- Volumes 84-95 (2024)
-
Volumes 72-83 (2023)
-
Volume 83
Pages 1-258 (December 2023)
-
Volume 82
Pages 1-204 (November 2023)
-
Volume 81
Pages 1-188 (October 2023)
-
Volume 80
Pages 1-202 (September 2023)
-
Volume 79
Pages 1-172 (August 2023)
-
Volume 78
Pages 1-146 (July 2023)
-
Volume 77
Pages 1-152 (June 2023)
-
Volume 76
Pages 1-176 (May 2023)
-
Volume 75
Pages 1-228 (April 2023)
-
Volume 74
Pages 1-200 (March 2023)
-
Volume 73
Pages 1-138 (February 2023)
-
Volume 72
Pages 1-144 (January 2023)
-
Volume 83
-
Volumes 60-71 (2022)
-
Volume 71
Pages 1-108 (December 2022)
-
Volume 70
Pages 1-106 (November 2022)
-
Volume 69
Pages 1-122 (October 2022)
-
Volume 68
Pages 1-124 (September 2022)
-
Volume 67
Pages 1-102 (August 2022)
-
Volume 66
Pages 1-112 (July 2022)
-
Volume 65
Pages 1-138 (June 2022)
-
Volume 64
Pages 1-186 (May 2022)
-
Volume 63
Pages 1-124 (April 2022)
-
Volume 62
Pages 1-104 (March 2022)
-
Volume 61
Pages 1-120 (February 2022)
-
Volume 60
Pages 1-124 (January 2022)
-
Volume 71
- Volumes 54-59 (2021)
- Volumes 48-53 (2020)
- Volumes 42-47 (2019)
- Volumes 36-41 (2018)
- Volumes 30-35 (2017)
- Volumes 24-29 (2016)
- Volumes 18-23 (2015)
- Volumes 12-17 (2014)
- Volume 11 (2013)
- Volume 10 (2012)
- Volume 9 (2011)
- Volume 8 (2010)
- Volume 7 (2009)
- Volume 6 (2008)
- Volume 5 (2007)
- Volume 4 (2006)
- Volume 3 (2005)
- Volume 2 (2004)
- Volume 1 (2003)
• Carbide slag has great potential as a flux in the iron ore sintering process.
• Bonding effect of carbide slag can improve the permeability of the green bed.
• A proper amount of carbide slag helps generate excellent bonding phases in sinter.
• 75% of lime can be replaced by carbide slag, with little change in sinter quality.
• Utilization of carbide slag can achieve considerable CO2 emission reduction.
Limestone or quicklime is a necessary flux in the iron ore sintering process. Its production and application process will cause CO2 emissions and various environmental pollution, but this has not attracted enough attention. Carbide slag (CS) is a calcium-rich solid waste produced in acetylene production, the harmless disposal of which is still incomplete, resulting in soil and groundwater pollution. This study investigated the granulation characteristics and sintering performance of the sintering mixture with different proportions of CS. The results show that replacing limestone with an appropriate proportion of CS is promising and beneficial to the formation of high-quality bonding phase. When CS accounts for 75% of the total mass of CS and limestone, the tumbler index increases by 8.10% and the comprehensive index decreases only from 100 to 96.16, which is within the acceptable range. The application of CS in iron ore sintering can achieve a clean disposal of it and a considerable carbon emission reduction, as the main component of which is Ca(OH)2.
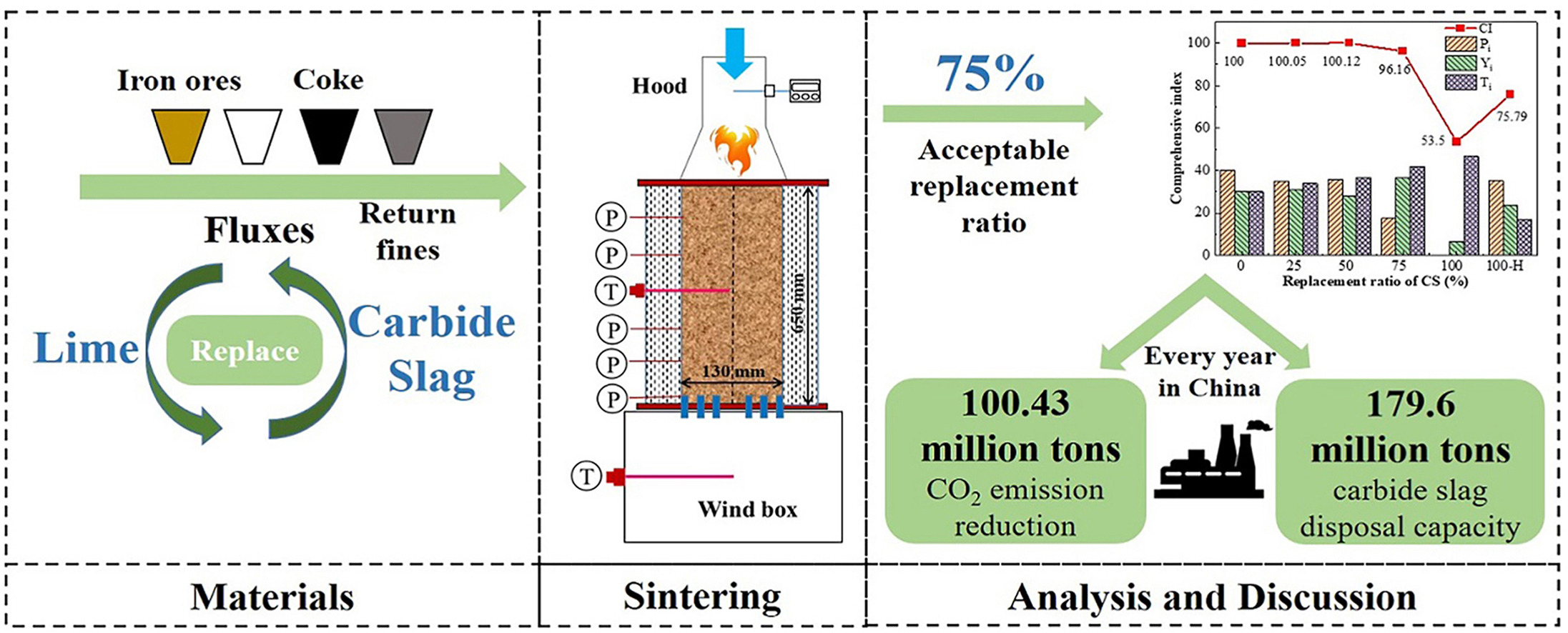