• Computational particle fluid dynamics (CPFD) is used to numerically simulate auxiliary intake pipe.
• Response surface method is used to optimize the structural parameters.
• Auxiliary intake velocity has the biggest impact on the two goal values.
• The goal value is most affected by the mix of intake speed and spacing length.
• Adding auxiliary air intake can reduce the power consumption coefficient.
Computational particle fluid dynamics (CPFD) approach is used to simulate a horizontal tube with an extra air intake. To determine the optimal values for the two objectives, a one-factor hill-climbing test is performed on three structural parameters of the auxiliary air intake (intake velocity, intake angle, and distance between two neighboring valves) and two objective values (operating time and power consumption coefficient). In this paper, a multi-objective optimization of the three structural parameters has been carried out using the response surface methodology and designing a multi-group central test. It was discovered that when the main air intake speed was 3 m/s, adding an auxiliary air intake with an intake speed of 5 m/s, an intake angle of 45°, and a distance of 1900 mm between the two adjoining valves improved particle evacuation. When compared to the situation with a main air intake speed of 5 m/s and no auxiliary air intake, the working time is reduced by 4.97%, and the power consumption coefficient is reduced by 33.51%.
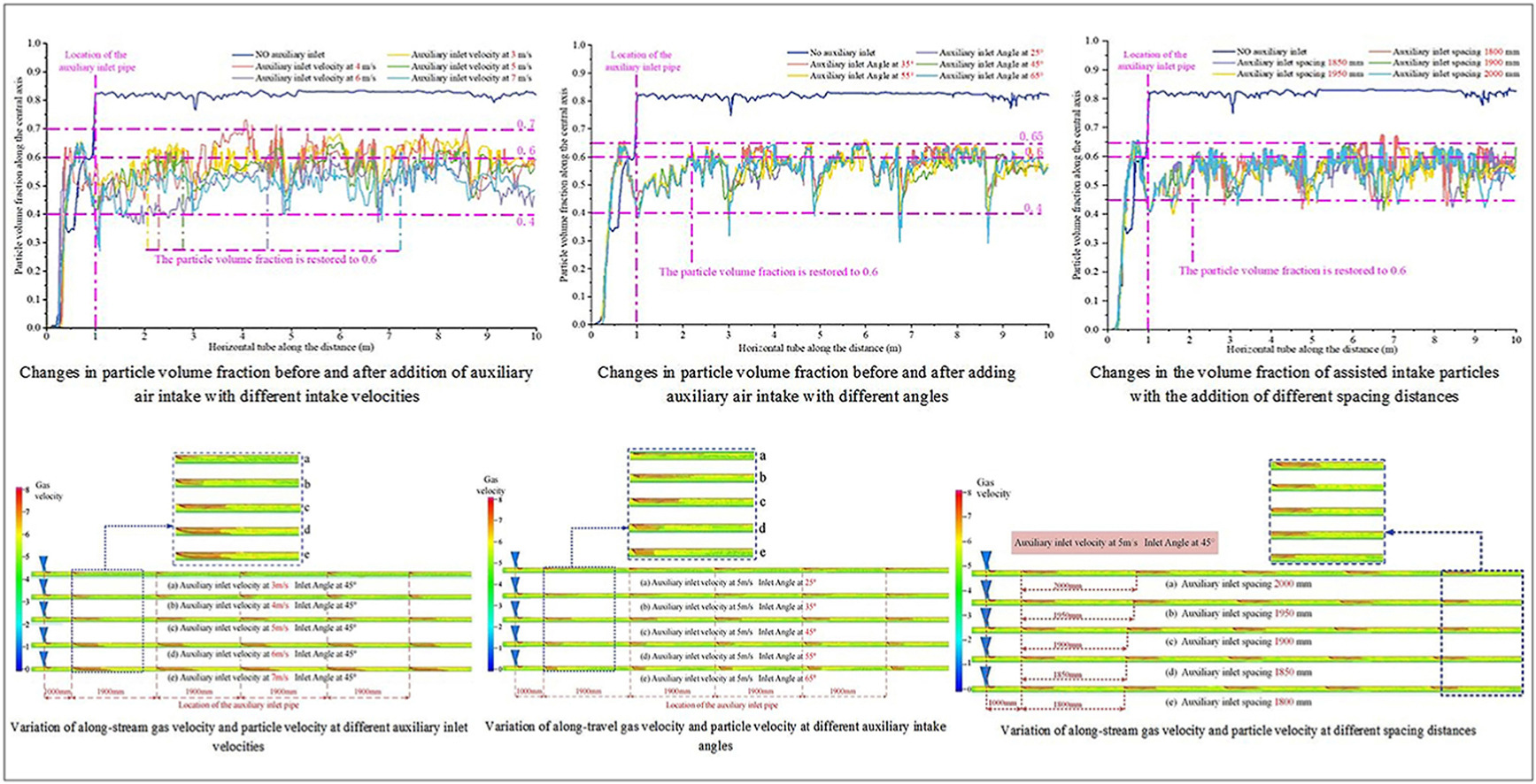