• Mixing speed of the composite conductive solution should be same as that of LIB slurry to disperse CB/Gr.
• LIB slurry has a better formed conductive network structure under the condition of 1200 rpm mixing speed.
• Well-formed conductive network structure and uniformed distributed conductive agent are appeared when 50min mixing time.
This paper proposed an optimal approach to disperse the composite conductive agent which is composed of carbon black (CB) and graphene (Gr) within lithium-ion battery (LIB) slurry with different mixing speeds and mixing times. The internal structures of LIB slurry are characterized by Electrochemical Impedance Spectroscopy, Scanning Electron Microscopy, and Raman experiment. Initially, a composite conductive solution is prepared by mixing the composite conductive agent with NMP solvent under the conditions of five different mixing speeds n1 (n1 = 1000, 1100, 1200, 1300, 1400 rpm) in the case of mixing time t1 = 10 min. Subsequently, LIB slurry is prepared by blending the composite conductive solution, LiCoO2 and PVDF-NMP solution under the conditions of five different mixing speeds n2 (n2 = 1000 ± 280, 1100 ± 280, 1200 ± 280, 1300 ± 280, 1400 ± 280 rpm) in the case of mixing time t2 = 6 min. By analyzing the internal structure of different LIB slurries, it shows that in the case of n1 = n2 = 1200 rpm, a conductive network structure is well formed within LIB slurry. Additionally, in order to determine the optimal time to prepare the composite conductive solution for LIB slurry, nine different t1 (t1 = 0, 10, 20, 30, 40, 50, 60, 70, 80 min) are selected. By analyzing the internal structure of different LIB slurries, a well-formed conductive network structure and a uniformly distributed composite conductive agent are deduced in LIB slurry when t1 = 50 min. Therefore, it can be concluded that the composite conductive agent composed of CB and Gr is able to be uniformly dispersed in LIB slurry by establishing a well-formed conductive network structure under the optimal mixing speed n1 = n2 = 1200 rpm and the optimal mixing time t1 = 50 min, t2 = 6 min. This kind of the internal structure has the potential to be used to further analyze the dispersion characterizations of LIB slurry under different composite conductive agent and CB/Gr ratios with the aim of improving the final performance of LIB.
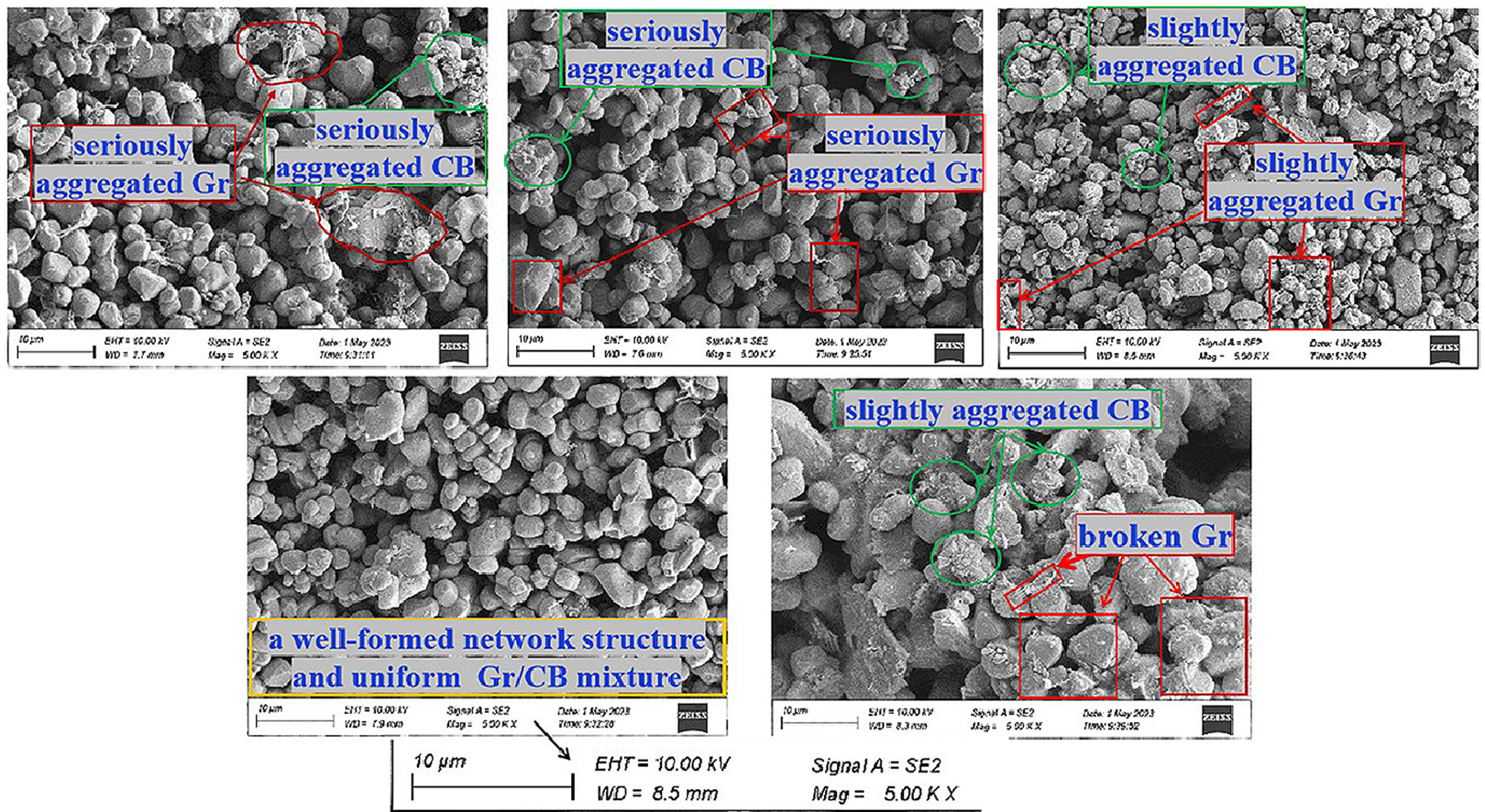