33 g/s to 35 g/s is observed for 0.75 mm to 1.25 mm vibration amplitude for the hopper-particle combination studied in this work. The work also reports the influence of vibration frequency, hopper, and particle dimension on the flow characteristics. The research facilitates the effective use of mechanical vibration to enhance powder flow that can further be extended to non-spherical and multi-material particles.
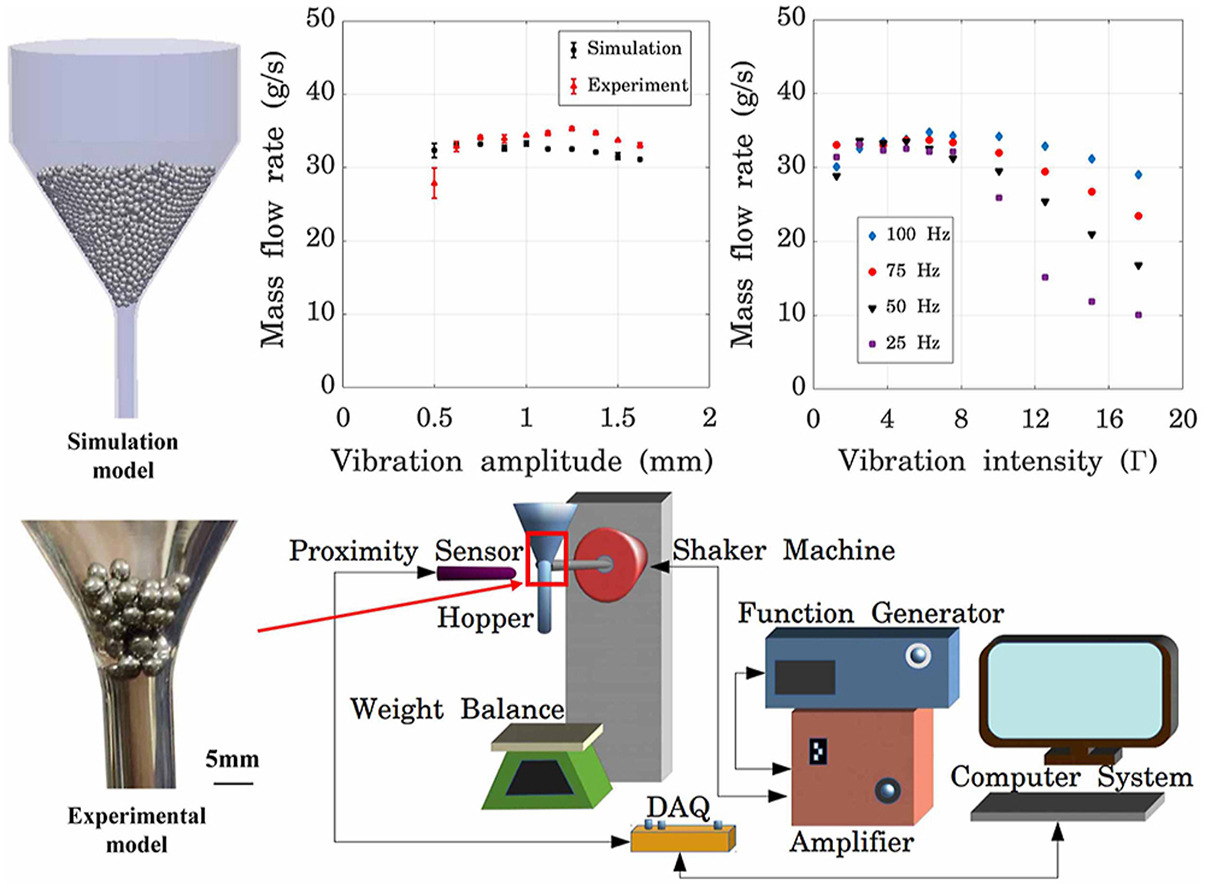