• Novel method for continuous coating of powders using foam.
• New continuous powder coating assessment method for foams and liquids.
• Image analysis proves coating quality is optimal when using foam.
• Scaling up has minor effect on coating quality.
• Coating quality depends on rheological properties of the coating liquid.
Coating with viscous formulations has been essential in numerous industries as it can be a means for providing functionalization, additional properties, as well as other benefits. However, there have been scarce studies that have investigated and proposed methodologies in literature. Continuous coating of powders with viscous liquids poses as a promising technology, which has been mentioned in some studies, but has not yet been thoroughly investigated. This paper employs the use of image processing and analysis, in combination with statistical analysis of particles to evaluate the effectiveness of foams and liquids as a means of coating powder beds. Two different sizes of twin screw mixers that are working in continuous operation are employed, and a new continuous foaming device is fabricated and used for the experiments of coating. The effect of materials and process parameters (as for example rotational speed, and flowrate) on the quality of coating are investigated. Image analysis is used to assess the coating quality. The results clearly showcase the potential of using twin screw mixers for coating purposes and not only for mixing. The hypothesis that using large bubble foams to improve the coating of viscous liquids on particles is proven correct, as they provide higher quality coatings compared to their equivalent liquids, when used in the twin screw mixer. Surprisingly, using a larger scale twin screw mixer, does not show a substantial effect on the mixing, regarding quality, however there is still a requirement for mix optimization for achieving scale-up of this process. These results provide a new pathway for coating powders with viscous formulations in industrial applications, requiring less energy and effort in this process, and can pave the way towards introducing more sustainable industrial methodologies for coating.
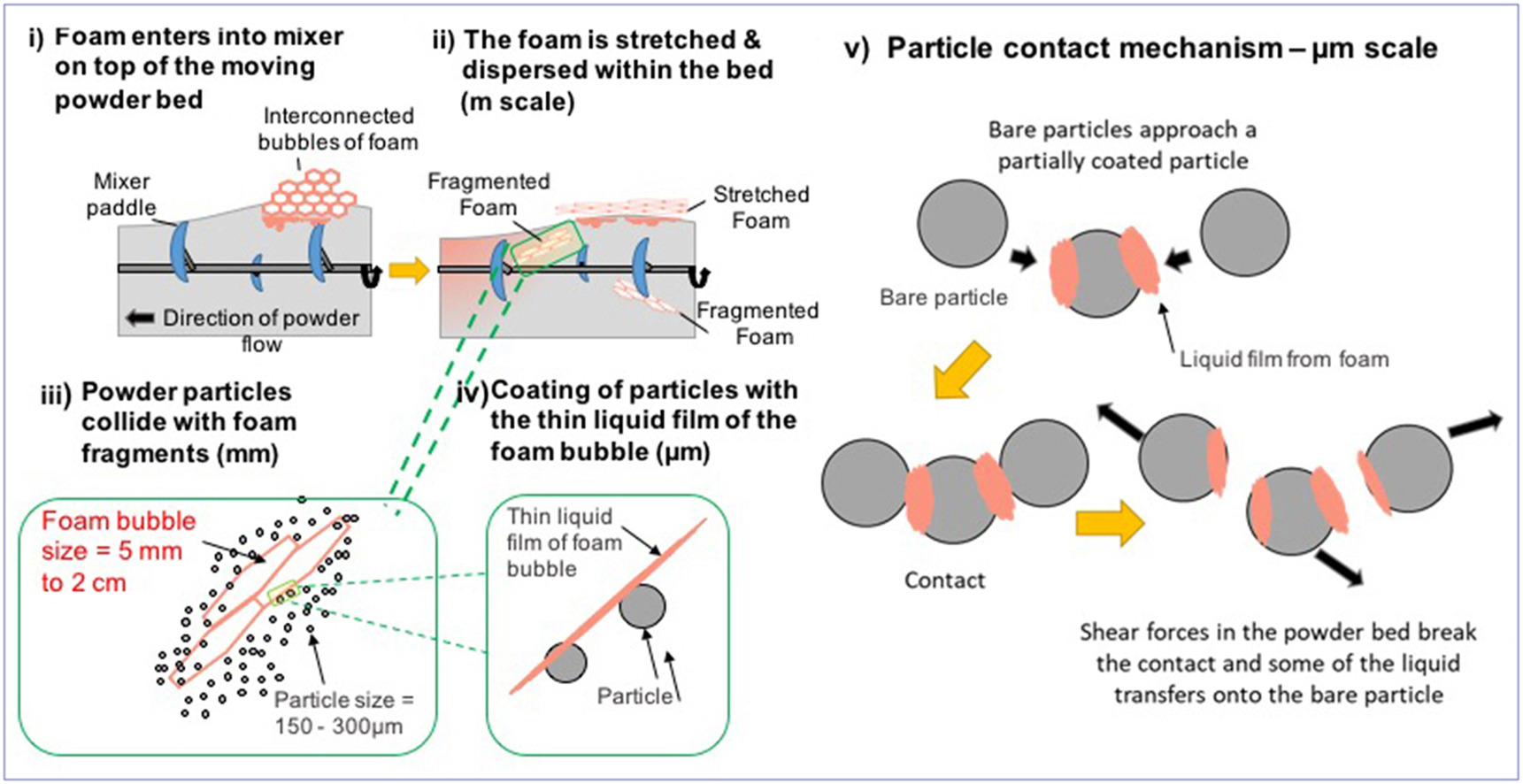