• Induration of iron ore pellets was investigated by coupled CFD-DEM.
• Transport phenomena for each pellet was addressed by a set of 1D radial equations.
• Model validation was carried out with pilot plant reactor.
• Heat and mass transfer were analyzed during the thermal cycle of induration process.
• Model was used to assess the relevance of process parameters.
Iron ore pellets are the main feedstock in ironmaking processes. While extensive research has addressed numerical modeling of the iron ore pellet induration process, little effort has been made to describe the intricate thermochemical processes occurring within the reactor starting from the pellet and particularly at the intra-particle scale. In this regard, discrete-continuous methods like CFD-DEM can generate more realistic, irregular particle assemblies, which leads to significantly more accurate predictions of voidage variation, wall effects, temperature distribution, and associated mass transfer phenomena. This study presents a numerical model based on computational fluid dynamics (CFD) coupled with the discrete element method (DEM) to simulate the thermal induration process of iron ore pellets. The presented model solving heat, mass, and momentum conservation equations for both continuous and discrete phases, provides detailed information on the thermochemical aspects of the process. Pilot-scale induration experiment was conducted to validate model predictions in terms of thermal history and final conversion fraction. It was found that inlet charge specifications, such as particle and pellet size, significantly impact the productivity of pelletizing plants, highlighting the potential of the presented model to optimize the process and improve plant productivity.
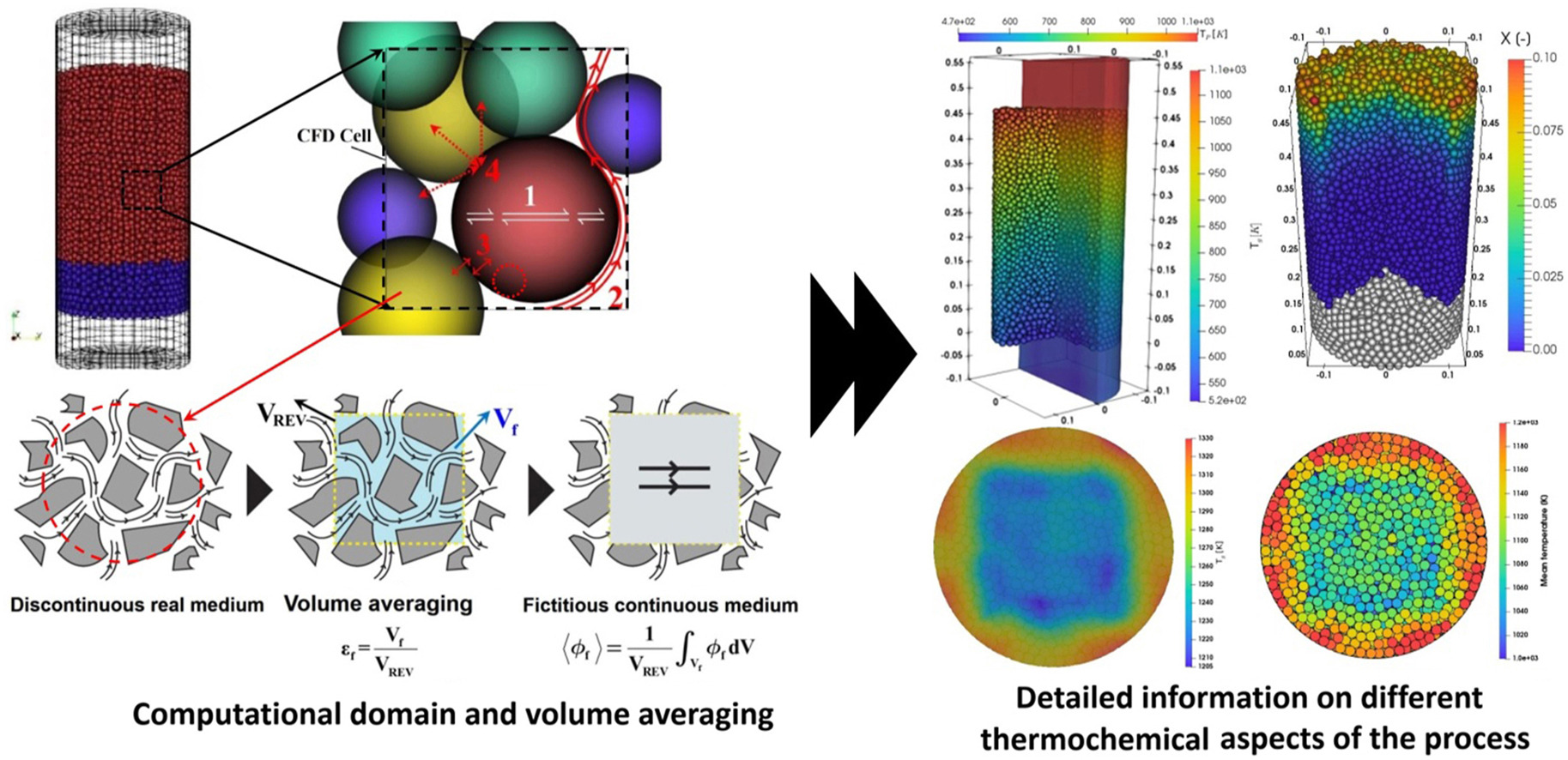