• Investigated the behaviour of recoating blades in continuous binder jet additive manufacturing.
• Analyzed blade motion in circular and helical patterns for surface quality assessment.
• Conducted Discrete Element Method (DEM) simulations with various blade shapes.
• Employed reverse calibration to accurately match sand material parameters.
• Optimized blade shape from normal to achieve full disc printing.
Binder jet additive manufacturing is used for producing molds and cores for sand casting, by using granular material and proper binder. The conventional system uses a layer-by-layer gantry motion. The new continuous printing machine is a helical motion system. It includes a recoating blade for the granular material which has been investigated. This study focuses on analysing the behaviour of the recoating blade when it moves in a circular or the helical motion, as well as assessing the quality of the layer surface. Discrete Element Method (DEM) simulations was conducted using various blade geometry, and the results were compared with experimental models. The input parameters of the sand material were calibrated using a reverse calibration model, which iteratively adjusts the parameter values until they match the bulk response observed in real experiments. This research study employed experimental testing and DEM modeling, initially using a normal blade to produce an annular disc, and then optimizing the blade shape to achieve full disc printing.
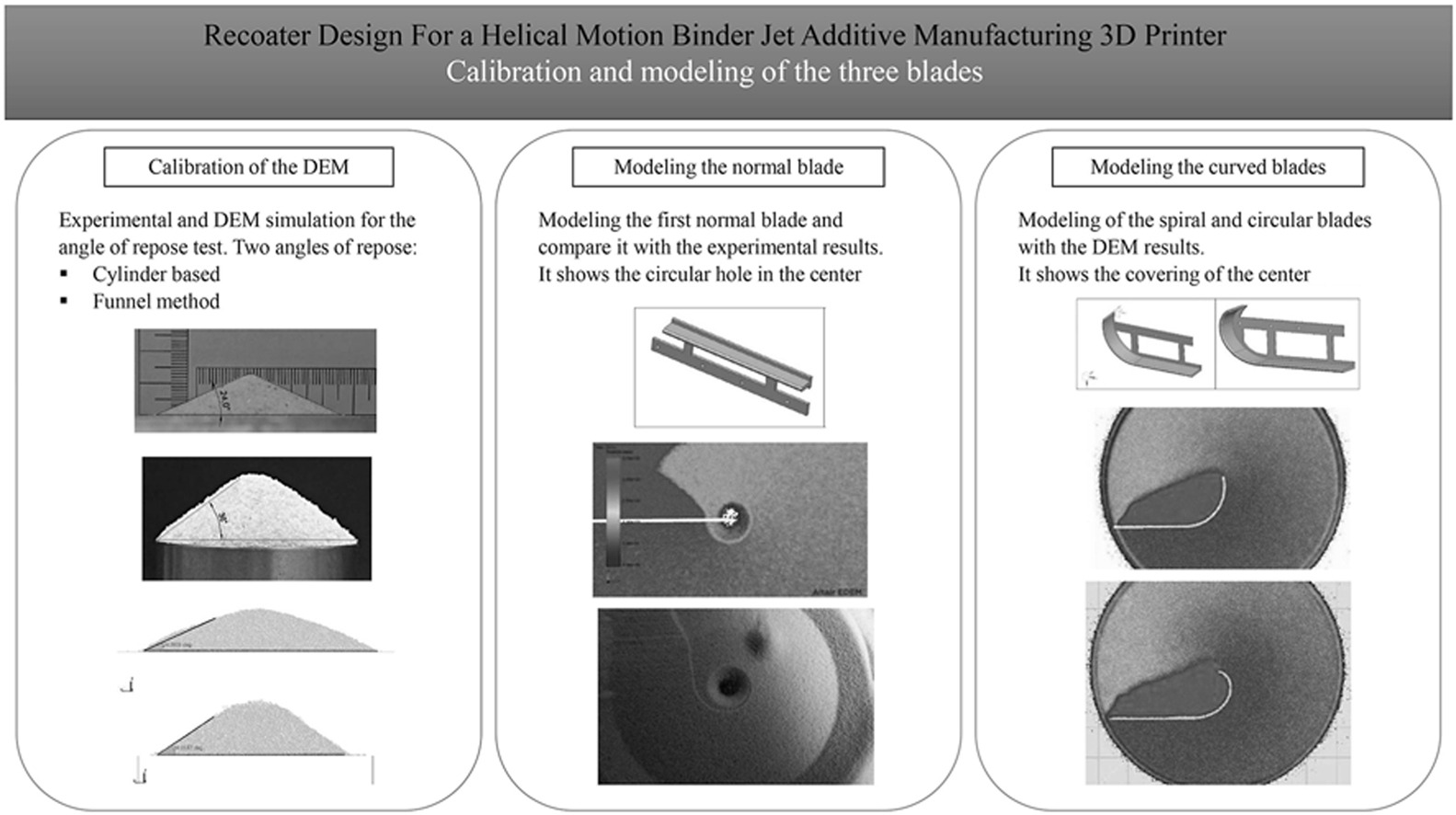