• The numerical model's accuracy in predicting transport dynamics was validated through indoor experiments.
• Developed a field-scale numerical model to simulate the transport of temporary plugging balls in horizontal wells.
• Identified parameters influencing the distribution of temporary plugging balls in the wellbore by sensitivity analysis.
This study explores the transport dynamics of temporary plugging balls in multi-cluster horizontal wellbores through a three-dimensional Computational Fluid Dynamics (CFD) model based on field dimensions. An experimental setup mimicking the transport of these balls was utilized to validate the model, revealing a maximum discrepancy of less than 22.2% in ball allocation proportions under identical conditions. This validation substantiates the model's precision in predicting transport dynamics across various operational scenarios. Key parameters, including pump rate, fluid viscosity, perforation discharge capacity, ball diameter, ball density, and the number of balls, were examined using the validated model. Findings indicate that pump rate, ball density, and perforation discharge capacity markedly influence ball distribution, followed by fluid viscosity. The number of balls has a lesser effect. Elevated pump rates augment inertial forces, prompting balls to migrate towards the toe-side of the wellbore. Moderate fluid viscosities enhance distribution uniformity, whereas extreme viscosities do not. Perforation clusters with higher discharge capacities attract more balls, thereby improving plugging efficiency. Lower ball density and smaller diameter yield more uniform distribution, while higher values lead to ball accumulation at the toe-end. This study offers valuable insights for optimizing parameters in temporary plugging fracturing technology, thereby improving the efficiency and effectiveness of hydraulic fracturing treatments.
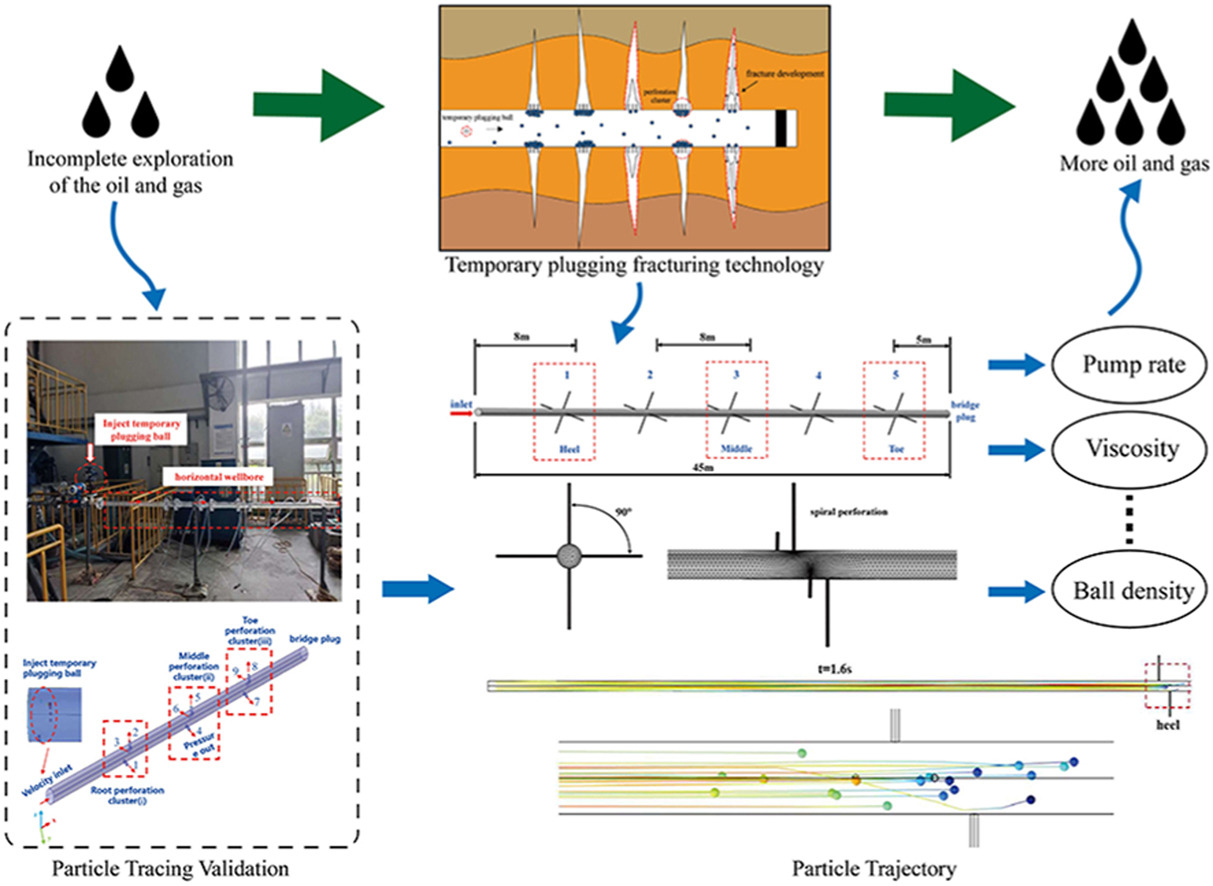