• DEM simulations are conducted to investigate the edge effect of HPGR mills.
• Edge effect is most significant to particle size, followed by particle-roll force and the least to throughput.
• Edge effect is enhanced/reduced by roll thickness and diameter but not grinding pressure.
• A unified equation is proposed for the different profiles of mill properties.
High pressure grinding rolls (HPGR) mills are an energy efficient comminution device widely used in the cement and mineral processing industries. Uneven roll wear and particle breakage near edges causes significant variation in grinding pressure along the axial direction. This study aimed to quantify the edge effect on mill performance through discrete element method (DEM) modelling. The DEM model, coupled with a multi-body dynamics (MBD) model for the motion of the floating roll and a particle fracture model, was calibrated and validated by the experimental data from a lab-scale HPGR mill. The simulations showed that the edge effect had the most significant impact on particle-particle compressive force and product size (characterised by the median particle size d50), followed by particle-roll force, and the least on throughput. Increasing roll length amplified the edge effect, causing larger variations in throughput, particle-roll force, and product size, while increasing roll size mitigated the edge effect, resulting in a more uniform product sizes and particle-wall interaction. On the other hand, varying grinding pressure had a minimal impact on the edge effect. A unified equation was proposed to quantify changes from parabolic to trapezoidal profiles. The proposed unified equation offers a new approach to predict changes in the wear and particle size profiles.
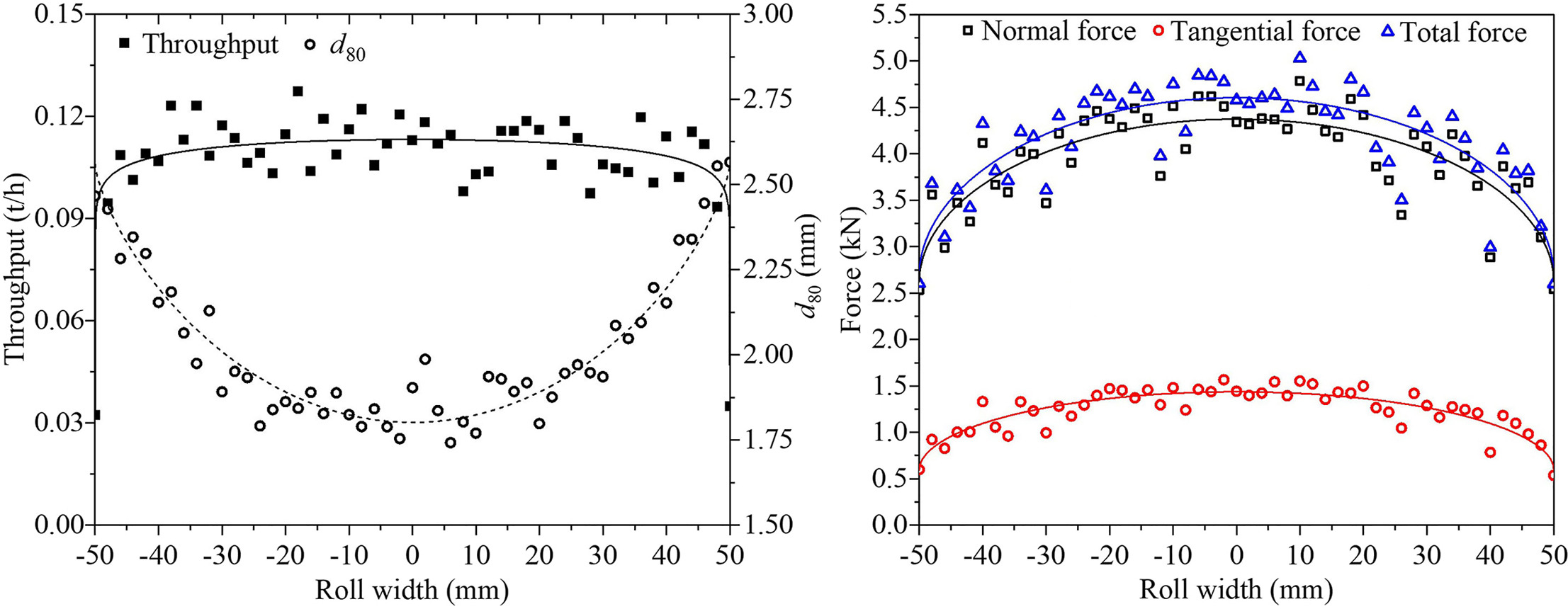