• Black mass is raw material for leaching instead of cathode powder.
• Research work performed at pilot scale instead of lab.
• For filtration centrifuge filter system is used.
• Economical process for recycling of LFP batteries.
• Graphite recovered with 93% carbon.
The rapid growth of the electric vehicle market has led to an unprecedented demand for lithium iron phosphate (LiFePO4) batteries, renowned for their exceptional safety, performance, and environmental benefits. However, the escalating volume of spent LiFePO4 batteries poses significant environmental and resource challenges. To address these concerns, this study develops an innovative industrial-scale recycling process utilizing centrifuge filtration to recover graphite assisted hydrometallurgy for efficient recovery of lithium, iron and phosphorus from LiFePO4 black mass powder (cathode powder + graphite). Hydrometallurgical acid leaching of LiFePO4 black mass powder is optimized under following conditions; 1.2 M sulfuric acid, 5% hydrogen peroxide, 100 g/L pulp density at 60 °C for 180 min reaction time in a 500 L reactor at pilot plant scale, achieving 99.7% lithium extraction efficiency and 93.5% fixed carbon in graphite residue. Metal composition and crystal structure were all revealed by extensive characterization utilizing atomic absorption spectroscopy (AAS), scanning electron microscopy (SEM), inductively coupled plasma optical emission spectroscopy (ICP-OES), x-ray diffraction (XRD) and particle size analyzer. This research provides a ground-breaking recycling pathway for LiFePO4 batteries, at pilot scale, promoting sustainable resource management, mitigating environmental risks, and supporting the circular economy. By leveraging centrifuge filtration-assisted hydrometallurgy, the recycling industry can efficiently recover valuable materials, reduce waste, and contribute to a more sustainable future.
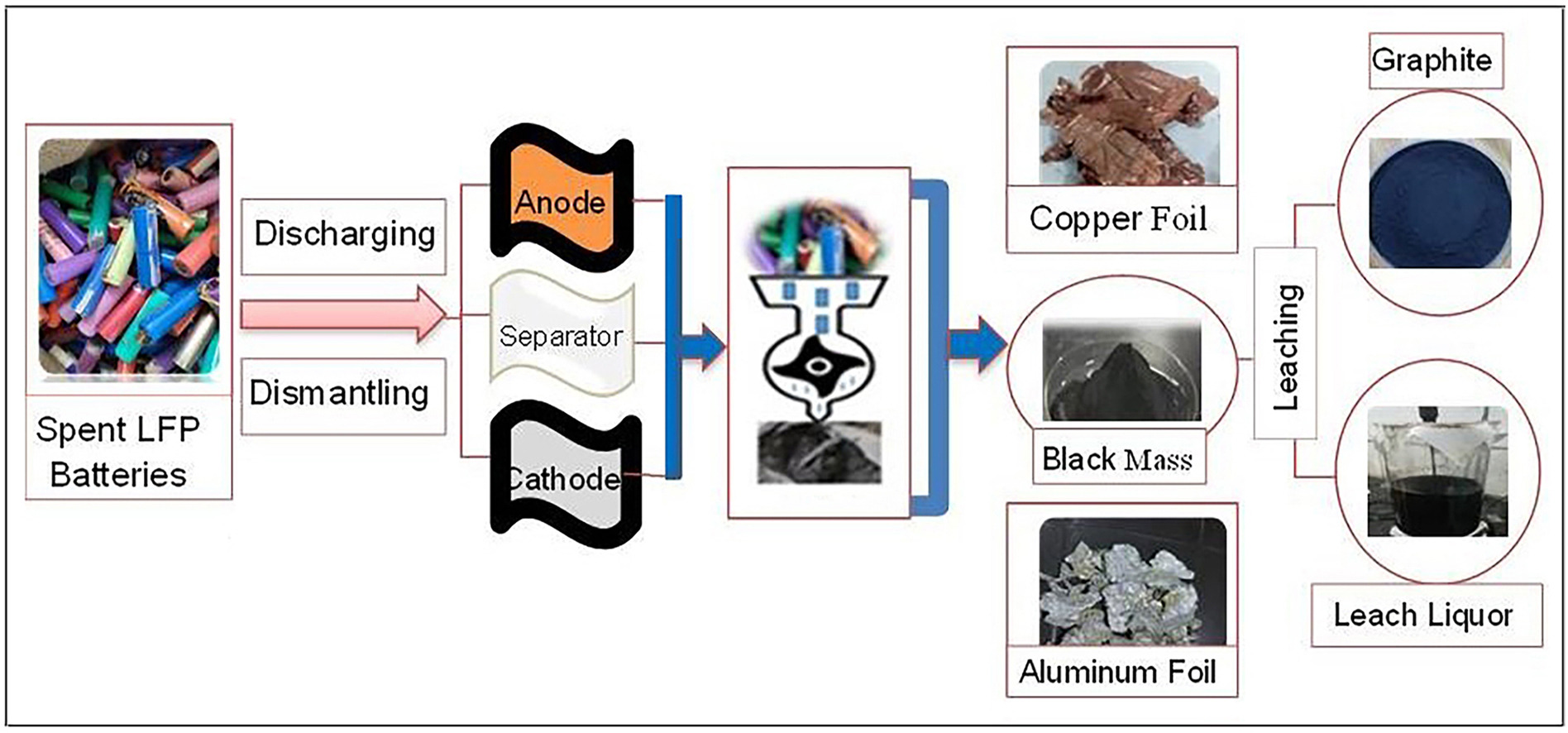