• Oxalic acid can be reused in several successive leaching experiments.
• The desired reaction is essentially completed within 2 min of calcining.
• The method of direct acid leaching after calcination is used without admixtures.
Limited research is available on lithium extraction technology for clay-type lithium deposits with relatively low lithium content. In this study, we investigated the effects of lithium extraction from lithium-poor clay ores using oxalic acid. The ore was first calcined and then fully mixed with solid oxalic acid powder, followed by water leaching. Raw material analysis revealed that the primary lithium-containing mineral was cookeite, with a lithium oxide content of 0.57%. The X-ray diffraction (XRD) patterns of the mineral phase before and after calcination at different temperatures revealed that the structure of the ores calcined at 300 and 400 °C was similar to that of the original ore. However, in the XRD patterns of the ore calcined at 500 °C, certain characteristic peaks of cookeite weakened or disappeared. Upon calcination at 600 °C, the hydroxyl group of cookeite was removed, amorphous phase of cookeite appeared, and maximum leaching yield was attained. Using response surface methodology optimization, the optimal calcination temperature and time; acid-to-ore and water-to-ore ratios; and reaction temperature and time were 600 °C and 2 min; 1:1 and 4 mL/g; and 95 °C and 6 h, respectively. The leaching yield under these optimal conditions was 92.33%. The results of this study revealed that lithium ions could be effectively extracted from mines using oxalic acid.
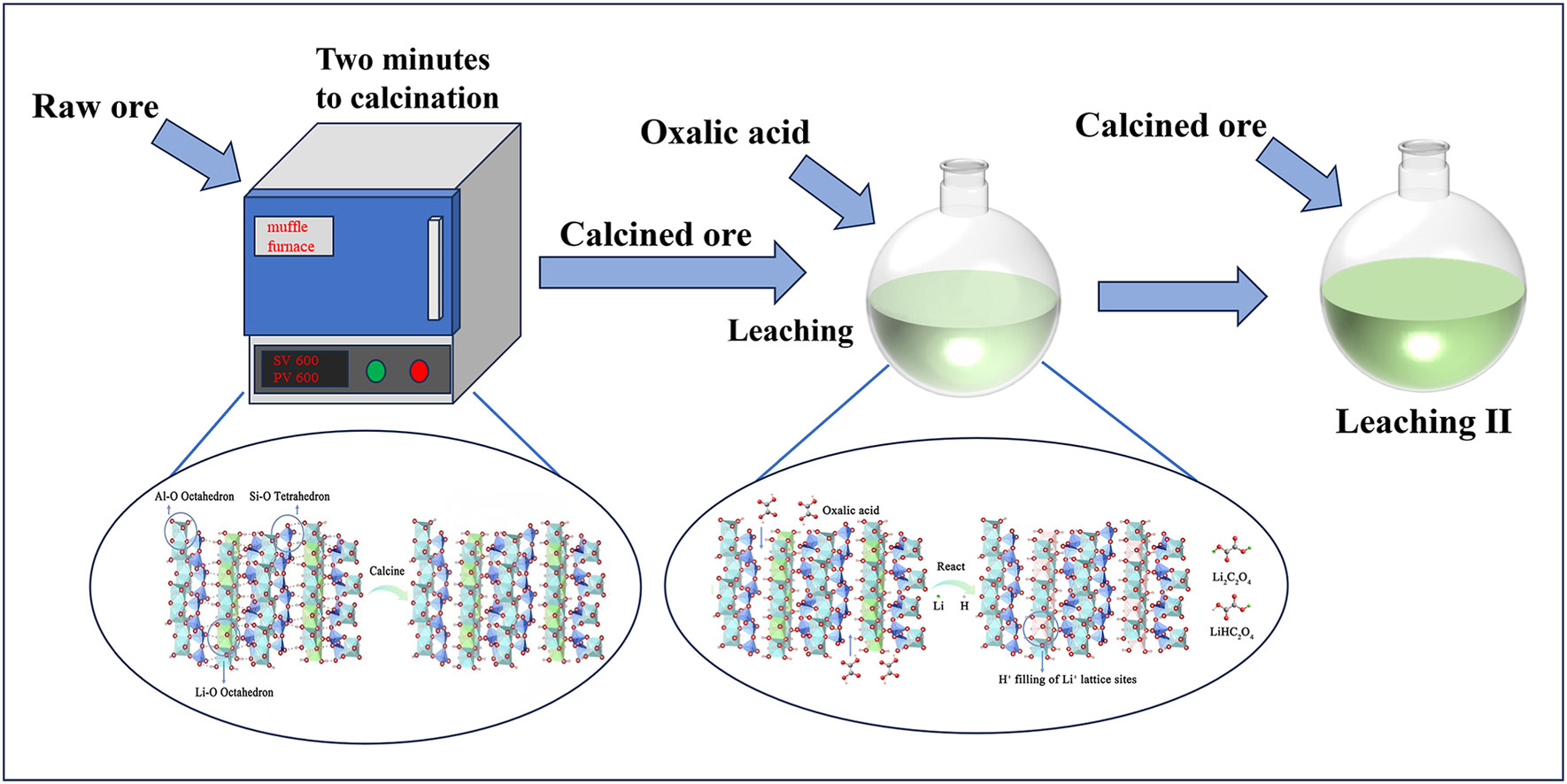