- Volumes 84-95 (2024)
-
Volumes 72-83 (2023)
-
Volume 83
Pages 1-258 (December 2023)
-
Volume 82
Pages 1-204 (November 2023)
-
Volume 81
Pages 1-188 (October 2023)
-
Volume 80
Pages 1-202 (September 2023)
-
Volume 79
Pages 1-172 (August 2023)
-
Volume 78
Pages 1-146 (July 2023)
-
Volume 77
Pages 1-152 (June 2023)
-
Volume 76
Pages 1-176 (May 2023)
-
Volume 75
Pages 1-228 (April 2023)
-
Volume 74
Pages 1-200 (March 2023)
-
Volume 73
Pages 1-138 (February 2023)
-
Volume 72
Pages 1-144 (January 2023)
-
Volume 83
-
Volumes 60-71 (2022)
-
Volume 71
Pages 1-108 (December 2022)
-
Volume 70
Pages 1-106 (November 2022)
-
Volume 69
Pages 1-122 (October 2022)
-
Volume 68
Pages 1-124 (September 2022)
-
Volume 67
Pages 1-102 (August 2022)
-
Volume 66
Pages 1-112 (July 2022)
-
Volume 65
Pages 1-138 (June 2022)
-
Volume 64
Pages 1-186 (May 2022)
-
Volume 63
Pages 1-124 (April 2022)
-
Volume 62
Pages 1-104 (March 2022)
-
Volume 61
Pages 1-120 (February 2022)
-
Volume 60
Pages 1-124 (January 2022)
-
Volume 71
- Volumes 54-59 (2021)
- Volumes 48-53 (2020)
- Volumes 42-47 (2019)
- Volumes 36-41 (2018)
- Volumes 30-35 (2017)
- Volumes 24-29 (2016)
- Volumes 18-23 (2015)
- Volumes 12-17 (2014)
- Volume 11 (2013)
- Volume 10 (2012)
- Volume 9 (2011)
- Volume 8 (2010)
- Volume 7 (2009)
- Volume 6 (2008)
- Volume 5 (2007)
- Volume 4 (2006)
- Volume 3 (2005)
- Volume 2 (2004)
- Volume 1 (2003)
• Variation of module configuration is suitable to modulate transport during planetary roller melt granulation.
• Material mixing promoted at higher free processing volume.
• Material mixing promoted at higher rotation speeds.
• Normalization of residence time distribution model parameters feasible.
• Aspects of fundamental transport mechanism revealed.
In comparison to the established twin-screw machines, the application of a planetary roller granulator for continuous operation of melt granulation is a promising alternative based on the unique process concept. An initial study focused on the material transport during processing as a key driver for the overall performance. Hereby, the impact of direct process parameters on the residence time distribution was the main objective.
These investigations are complemented in this study by considering the free processing volume, which is defined by the number of planetary spindles applied within a module. The impact on the processing conditions is evaluated with respect to the process setting in terms of feed rate and rotation speed.
The results highlight the potential of altering the underlying transport function in planetary roller melt granulation (PRMG) via the investigated direct process and equipment parameters. The impact of the feed rate is lower in comparison, while a higher rotation speed as well as a higher free processing volume promote material mixing. Moreover, a normalization of the determined residence time distribution (RTD) model data was feasible with respect to the process settings and the number of applied planetary spindles in the processing zone. This demonstrates the key role of the free processing volume in the fundamental mechanisms of material transport and mixing during PRMG.
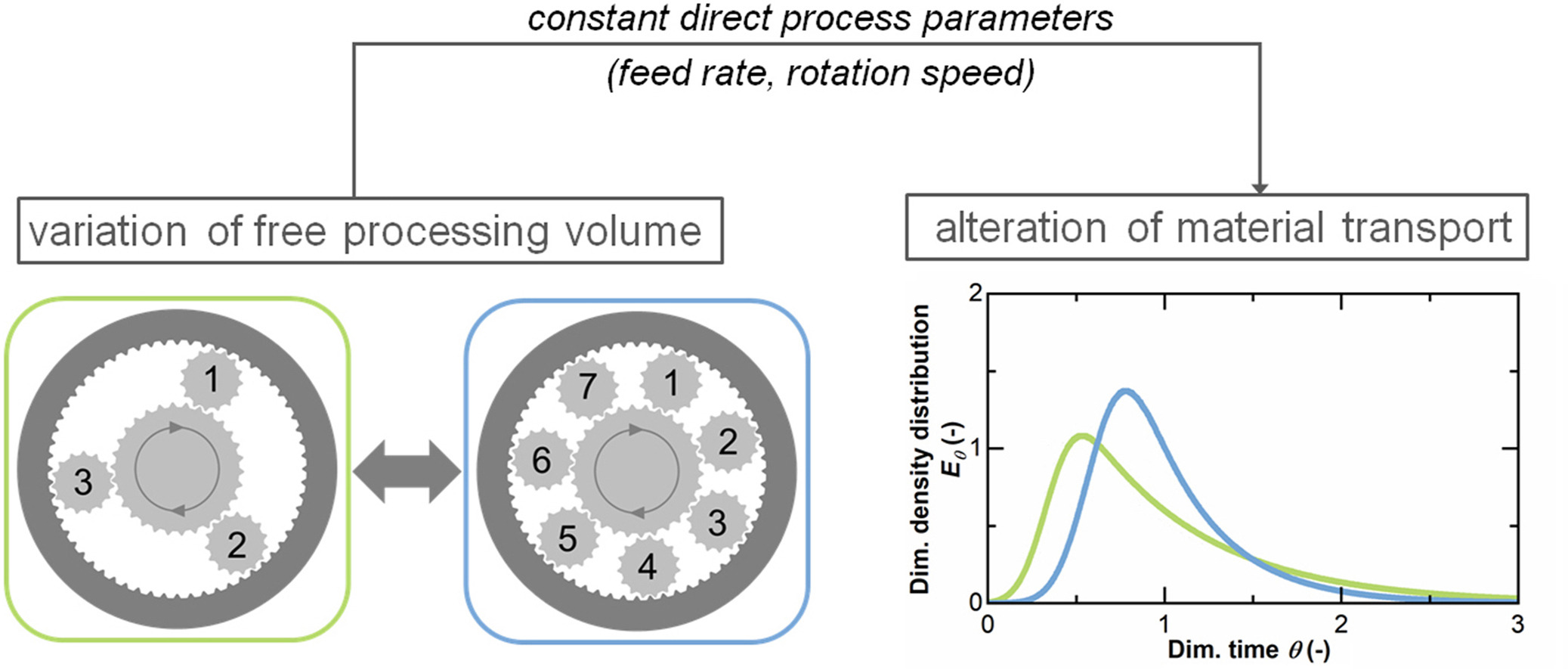