• Gas and multiphase flow under different pressures were analyzed by modeling.
• Atomization experiments and characterization of powders for additive manufacturing were performed.
• Experimental validation provided support for the predictive accuracy of the model.
• Synergistic effect mechanism of particle size and morphology was revealed.
• This study provides theoretical support for precise control of superalloy powders.
The particle size and morphology of superalloy powders are crucial parameters that significantly influence the performance of additive manufacturing (AM) processes. This study investigates the effects of atomization pressure on these characteristics through a combination of computational fluid dynamics (CFD) simulations and vacuum induction melting gas atomization (VIGA) experiments. The CFD simulations revealed that increasing the atomization pressure from 2.0 MPa to 3.5 MPa resulted in a rise in maximum gas velocity from 526 m/s to 537 m/s and a reduction in median particle size (D50) from 60.9 μm to 37.5 μm. Subsequent experiments demonstrated a decrease in D50 from 52.9 μm to 35.6 μm, and sphericity from 0.9432 to 0.9377, as pressure increased. The particle size results of the atomization experiments and numerical simulations show strong consistency, validating the accuracy of the numerical simulation results. The volume of hollow particles also increased slightly in specific size fractions. These results suggest that higher atomization pressures produce finer powders with lower sphericity, but also promote particle adhesion, reducing the overall refinement effect. This study provides insights into optimizing atomization conditions for the precise control of superalloy powders in AM.
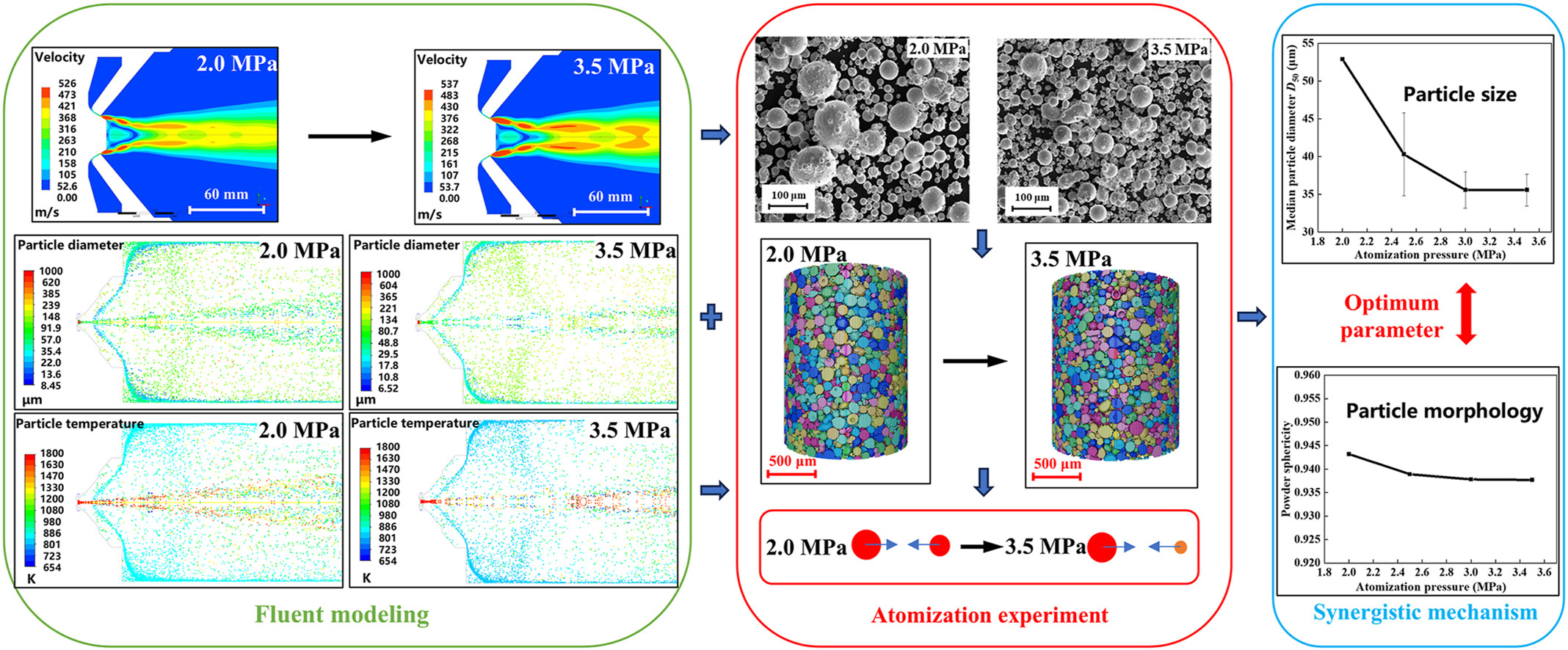
Superalloy powders; Additive manufacturing; Atomization pressure; CFD modeling; Particle size; Morphology