• Modeling multi-zone polymerization reactor by coupling hydrodynamic and population balance equations.
• Utilization of two-fluid model to simulate the hydrodynamics.
• Investigating impact of operating conditions and design parameters on reactor performance.
• Effect of hydrodynamic conditions on particle size distribution is shown.
This research focuses on modeling a multi-zone circulating reactor (MZCR) in the polypropylene production process. In these reactors, designed for polyolefin production, small catalyst particles (20–300 μm) initiate polymerization in the presence of monomer gas. The reactor consists of two main regions: the riser and the downer. The riser operates in the fast fluidization and the downer is in the moving bed regime. Employing the two-fluid model with the Eulerian-Eulerian approach, the dynamics of both solid and gas phases were modeled by applying Newton's laws of motion and assuming spherical particles. The population balance of particles within the reactor was also coupled with the equations of motion. The simultaneous solution of these equations provides valuable insights into particle and fluid behavior, revealing trends such as the growth of polymer particles. Furthermore, the impact of various operating conditions was explored. This study also examined the effects of design parameters (gas inlet velocity, average inlet diameter, and temperature) on the system performance. For instance, it was shown that in the case where the solid circulation flux is 30 kg/(m2 s) the velocity of particles in the bed increases from 0.4 at the inlet to 1.1 m/s in the fully developed zone, when it is 43 kg/(m2 s) the velocity of particles increases from 0.3 to 1.4 m/s, and when it is 55 kg/(m2 s), it is increased from 0.22 to 1.5 m/s. Additionally, trends in particle size distribution based on temperature adjustments were revealed. This study showed that higher temperatures accelerate the polymerization reaction rate, promoting faster growth kinetics and the formation of larger particles.
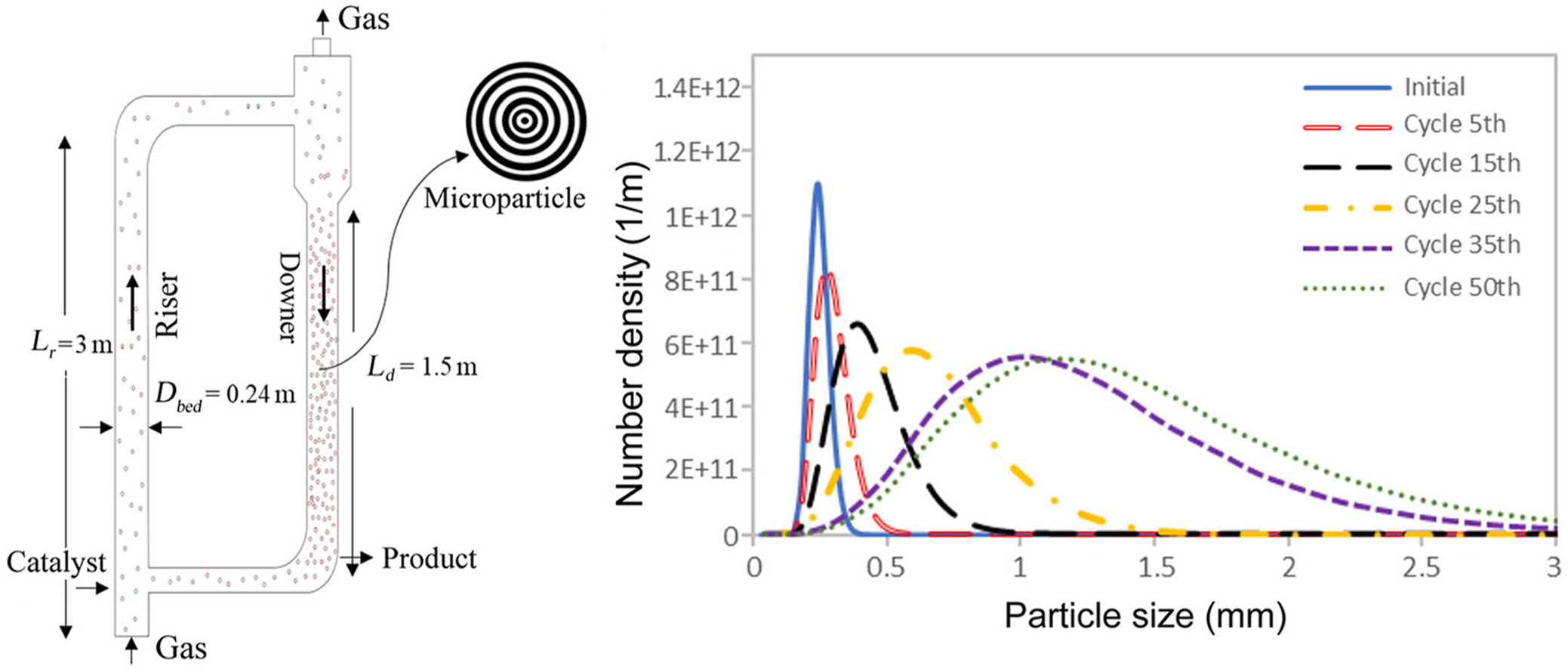