- Volumes 84-95 (2024)
-
Volumes 72-83 (2023)
-
Volume 83
Pages 1-258 (December 2023)
-
Volume 82
Pages 1-204 (November 2023)
-
Volume 81
Pages 1-188 (October 2023)
-
Volume 80
Pages 1-202 (September 2023)
-
Volume 79
Pages 1-172 (August 2023)
-
Volume 78
Pages 1-146 (July 2023)
-
Volume 77
Pages 1-152 (June 2023)
-
Volume 76
Pages 1-176 (May 2023)
-
Volume 75
Pages 1-228 (April 2023)
-
Volume 74
Pages 1-200 (March 2023)
-
Volume 73
Pages 1-138 (February 2023)
-
Volume 72
Pages 1-144 (January 2023)
-
Volume 83
-
Volumes 60-71 (2022)
-
Volume 71
Pages 1-108 (December 2022)
-
Volume 70
Pages 1-106 (November 2022)
-
Volume 69
Pages 1-122 (October 2022)
-
Volume 68
Pages 1-124 (September 2022)
-
Volume 67
Pages 1-102 (August 2022)
-
Volume 66
Pages 1-112 (July 2022)
-
Volume 65
Pages 1-138 (June 2022)
-
Volume 64
Pages 1-186 (May 2022)
-
Volume 63
Pages 1-124 (April 2022)
-
Volume 62
Pages 1-104 (March 2022)
-
Volume 61
Pages 1-120 (February 2022)
-
Volume 60
Pages 1-124 (January 2022)
-
Volume 71
- Volumes 54-59 (2021)
- Volumes 48-53 (2020)
- Volumes 42-47 (2019)
- Volumes 36-41 (2018)
- Volumes 30-35 (2017)
- Volumes 24-29 (2016)
- Volumes 18-23 (2015)
- Volumes 12-17 (2014)
- Volume 11 (2013)
- Volume 10 (2012)
- Volume 9 (2011)
- Volume 8 (2010)
- Volume 7 (2009)
- Volume 6 (2008)
- Volume 5 (2007)
- Volume 4 (2006)
- Volume 3 (2005)
- Volume 2 (2004)
- Volume 1 (2003)
• Systematically study the impact of using DEM on measurement accuracy.
• Proposed a measurement correction calculation method.
• The range of correction coefficient values has been determined
• Blockage at inlet alters particle paths but not measurements.
• Investigated the effects of parameter variations on transient torque fluctuations.
The Coriolis force method is a recently developed and highly regarded direct measurement technique that enables high-precision measurement of bulk materials. The operational parameters and variations thereof directly influence the measurement accuracy of the equipment. In this study, a measurement correction coefficient is introduced to improve the calculation method for mass flow rate of the materials. The DEM is employed to simulate the motion of particle groups within the Coriolis force scale under different parameters, and the effects of various structural and operational parameters on the measurement results are compared. The research findings indicate that a lower rotational speed leads to more stable instantaneous measurement results, although the measurement error is relatively large. When the rotational speed exceeds 300 rpm, the measurement error remains within 15%. For materials with a radius of 1–2 mm, the variation range of precision error is approximately 0.4%. Among the structural parameters, the radius of the measurement wheel has the most significant impact on the measurement results, wherein a larger measurement wheel radius corresponds to a smaller measurement error. The horizontal angle of the blades follows as the next influential parameter, with a clockwise rotation and a horizontal angle of 30° resulting in a measurement error below 2%.
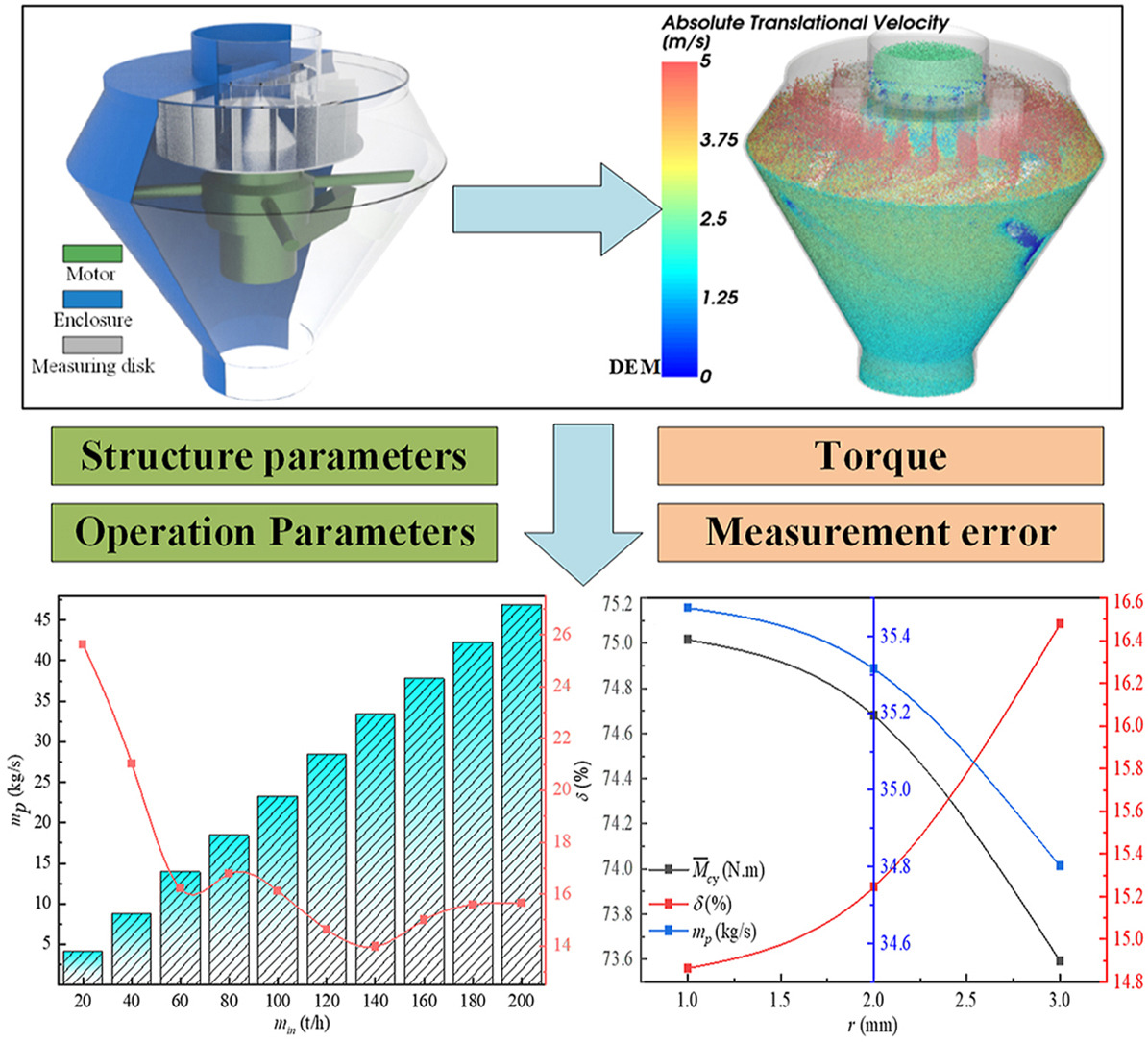